Keywords: NMC, Polyvinylidene fluoride, Cathode powder, Powder rheology, Dry electrode powder
RH136
Abstract
Optimization of electrode manufacturing for lithium-ion batteries has been increasingly focused upon due to inefficiencies and environmental concerns surrounding traditional slurry electrode processing methods. To eliminate the pitfalls of utilizing a slurry there has been an effort to use dry powder coating techniques. While this eliminates the cost, time, and environmental concerns associated with using a solvent, dry powder coating does present additional challenges in powder handling and processing. In this application note the new TA Instruments™ Powder Accessory is utilized to characterize powder bulk shear and flowability properties of a lithium nickel manganese cobalt (NMC) cathode powder with different ratios of carbon black and polymer binder. The powder cohesion, unconfined yield strength, flow function and total flow energy were characterized to provide formulation and scale-up insight. Thermogravimetric analysis (TGA) is utilized as a facile technique to identify binder content in the powder. Scanning electron microscopy (SEM) in conjunction with energy dispersive spectroscopy (EDS) ties the bulk properties of the powder to the underlying microstructure that affects the specific powder shear and flow behavior. The results show that altering the polymeric binder content influences the interparticle interaction and subsequent bulk shear and flow properties.
Introduction
As lithium-ion batteries (LIBs) have emerged as the most prominent energy storage solution, the manufacturing processes behind their design have come into focus [1]. A costly and timeconsuming segment of battery manufacturing is the fabrication of the electrodes. The components of the electrode are mixed with a solvent to form a slurry, which is then coated and dried onto a metal foil current collector. This solution-based process allows for adequate mixing to produce a uniform electrode coating in a large-scale roll-to-roll process, but the use of solvent adds time and cost to the overall electrode manufacturing. The drying and solvent recovery accounts for over 40% of the overall energy consumption and a significant portion of the cost. Second, the drying steps required to remove the solvent create additional time added to the manufacturing process [2]. Additionally, solvent, especially for cathode fabrication, is generally an environmentally toxic organic solvent, such as N-Methyl-2-pyrrolidone (NMP) [3].
Based upon the above considerations, there have been efforts to implement dry powder coating processes to fabricate LIB electrodes. As a result, powder properties are critical to the manufacturing process. Flowability is important for transporting powder in scale-up and production and the cohesion of the powder impacts coating uniformity. The dry powder coating process involves mixing the active electrode components with a polymeric binder in the dry powder state. The mixed electrode powder is then applied to a metal foil and a combination of temperature and pressure is utilized to adhere the powder electrode to the substrate. During this process, the powder will be under compression and shear. This dry electrode process reduces the time and cost associated with using solvent and is a more cost-efficient process compared to using a slurry precursor [3].
One of the most widely used cathode materials is lithium nickel manganese cobalt (NMC). This is largely due to its high energy density and long cycle life compared to other cathode materials [4]. The amount of NMC loading in the cathode material is critical for the battery energy density. In this note, the powder rheological properties of a fixed content of NMC based cathode powder will be analyzed. The NMC is mixed with differing ratios of carbon black (CB) and polyvinylidene fluoride (PVDF) binder. These components were varied as the CB contributes a conductive network to the system while the PVDF provides a physical network for adhesion to the substrate. The interplay between these two network functions must be understood to optimize the electrode design. With PVDF’s insulating properties, high PVDF content can result in an insufficient conducting network where battery performance will suffer. On the other hand, lack of PVDF binder can have detrimental effects on the electrode’s coating properties during processing. Optimizing the amount of PVDF binder and carbon black with the active NMC cathode material is essential for final performance of the electrode.
In this note, powder NMC samples mixed with varying amounts of CB and PVDF are investigated to explore impacts on powder flowability and provide insight into powder processing conditions. The powder shear and flow properties are explored using TA Instruments Powder Rheology Accessory. Scanning electron microscopy (SEM) and thermogravimetric analysis (TGA) are also used to correlate the powder properties with the microstructure and PVDF content, respectively.
Experimental
The mixed cathode powder samples were procured from SpectraPower, LLC (Livermore, CA) and composed of NMC811, carbon black, and PVDF binder. Three powders were utilized for testing with weight ratio compositions of 96:3:1, 96:2:2, and 96:1:3 for NMC:CB:PVDF.
