From Industrial Revolution to Composites Innovation
Since the industrial revolution, innovation in various industries such as automotive, aerospace, construction and others has been attributed to the development of materials such as aluminum, steel, and iron. Today, growing populations and industries are further driving demand for high-performing, environmentally safe and lightweight materials. Composites materials meet these requirements and support new product design.
Composite materials are comprised of two or more distinct phases bonded together based on their individual physical and chemical properties which leads to their classifications in matrices. Composites have properties such as light weight, high strength-to-weight ratios, and resistance to chemicals, corrosion, and heat, among many others that cannot be achieved with a single material alone. Endless material combinations offer greater control over final performance characteristics. This freedom for ultimate material design opens opportunities for diverse applications across countless industries.
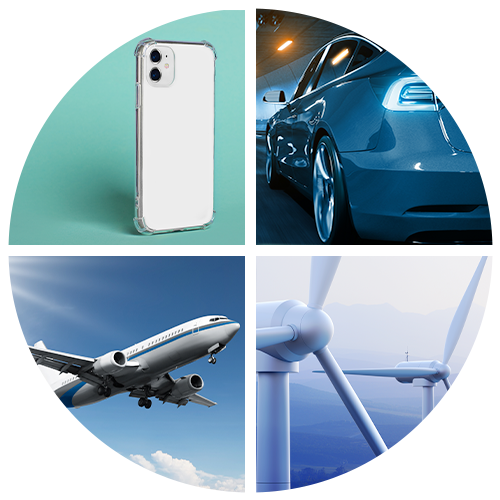
Rethinking Material Design with Composites
With the demand for environmentally safe and high performing materials from end-users, all members of the composites value chain — raw material manufacturers, semi-finished/finished material, component, structurers, and OEM/MRO — are rethinking how they innovate in making new materials with composites. This surge is a result of global changes such as:
- Growing need for strong, lightweight materials for automotive, aerospace, and wind energy applications
- Increasing demand for personal electronics like laptops and mobile phones
- Advancements in 3D printing technologies for fiber reinforced composite tooling, ceramic matrix composites (CMCs), and woven fiber composites.
This shift comes with a new set of challenges as composite materials must be highly specified for their end use, requiring enhanced testing at every step of the value chain. Safety and performance cannot be compromised hence the need for high quality testing.
TA Instruments | Waters solutions enable research scientists and engineers to efficiently characterize and test materials without compromising product safety and performance throughout the composites value chain. Advanced techniques help you investigate physical, thermal, and mechanical properties of your composite matrix such as viscosity, cure time, creep, durability/fatigue, compression, tensile or flexural strength, and many other properties as you innovate for performance with safety in mind.
Composites Value Chain
Learn more about the analytical solutions used as you go through each stage of the composite development process.
Since each raw material comes with varying properties and is processed with end-use application in mind, manufacturers must accurately characterize their materials and understand how their properties will impact final product performance. In order to meet the demands of semi-finished/finished material customers and ultimately Original Equipment Manufacturers (OEMs), raw material manufacturers must quantify the individual properties of their starting material plus characterize their final blends. The common composite raw materials are resins (thermoplastics and thermosets) and fibers.
Explore Waters/TA Instruments solutions that would help your Research, Product development and fundamental QA/QC testing.
