Optimization of Catalytic Reactions by High-Pressure TGA
Frieder Dreisbach
March 28, 2022
Catalytic reactions are everywhere: from plastics and bread to over 90% of all chemicals worldwide, countless goods and materials are manufactured with the aid of catalysts.1 Catalysts are substances that speed up sluggish chemical reactions. Faster reactions are more technologically and economically competitive. Furthermore, optimized catalysts offer a huge potential to reduce energy and resource consumption and lower carbon dioxide emissions.
Heterogeneous Catalysis
In industrial applications, catalysis, or a reaction using a using a catalyst, is classified as either , where the catalyst is in the same (usually liquid) phase as the reactant, or heterogeneous, where often a solid catalyst reacts with fluidic (gaseous or liquid) reactants.
Heterogeneous catalysis is an interface process, i.e. the size of the accessible catalyst surface area influences the reaction rate. Most catalytically active materials are small particles with a large surface-to-mass ratio, offering more reactivity with less catalyst.
Researchers measure reaction rates under application conditions to optimize their process and take maximum advantage of expensive catalyst materials. With better performing catalyst materials, reactions require less catalyst and therefore cost less, reduce energy consumption, and require fewer natural resources to manufacture products.
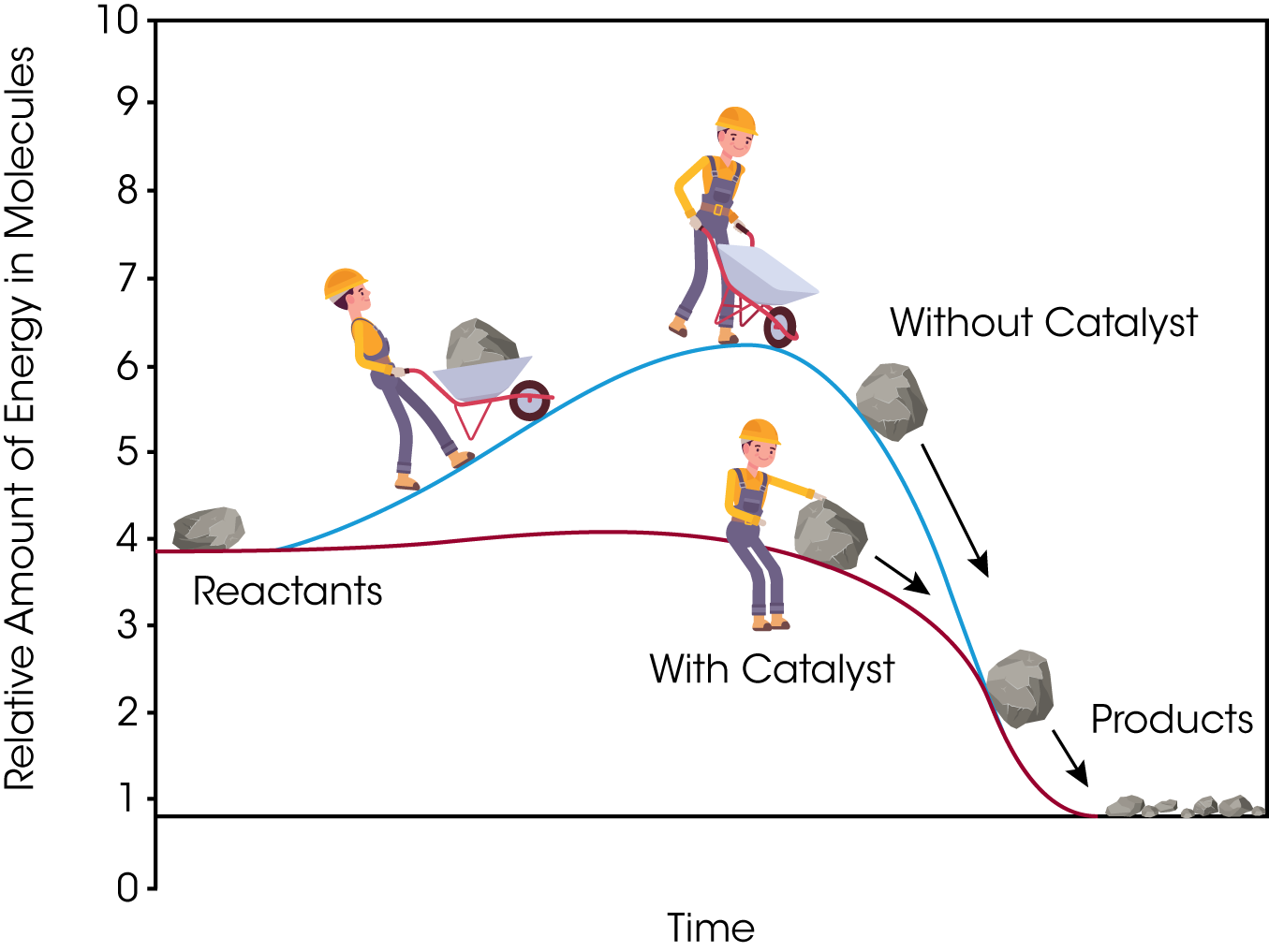
Catalyst Testing through High-Pressure TGA
High-pressure thermogravimetric analysis (HP-TGA) enables researchers to investigate reactions between a catalyst and a gas phase reactant under realistic working conditions on the lab scale. Reaction conditions can include high pressure, high temperature, and reactive gas mixtures and steam. Activation and deactivation of a catalyst by oxidation, reduction or coking are associated with a weight change and can be measured with high resolution in the HP-TGA. Simultaneously, the yield and kinetics of the reaction can be monitored by evolved gas analysis with online Mass Spectrometry, Gas Chromatography, FTIR or other methods. These data are extremely useful to optimize reaction conditions and develop improved catalyst materials.
The HP TGA instrument can be used as a catalytic reactor while monitoring the catalyst weight. This experimental setup allows researchers to exactly identify conditions that induce catalytic reactions and changes in the catalyst material such as activation or deactivation. The HP TGA’s reaction atmosphere can consist of common reactive gases such as hydrogen, methane, ethane, carbon dioxide or carbon monoxide and also steam, and the experimental conditions can cover temperatures up to 1100°C and pressures up to 80 bar.
The main benefit of performing catalytic gas phase reactions on solid catalysts in a TGA instrument is to measure the catalyst weight during the experiment to detect catalyst activation or deactivation processes continuously and quantitatively as they occur.