Powder rheology testing was performed on the TA Instruments HR-30 performance rheometer using the powder shear and flowability accessories. Shear experiments were performed per ASTM D7891, with a 9 kPa pre-shear consolidating stress with subsequent shear steps at 7, 6, 5, 4, and 3 kPa consolidating stress [5]. The powder flowability experiments were conducted at a rotor tip speed of 100 mm/s. Analysis was performed in TRIOS™ Software using the automated powder analysis software feature. Additional details of powder testing and analysis can be found in TA Instruments application notes RH123 and RH126 [6] [7]. The PVDF content in the cathode powder was confirmed using the TA Instruments Discovery™ TGA 5500 where a temperature ramp from ambient to 1000 °C was performed at a heating rate of 20 °C/min. Particle size, shape, and surface morphology of the powder was investigated by SEM using a Phenom™ XL benchtop SEM by Thermo Fisher. The powder was prepared on double-sided carbon tape and imaged at a 5 kV accelerating voltage.
Results and Discussion
Thermogravimetric Analysis
The composition of the formulation is critical for electrode function and final battery performance. The TGA results are shown in Figure 1. The first step at approximately 490 °C corresponds to the initial PVDF decomposition and the second step can be attributed to PVDF decomposition confined at the polymer-ceramic interface [8]. The weight change to 99, 98, and 97% confirms a 1-3 wt% PVDF content, respectively.
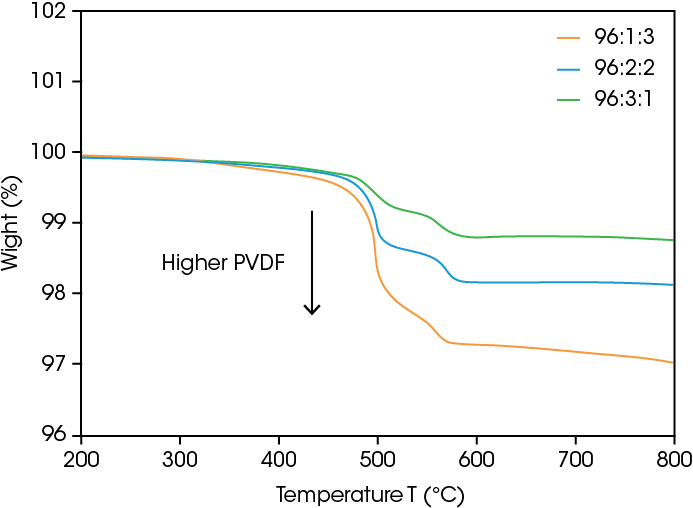
Scanning Electron Microscopy
To correlate the microstructure to the rheological properties SEM was used along with Energy Dispersive Spectroscopy (EDS). Figure 2 shows SEM images of 1-3 wt% PVDF in a-c, respectively. At low PVDF content, the surface of the NMC particles is rough (micron size protrusions). As the PVDF content increases the surface becomes smoother. A polymeric coating will appear smooth compared to inorganic particles when imaged at low kV with no additional coating.
Figure 2d shows an EDS map of the 3 wt% PVDF content powder. The yellow signature is the carbon Kα line. The strong carbon signal from between NMC particles identifies PVDF bridging. The extraneous carbon signals are from the CB along with additional PVDF coating and manifest as the carbon signals in smaller particles. While the PVDF is important for binding purposes, excessive particle coating is not desirable as it does not contribute to the conducting network of the CB. The surface coverage of PVDF on NMC reduces the active sites available on the cathode and will ultimately place a limit on the battery performance.
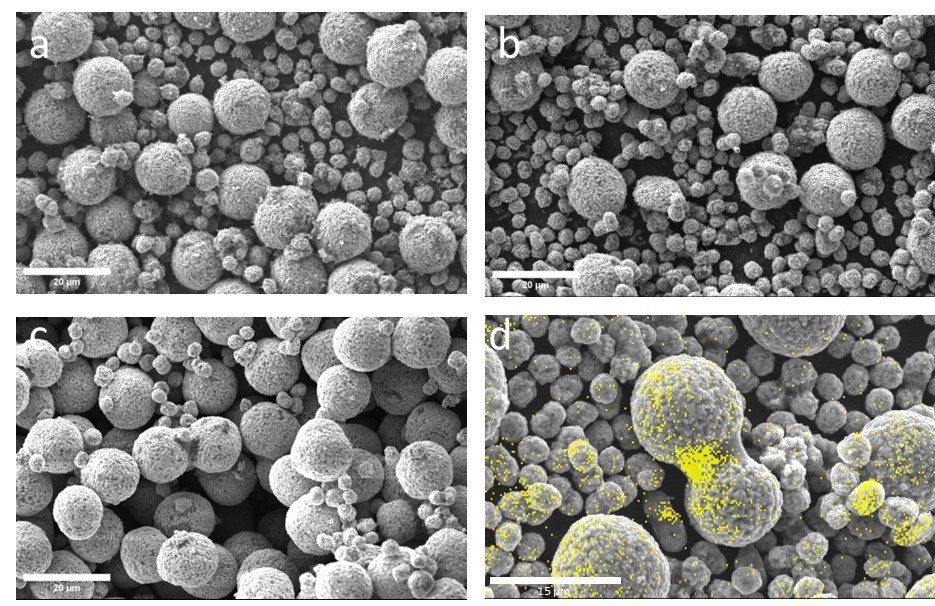
Powder Shear
Powder electrode processing includes feeding raw materials into processing equipment, then mixing the powder and dry coating the electrode with powder under shear. Powder cohesion and flowability are critical for electrode powder processing. It should have good cohesive properties while having adequate flow to allow efficient transport and mixing. The powder shear data for the three cathode powders is shown in Figure 3.
