Keywords: workflow automation, polymer melts, auto-trim, Discovery Hybrid Rheometer, recyclable polymers, LDPE
RH127
Abstract
The auto-trim accessory for Discovery Hybrid Rheometers automates the melting, gap setting, and crucial sample trimming step in polymer melt rheology testing. The automation of this step improves data consistency by up to 5x, increases continuous walkaway time by 80%, and reduces new operator training time to less than 30 minutes. This setup requires the operator to simply load the material, close the oven, and press Start to generate high quality polymer melt rheology data.
Introduction
Polymer melt rheology can be used to fingerprint molecular architecture, which can affect processing, extruding, and molding parts. Processing may involve holding polymers at isothermal conditions for extended periods of time or increasing the temperature to improve flowability into molds. It is important to quantify the melt parameters to assess stability, determine processing conditions, and maintain quality control especially for variable feedstocks such as post-consumer recycled (PCR) materials. These parameters may be quantified with oscillatory measurements performed on the TA Instruments Discovery Hybrid Rheometer (DHR) with Environment Test Chamber (ETC) oven. Polymer melt rheology workflows are improved with the addition of the auto-trim accessory.
A common geometry for polymer melt rheology is the parallel plate. With this geometry, the velocity gradient induced on the fluid is greatest at the exterior edge and the torque measured by the instrument is representative of this edge. To achieve accurate and reproducible results, it is important to properly fill and trim the sample to prevent edge effects. If the gap is underfilled, values will be lower than expected and if the gap is overfilled, additional drag will result in higher-than-expected values. Both scenarios produce inaccurate results, and variability in underfilling or overfilling results in data inconsistencies.
For parallel plate geometries, correct filling is achieved by loading extra sample, lowering to the trim gap (typically 5% above the geometry gap), and trimming the sample flush to the parallel plates with a flat surface. The geometry is then lowered to the geometry gap where the sample should bulge slightly, indicating the correct fill. If polymer pellets, flakes, or powder are being used, this step is traditionally performed with a removable melt ring. This step requires a trained user to remain at the instrument to load sample into the melt ring, wait until the sample melts, lower the geometry to be in contact with the sample, remove the melt ring, send the geometry to the trim gap, trim the sample, and finally send the geometry to the geometry gap. This process also involves opening and closing the ETC oven, which affects temperature equilibration of the sample and allows oxygen to enter if an inert environment is being used.
Variability in sample filling and trimming between users can also cause data variability. For a user new to trimming, the variability and validity of their data is reliant upon correct and consistent trimming. For multiple operators, they must strictly follow their trimming standard operating procedure and use the same trimming tools. The timing also must be consistent between operators, including oven dwell time, trim time, and oven open time. The auto-trim accessory removes many sources of variation related to user error and multi-user inconsistencies. The TA Instruments auto-trim accessory can be used to improve consistency, repeatability, and accuracy of measurements.
Auto-Trim Accessory
The auto-trim accessory, shown in Figure 1, consists of the stage, disposable trimmer, locking ring, and pneumatic controls (not shown). Training is straightforward, especially for new users, and takes less than 30 minutes. The user equilibrates the geometry and accessory to the desired temperature and zeroes the gap. Then, the user loads the disposable trimmer and secures it with the locking ring. The user loads a sample, closes the oven, and starts the TRIOS procedure. Once the procedure is initiated, the user may walk away while the instrument, accessory, and software execute the remaining steps. The instrument lowers the geometry to the trim gap and after waiting the user-specified time, the sample is trimmed by the automatic lowering of the trimmer assembly as shown in boxes 1, 2, and 3 of Figure 1. The auto-trim accessory semi-automates polymer melt rheology workflow, resulting in better data consistency, increased walkaway time, and reduction in operator training.
