Polymer synthesis from monomers and other raw materials requires carefully controlled processes that account for the polymer chemistry and architecture. The catalyst structure and reaction conditions determine the molecular weight and molecular weight distribution of the final polymer, which impacts processability and its suitability for end-use applications.
Analytical technology powers fundamental polymer research and provides material properties relevant to QA/QC, ensuring that the polymers are developed and produced with the right combination of parameters for the final application.
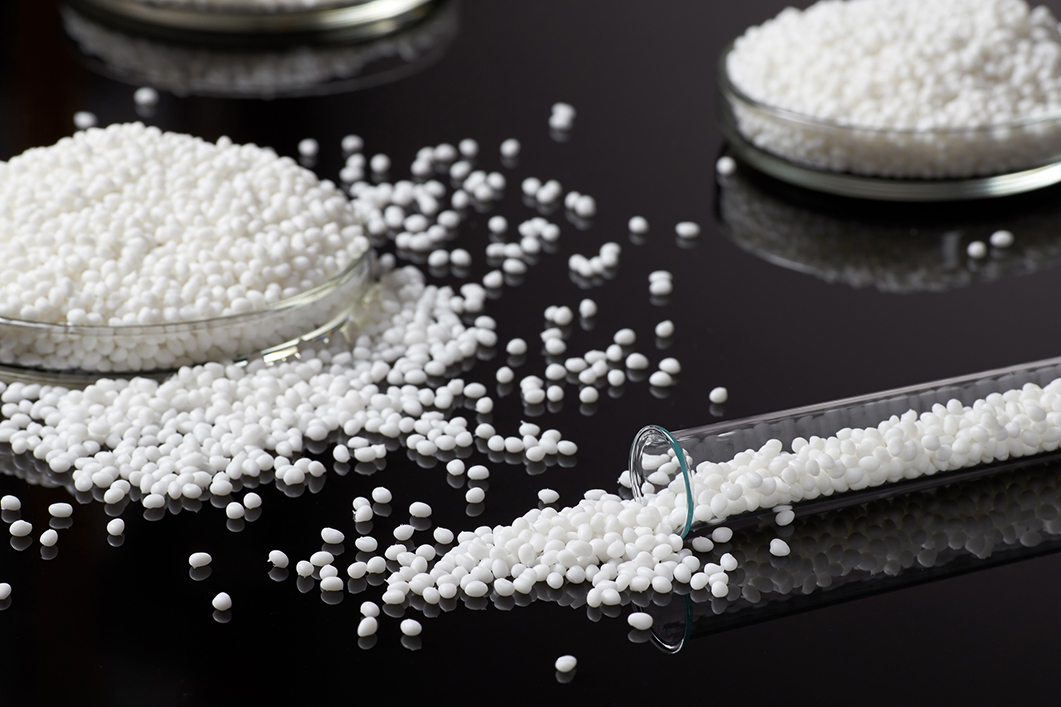
Instruments and Test Parameters
Differential Scanning Calorimetry
Phase transition
- Melting temperature (Tm)
- Heat of fusion
- Glass transition (Tg)
- Crystallinity
Heat capacity
Thermal stability
- Oxidative Induction Time (OIT)
- Oxidative Onset Time (OOT)
Polymer Workflow Automation
Thermal stability
- Decomposition temperature
Composition determination
- Volatile or solvent content
- Filler content (residue)
- Decomposition products
- Evolved gas analysis, TGA-MS, TGA-FTIR, TGA-GCMS
Polymer Workflow Automation
Processability
- Viscosity flow curve
- Zero shear viscosity
- Viscoelastic properties (Storage modulus, loss modulus)
- Crossover modulus and frequency
Melt strength
- Extensional viscosity
Polymer Melt Rheology Workflow Automation
Mechanical properties of materials
- Storage modulus, loss modulus, tan delta
- Glass transition (Tg)
Characterization of mechanical anisotropy
- Storage modulus, loss modulus, tan delta
Material strength
- Young’s modulus, yield strength, ultimate strength, elongation at break
- Fatigue and durability, S-N curves
- Strength vs. temperature
Final assembly strength
- Flexural, bending or crush failure points
- Fatigue and durability, S-N curves
- Strength vs temperature
Application Examples
What is the processing temperature for this resin?