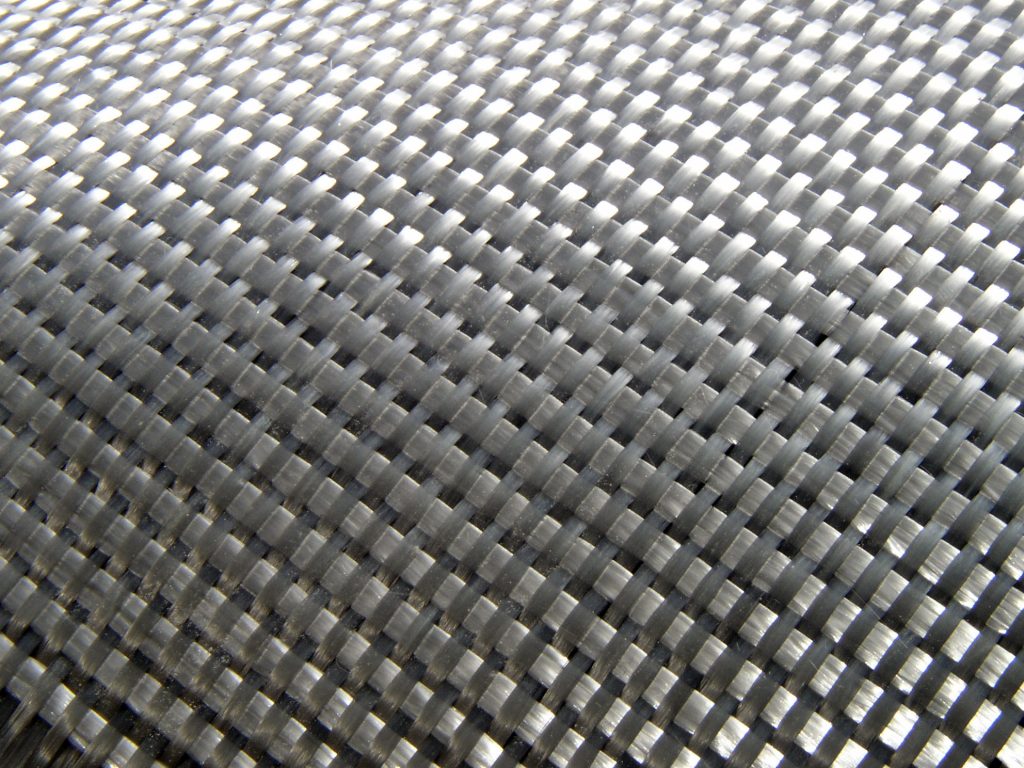
- Coefficient of Thermal expansion (CTE)
- Glass transition temperature (Tg)
- Glass fiber content
- Glass transition temperature (Tg)
- Coefficient of Thermal expansion (CTE)
- Tensile
- Compression
- Compression after impact (CAI)
- Flexural
- Torsional
- Shear
- Impact
- Fatigue
When designing semi-finished/finished materials to the specification requirements of both component manufacturers and OEMs, tests must be performed to verify material qualities. Understanding how material processing affects properties and performance is very important in processing an excellent product.
Whether you’re making semi-finished products such as prepregs or finished products via other manufacturing processes (e.g., compression molding), using the right analytical solutions to understand how the properties of your material will affect performance is very important to manufacturing a high value product that will meet the specifications of your end-user.
Explore Waters/TA Instruments solutions to help you refine material properties crucial for processing that will lead to high performing materials.
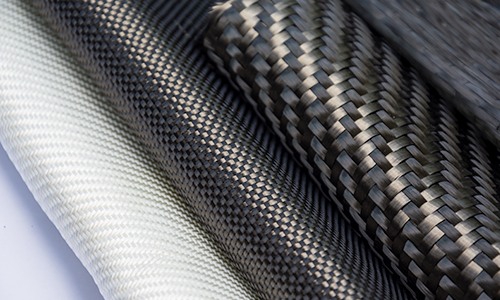
- Coefficient of Thermal expansion (CTE)
- Glass transition temperature (Tg)
- Creep
- Glass transition temperature (Tg)
- Glass transition temperature (Tg)
- Coefficient of Thermal expansion (CTE)
- Tensile
- Compression
- Compression after impact (CAI)
- Flexural
- Torsional
- Shear
- Impact
- Fatigue
- Viscosity
- Cure time
- Linear & Torsional DMA
The materials produced via semi-finished /finished manufacturing processes are used in developing and manufacturing components for structural companies with an end-use application in mind. Since at this stage, the end-use application is specifically defined, prototyping, manufacturing, and testing to meet specifications is crucial. Any product failure can compromise safety, especially in the automotive and aerospace industries.