Optimizing Yield and Productivity
A key to improving the efficiency of catalytic reactions is selecting the optimal operating conditions for a given reaction. Product costs and environmental footprint can be reduced even further by developing catalytic processes using alternative feedstocks, which also require adapted process control.2
Example of optimizing catalysis conditions: Methanation of carbon dioxide is a process to generate methane by reduction with hydrogen following the reaction equation CO2 + 4 H2 ↔ CH4 + 2 H20. Hydrogen from renewable energy can be used to convert carbon dioxide into green methane as feedstock for chemical processing. This reaction has high commercial relevance as a key process in the power-to-gas (PtG) concept. In the example shown here, an alumina supported nickel catalyst is used for the methanation reaction a series of catalytic experiments with a gas mixture of 2% CO2, 8% H2 and 90% Ar. The pressure and temperature dependence of the reaction yield was monitored at various temperatures between 275°C and 350°C and at 1.5 bar, 15 bar and 30 bar using an online MS. Figure 2 compares the methane yield at all three pressures monitoring the mass trace m/z 15, which indicates the methane concentration which is the target product of the methanation reaction.

Comparing the MS data at different pressures and temperatures reveals that higher pressure leads to a higher reaction yield. The influence of temperature on the yield is similar, but more pronounced at 15 and 30 bar compared with the measurement at 1.5 bar. No catalyst weight change was detected at any pressure which proves that no deactivation or side reaction occurred.
Catalyst Deactivation
Catalyst deactivation describes the loss of catalytic activity or selectivity over time. All catalysts deactivate over time and must be replaced, but the operating time before deactivation can vary widely: it depends on the type of catalyst, the process, and the maintenance of optimum operating conditions, among other factors. Catalysts can deactivate in a few seconds or operate on schedule for several years.3 For industrial catalytic processes, catalyst deactivation is a major economic risk. Shutting down processes and replacing catalysts costs the chemical industry billions of dollars per year.4
There are common chemical, mechanical, and thermal mechanisms for catalyst deactivation which can be classified in different types: i.e. poisoning, coking or fouling and ageing.5, 6
Although catalyst deactivation is usually unavoidable in the long term, the beginning of premature deactivation can often be avoided with suitable process control measures7 which is the subject of research and development with the aim to design more robust industrial processes and catalyst materials.8 As a result, deactivation can be delayed and even reversed.