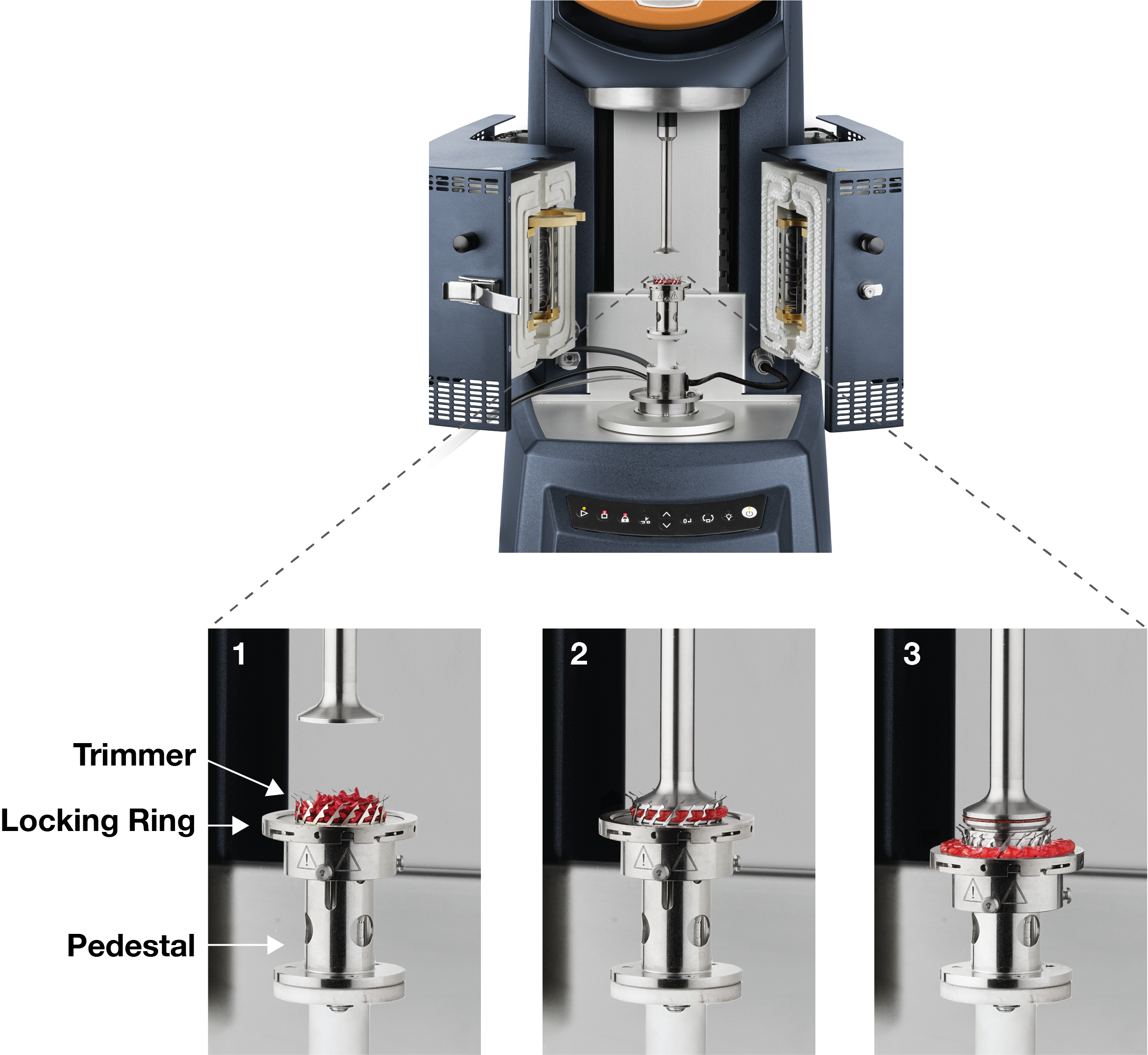
Data Consistency
Low density polyethylene (LDPE) is a common packaging material which may be recycled. Quantifying melt properties of virgin LDPE is important for processing and making blends with virgin and recycled content. The data shown in Figure 2 was collected with the auto-trim accessory and is for virgin LDPE at 180 °C. A total of 36 tests were performed divided amongst 3 operators ranging from novice to experienced rheologists. The crossover modulus is plotted as a function of test number and each value between test number and operator falls within ±8%. The coefficient of variance (COV = Standard Deviation/Mean) for all the auto-trimmed tests was 2.3%, which is comparable to a COV of 2.6% for a single expert rheologist performing manual trimming.