Understanding the temperatures at which polymers soften and melt is a fundamental material property relevant to polymer processing. As one of the first steps in extrusion, injection molding and film blow molding processes, resin pellets are routinely heated past the melting point; for thermoforming and blow molding, the resin is heated above its glass transition temperature to soften it, but without completely melting it. This transformation from a solid resin pellet (lower energy state) to a softened or completely melted pellet (higher energy state) requires the input of energy and can be measured using Differential Scanning Calorimetry (DSC).
In a DSC test, the heat flow of the sample is monitored as the temperature is increased at a constant rate. Thermal transitions such as melting and glass transition show up as endothermic events, where the material absorbs heat as it moves into the higher energy state. The results also reveal information about the polymer morphology, with clear differences between amorphous and semi-crystalline states. During a DSC test’s first heat cycle, amorphous materials display a broad glass transition without melting, while semi-crystalline polymers have a sharp and well-defined melting peak. Since the melting and glass transition temperatures are unique to each polymer, this information can be used to quickly evaluate the quality of the incoming feedstock prior to processing.
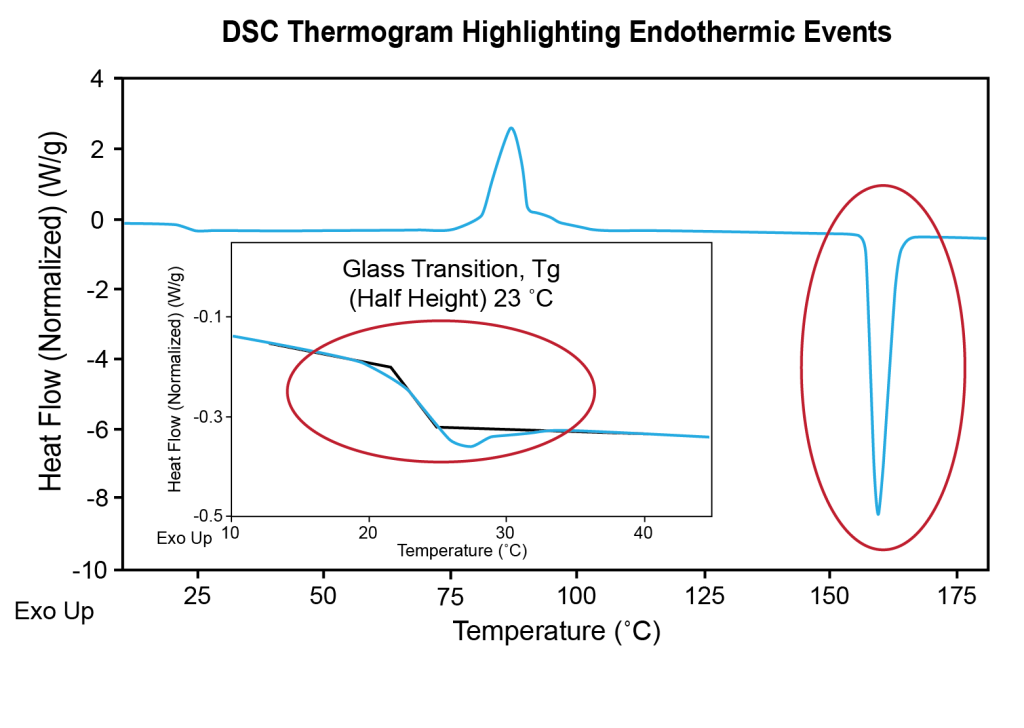
Answer the following questions with results from your DSC:
- Feedstock evaluation: Is this a neat polymer, or is it a blend? Can vendor A’s resin be replaced with lower cost resin from vendor B?
- Processing: How much thermal energy is needed to completely melt the resin pellets?
- After processing: Is there a thermal history after processing vs. as-received? (1st vs. 2nd heat)
- End-of-life recycling: Does this batch of PCR (post-consumer resin) have significant contamination from other polymers?
How does this resin decompose?
Common thermoplastic processing techniques, like extrusion, injection molding and blow molding, require the resin to be heated above the melting point for easy processing. However, it is important to carefully control the processing temperatures to avoid resin degradation that can occur at elevated temperatures. For polymers, the onset of degradation can be identified as the temperature at which significant weight loss (typically >5%) starts to take place and can measured using a Thermogravimetric Analyzer (TGA).