Table 1 shows the shear properties from the yield locus analysis performed in TRIOS Software. Cohesion, unconfined yield strength, and major principal stress decreased with increasing PVDF binder content. The flow function, which indicates if the sample will be a free-flowing powder, can be determined by taking the ratio of major principal stress over unconfined yield strength, as described in [6]. Following the Jenike Flowability Classification system all three of the powders lie in the easy flowing regime which corresponds to a flow function between 4 and 10 [9]. The SEM images in Figure 2 help explain this, as the presence of higher PVDF content acts to coat the particles and provide a smoother surface. This smoother surface reduces interparticle friction in the shear experiment and gives the bulk properties of higher flow function and less cohesion with higher polymer content.
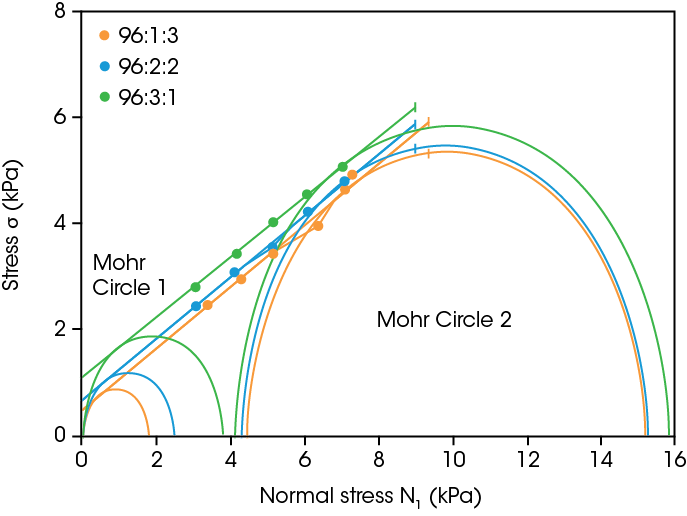
Table 1. Yield locus analysis summary of the three cathode powders
NMC/CB/PVDF | Cohesion (kPa) | Unconfined Yield Strength (kPa) | Major Principal Stress (kPa) | Flow Function |
---|---|---|---|---|
96/3/1 | 1.11 | 3.81 | 15.84 | 4.16 |
96/2/2 | 0.7 | 2.44 | 15.27 | 6.25 |
96/1/3 | 0.52 | 1.8 | 15.19 | 8.45 |
Powder Flow
Powder flow testing provides insight into the powder flowability and effective materials transport for processing. Figure 3 shows the total flow energy during confined and unconfined conditions. Confined conditions occur when the impeller rotor is moving down, and unconfined occurs when the rotor is moving upwards. The samples with the higher PVDF content have a higher total flow energy in both cases, showing that adding PVDF requires the rotor to do more work to move up and down through the sample.
As shown in the SEM images and the shear results, the PVDF binding effect leads to a smoother surface that reduces interparticle friction, but also causes agglomeration in the powder due to interparticle binding. The agglomeration will lead to a higher energy input needed for sufficient flow. In the confined measurement, the cycling shows a slightly increasing total flow energy due to the increased mixing, causing more binding and larger agglomerates to form. The presence of larger agglomerates requires more work done by the rotor to compress the powder while going downwards during the confined flow step. In the unconfined measurement the particle binding does cause an overall increase in flow energy at higher PVDF content, but the absence of compression during the experiment leads to a relatively steady total flow energy during cycling.