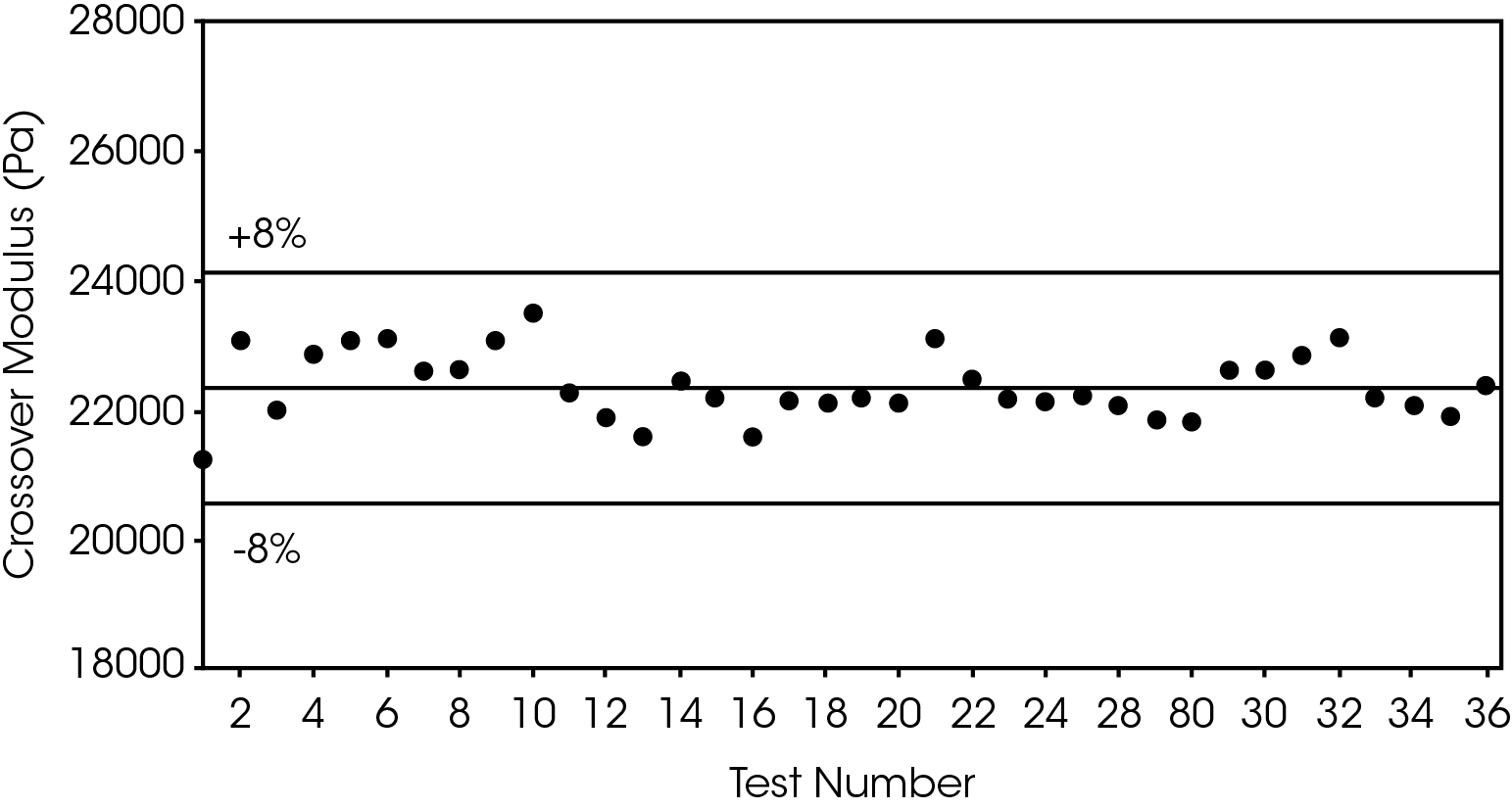
Walkaway Time
The total experiment time for both auto-trim and manual trimming experiments is shown in Figure 3 for LDPE at 180 °C. The total time is divided into user time and walkaway time. The user time for the auto-trim method is about a minute, just 22% of the manual method time. Even though the total test time is about the same, the user gains approximately an 80% increase in walkaway time. This reduction of user time would result in more than an hour of additional available operator time per 8-hour shift. This walkaway time enables the user to prepare additional samples, check on other instruments, or even run a second rheometer with an auto-trim accessory. This increase in walkaway time is amplified when testing samples that have a long relaxation time, such as acrylonitrile butadiene styrene (ABS). The auto-trim accessory frees up user time all while maintaining the same amount of total experiment time as compared to the manual method.
