Plastic parts produced by converters are often find use in products produced by OEM manufacturers as a component of a larger assembly. End market applications for plastics are diverse and range from packaging for food and consumer care products, to applications in automotive, building and construction, medical devices, and personal electronic devices. These end-users of plastic products benefit from using analytical techniques to characterize product performance, predict product lifetimes, and perform failure analysis studies.

Instruments and Test Parameters
Material strength
- Young’s modulus, yield strength, ultimate strength, elongation at break
- Fatigue and durability, S-N curves
- Strength vs. temperature
Final assembly strength
- Flexural, bending or crush failure points
- Fatigue and durability, S-N curves
- Strength vs temperature
Differential Scanning Calorimetry
Thermal stability
- Oxidative Induction Time (OIT)
- Oxidative Onset Time (OOT)
Phase transition
- Crystallinity
Polymer Workflow Automation
Thermal stability
- Decomposition temperature
Polymer Workflow Automation
Mechanical properties of materials
- Storage modulus, loss modulus, tan delta
- Glass transition (Tg)
Characterization of blend compatibility
- Storage modulus, loss modulus, tan delta
Effect of heat and humidity on mechanical properties
- Storage modulus, loss modulus, tan delta
- Glass transition (Tg)
Characterization of mechanical anisotropy
- Storage modulus, loss modulus, tan delta
Application Example
How does the product perform?
Understanding the product performance under final end-use application conditions helps guide product formulation, process optimization, and plays an important role in troubleshooting and failure analysis. For plastic products, the mechanical properties are closely tied to the end-use product performance and can be evaluated through a combination of different mechanical testing techniques that provide information on the material’s modulus. Depending on the type of deformation, additional information and insights can also be obtained.
- Monotonic testing: Unidirectional deformation to failure under an applied load – test materials under conditions of increasing load (e.g., Stress-strain curves)
- Fatigue testing: Understand damage and failure from repeated loading – test materials and finished products under conditions of increasing cycling (e.g., S/N curves)
- Dynamic Mechanical Analysis (DMA): Study solid viscoelastic properties as a function of temperature and deformation frequency (e.g., Glass transition temperature (Tg), Time-Temperature Superposition (TTS))
DMA testing investigates the temperature dependance of a solid specimen’s mechanical properties under bending, compression, or tensile deformation. It provides quantitative information about the material’s viscoelastic properties through the Storage Modulus (E’), Loss Modulus (E”) and tan(δ) (damping factor). When polymeric specimens are heated, they undergo transitions that are reflected in these mechanical parameters. DMA is one of the most sensitive techniques available to measure glass transition and beta transition temperatures, since it picks up on subtle changes in local polymer mobility brought about by the increased temperature.
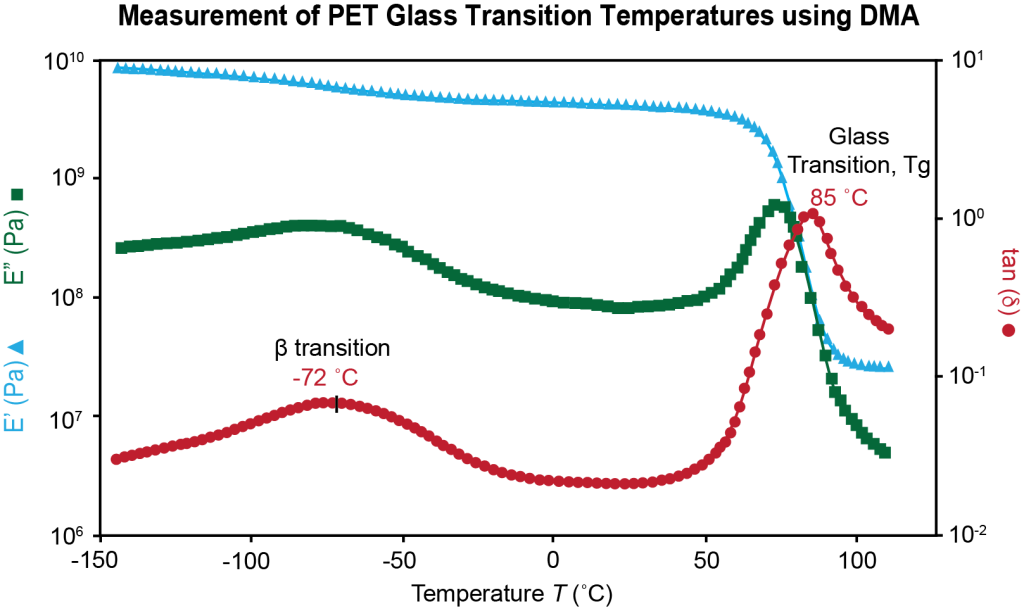