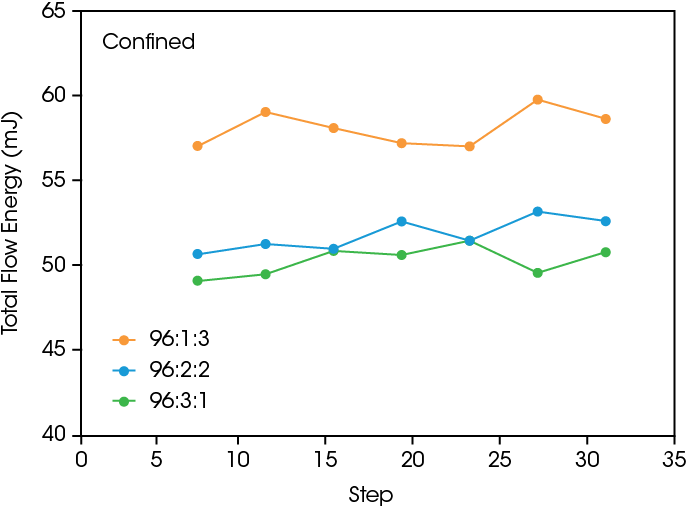

Conclusions
With the increasing demand for cost saving in manufacturing processes of LIBs, the use of powder coating technologies to fabricate electrodes is being increasingly explored. Understanding the bulk properties of the powders is necessary for optimal formulation and design of the mixing and coating process. In this work, NMC-based cathode powders were analyzed for insight into optimizing the electrode formulation and processing conditions. Discovery TGA provides a quality check on the binder content from the formulation and determines how much binder is present in the sample. With the TA Instruments Powder Accessory, the shear and flowability properties were characterized, showing that flowability and flow energy are impacted by increasing PVDF binder content. Using SEM imaging, it was shown that higher PVDF content acts to coat the surface of the particles and act as physical binder of the cathode particles, acting to reduce interparticle friction and increase flowability. As a result, the shear powder analysis shows a higher flow function and lower cohesion for greater PVDF content. The binding effect of the particles leads to an overall higher total flow energy when tested in the powder flow configuration with a smooth surfaced cup and impeller rotor. These results can be used to optimize the formulation and the powder mixing process and ensure homogenous cathode powders that will have repeatable and consistent electrochemical performance.
References
- Y. Lu, C.-Z. Zhao, H. Yuan, J.-K. Hu, J.-Q. Huang and Q. Zhang, “Dry electrode technology, the rising star in solid-state battery
industrialization,” Matter, vol. V, no. 3, pp. 876-898, 2022. - A. Gyulai, W. Bauer and H. Ehrenberg, “Dry Electrode Manufacturing in a Calender: The Role of Powder Premixing for Electrode Quality and Electrochemical Performance,” ACS Appl. Energy Mater., vol. VI, no. 10, p. 5122–5134, 2023.
- M. Ryu, Y.-K. Hong, S.-Y. Lee and J. H. Park, “Ultrahigh loading dry-process for solvent-free lithium-ion battery electrode fabrication,” Nature Communications, vol. 14, p. 1316, 2023.
- A. K. Stephan, “A Pathway to Understand NMC Cathodes,” Joule, vol. IV, no. 8, pp. 1632-1633, 2020.
- ASTM International, “ASTM D7891-5 Standard Test Method for Shear Testing of Powders Using the Freeman Technology FT4 Powder Rheometer Shear Cell,” 2016, 2016.
- J. Vail, S. Cotts and T. Chen, “Powder Rheology of Lactose: Impacts of powder morphology on performance of pharmaceutical excipients,” TA Instruments, vol. RH123.
- K. Dennis and S. Cotts, “RH125: Powder Rheology of Graphite: Characterization of Natural and Synthetic Graphite for Battery Anode Slurries,” TA Instruments, New Castle, DE.
- S. Dwivedi, M. Badole, K. Gangwar and S. Kumar, “Relaxation processes and conduction behaviour in PVDF-TrFE and KNNbased composites,” Polymer, vol. 232, p. 124164, 2021.
- W. Chen and A. W. Roberts, “A modified flowability classification model for moist and cohesive bulk solids,” Powder Technology,
vol. 325, pp. 639-650, 2018.
Acknowledgement
This paper was written by Mark Staub, Ph. D and Hang Lau, Ph.D at TA Instruments.
TA Instruments, TRIOS, and Discovery is a trademark of Waters Technologies Corporation. PHENOM is a trademark of Thermo Fisher Scientific Inc.
Click here to download the printable version of this application note.