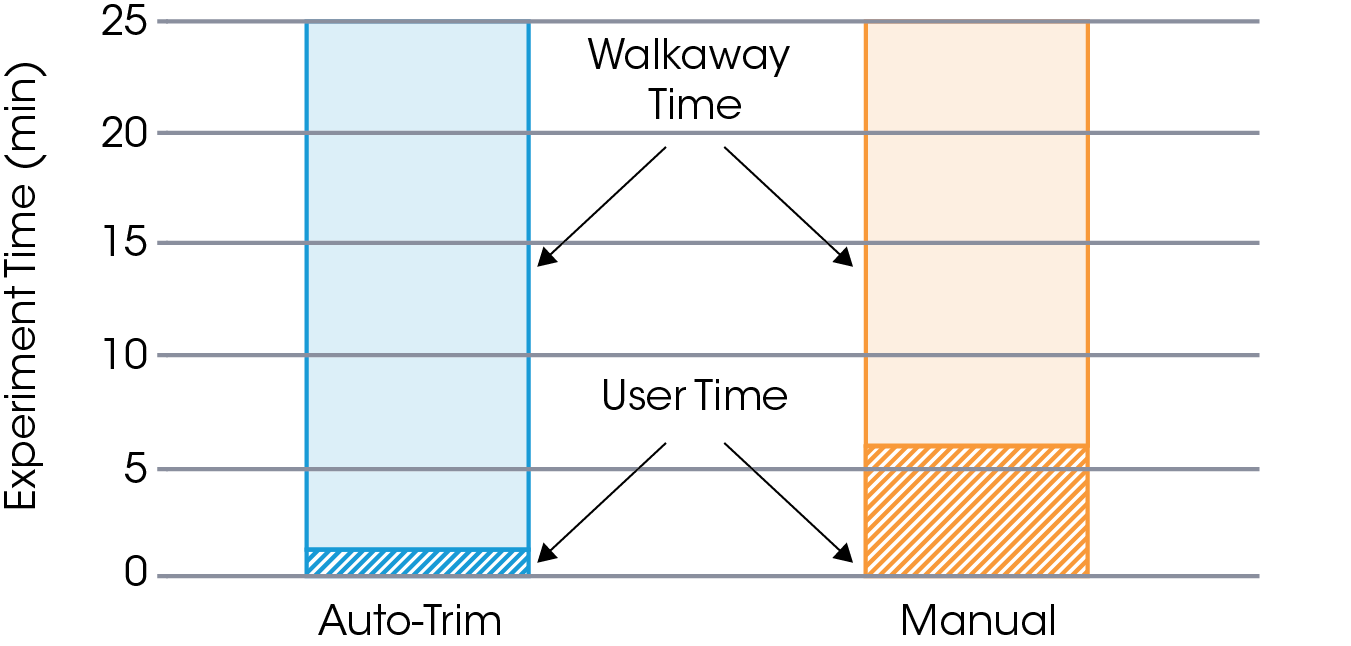
Conclusions
The TA Instruments auto-trim accessory automates a key step in polymer melt rheology workflow, resulting in improved data consistency and increased user walkaway time. The accessory greatly reduces sources of data variability including individual user consistency, multi-user consistency, and the thermal profile the sample experiences. The time that it frees up for an individual user can allow for a single operator to manage multiple instruments or perform other valuable tasks in the lab. These increases in data consistency and operator efficiency are all realized with minimal required operator training.
Acknowledgement
This paper was written by Kimberly Dennis, PhD at TA Instruments.
Click here to download the printable version of this application note.