Waters/TA Instruments solutions can help investigate mechanical properties that are crucial to product performance and prevent failure of end-use product applications.
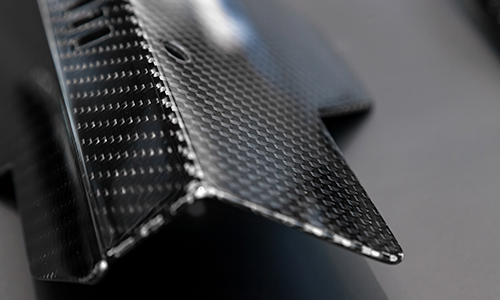
- Tensile
- Compression
- Compression after impact (CAI)
- Flexural
- Torsional
- Shear
- Impact
- Fatigue
- Coefficient of Thermal expansion (CTE)
- Raw Materials
-
Since each raw material comes with varying properties and is processed with end-use application in mind, manufacturers must accurately characterize their materials and understand how their properties will impact final product performance. In order to meet the demands of semi-finished/finished material customers and ultimately Original Equipment Manufacturers (OEMs), raw material manufacturers must quantify the individual properties of their starting material plus characterize their final blends. The common composite raw materials are resins (thermoplastics and thermosets) and fibers.
Explore Waters/TA Instruments solutions that would help your Research, Product development and fundamental QA/QC testing.
- Coefficient of Thermal expansion (CTE)
- Glass transition temperature (Tg)
- Glass fiber content
- Glass transition temperature (Tg)
- Coefficient of Thermal expansion (CTE)
- Tensile
- Compression
- Compression after impact (CAI)
- Flexural
- Torsional
- Shear
- Impact
- Fatigue
- Semi-Finished/Finished Materials
-
When designing semi-finished/finished materials to the specification requirements of both component manufacturers and OEMs, tests must be performed to verify material qualities. Understanding how material processing affects properties and performance is very important in processing an excellent product.
Whether you’re making semi-finished products such as prepregs or finished products via other manufacturing processes (e.g., compression molding), using the right analytical solutions to understand how the properties of your material will affect performance is very important to manufacturing a high value product that will meet the specifications of your end-user.
Explore Waters/TA Instruments solutions to help you refine material properties crucial for processing that will lead to high performing materials.
- Coefficient of Thermal expansion (CTE)
- Glass transition temperature (Tg)
- Creep
- Glass transition temperature (Tg)
- Glass transition temperature (Tg)
- Coefficient of Thermal expansion (CTE)
- Tensile
- Compression
- Compression after impact (CAI)
- Flexural
- Torsional
- Shear
- Impact
- Fatigue
- Viscosity
- Cure time
- Linear & Torsional DMA
- Components
-
The materials produced via semi-finished /finished manufacturing processes are used in developing and manufacturing components for structural companies with an end-use application in mind. Since at this stage, the end-use application is specifically defined, prototyping, manufacturing, and testing to meet specifications is crucial. Any product failure can compromise safety, especially in the automotive and aerospace industries.
Waters/TA Instruments solutions can help investigate mechanical properties that are crucial to product performance and prevent failure of end-use product applications.
- Tensile
- Compression
- Compression after impact (CAI)
- Flexural
- Torsional
- Shear
- Impact
- Fatigue
- Coefficient of Thermal expansion (CTE)
Composites Resources
Webinars
Blog
Application Notes
- Testing to Improve the Durability of Artificial Heart Valves
- Flexural Fatigue Behavior of Woven Fiberglass Composites at Elevated Temperature
- Using an ARES Rheometer to investigate the β-relaxation change of graphene poly(ethylmethacrylate) nanocomposite
- Characterization of the Degree of Cure of Thermosetting Resins by DSC
- Stress/Strain Evaluation of Fibers Using TMA
- View all Application Notes