Assessing Catalyst Coking
Catalyst deactivation due to coke formation is an important technological and economic problem in petroleum refining and the petrochemical industry. Improved resistance of catalysts to coking can be achieved by using other catalytically active metals and/or adjusting reaction conditions such as temperature, pressure, or gas composition. Material and process optimization for coke formation requires measurement of catalyst deactivation kinetics under real reaction conditions.9
Example of measuring coking: A steam reforming reaction at 700°C and 10 bar is presented below. The reaction atmosphere consists of argon, methane, and steam with a steam to methane ratio of 4:1. Under these conditions, hydrogen generation is detected by online MS while the catalyst weight remains constant. To assess the onset of coking, the steam to methane ratio is changed to 1:1 and later to 1:2 by adjusting methane and steam flowrates. Figure 3 visualizes the catalyst weight and the steam to methane ratio over time.

At steam to methane ratios of 4:1 and 1:1, the catalyst weight is stable. When the ratio is changed to 1:2, the excess of methane immediately leads to a fast weight increase of 0.3 %wt/min. This weight increase is caused by the formation of coke (elemental carbon) on the catalyst. This coking process can be reversed, and the catalyst regenerated by switching off the methane flow. Now the steam oxidizes the coke which leads to a fast weight loss rate 0.9 %(wt)/min. In only 15 minutes, more than 4 mg of coke are removed from the catalyst surface. This proves the reversibility of the process if the reaction conditions are adjusted quickly enough. Figure 4 shows that coking can lead to impressive amounts of carbon formed if reaction conditions are not changed quickly after the coke formation starts.

Optimized Catalysis is just an Experiment Away
As the examples and techniques above demonstrate, catalysis can be improved through selecting the best catalyst and reactants, optimizing reaction conditions, and avoiding, delaying or reversing deactivation. Enhanced catalytic reactions offer increased sustainability while reducing cost.
High-Pressure TGA is a leading method to study catalyst performance and optimize heterogenic catalytic reactions. Gas phase reactions such as methanation, steam reforming and many other technically and commercially important reactions can be performed in a HP-TGA instrument at relevant pressure, temperature and gas or vapor composition conditions. The reaction turnover can be monitored by EGA analysis with mass spectrometry, FTIR or other suitable methods and the catalyst weight signal provides valuable online data on activation and deactivation processes.
Do you want to learn more about the potential of TGA for optimizing catalytic materials and processes? Please review our application note on the topic or watch the recorded webinars on TGA under extreme conditions or optimizing catalysts with TGA methods. Do not hesitate to contact TA Instruments experts to discuss your testing needs and explore the ideal instrumentation for your lab.
References:
- Ma, Z. and Zaera, F., Heterogeneous Catalysis by Metals, in King, R. Bruce; Crabtree, Robert H.; Lukehart, Charles M.; Atwood, David A. (eds.), Encyclopedia of Inorganic Chemistry, John Wiley & Sons, Ltd.
- Anderson, N., (2000), Practical Process Research & Development, Optimizing Catalytic Reactions, 185-201.
- Bartholomew, C.H., Mechanisms of catalyst deactivation, Applied Catalysis A: General 212 (2001) 17–60.
- Boskovic G., Baerns M. (2004), Catalyst Deactivation, in: Baerns M. (eds) Basic Principles in Applied Catalysis. Springer Series in Chemical Physics, vol 75. Springer, Berlin, Heidelberg.
- Figuerido, J.L. (Ed.), Progress in Catalyst Deactivation, NATO Advanced Study Institute Series E, Marunus Nijhoff, Boston, 1982.
- Hughes, R., Deactivation of Catalysts, Academic Press, London, 1984 (Chapter 8).
- Oudar, J. and Wise, H., Deactivation and Poisoning of Catalysts, Marcel Dekker, New York, 1985, 1.
- Butt, J.B., Petersen, E.E., Activation, Deactivation, and Poisoning of Catalysts, Academic Press, San Diego, 1988.
- Wolf, E. E. and Alfani, F., (1982), Catalysts Deactivation by Coking, Catalysis Reviews, 24:3, 329-371