During thermal analysis of polymers, TGA tests are routinely performed before DSC testing since the TGA results help establish the upper temperature limits for subsequent testing. Apart from identifying the degradation window for processing, TGA results also quantitatively reveal the composition of the major ingredients in the resin, such as the amount of base polymer, plasticizer, and filler present. The off-gas generated during a TGA experiment can be further analyzed to gain insights into the chemical identity of the decomposition products. This type of Evolved Gas Analysis (EGA) is especially powerful since it combines real-time TGA data with results from FTIR and GC-MS.
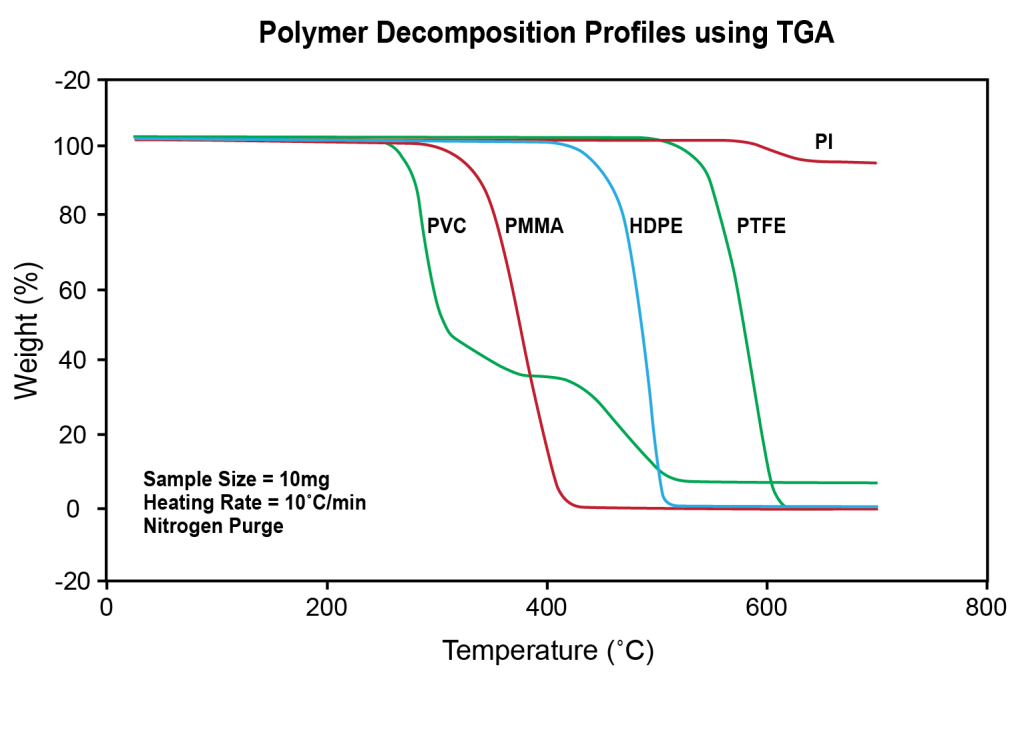
Answer the following questions with results from your TGA:
- Feedstock evaluation: At what T does this resin decompose? What is the decomposition profile?
- Processing: Are there volatile materials in this batch of resin? Will there be off-gassing after processing?
- Failure Analysis: Is there a difference in the filler content or the decomposition profiles of the good vs. bad parts?
- End-of-life recycling: During pyrolysis, at what temperature does the maximum weight loss occur? What contaminants are presents in this batch of recycled resin?
Related Application Notes:
How stable is this resin during processing and end-use?
Stabilizers and other additives are often added to resins to prevent degradation from environmental effects encountered during processing and end-use conditions. These additives include antioxidants, oxygen scavengers, heat and UV light stabilizers, or flame retardants, to ensure the polymer’s intended properties are maintained during processing and the product’s lifetime. Stabilizers are inherently sacrificial and are gradually consumed when exposed to high temperature or UV light; once the stabilizer is completely exhausted, the polymer properties start to degrade rapidly.
The performance of stabilizers can be evaluated through Oxidative Induction Time (OIT) analysis on the DSC. In this isothermal test, the purge gas in the DSC is switched from Nitrogen to Oxygen, providing an environment where the stabilizer is consumed. At the onset of polymer degradation, the heat flow signal starts to increase and the time is noted as OIT.
Temperature ramps on the DSC can also be used to measure the Oxidative Onset Time (OOT), a related measure of polymer stability. Both OIT and OOT tests can also be performed using a high-pressure DSC, which reduces test time by accelerating stabilizer consumption.
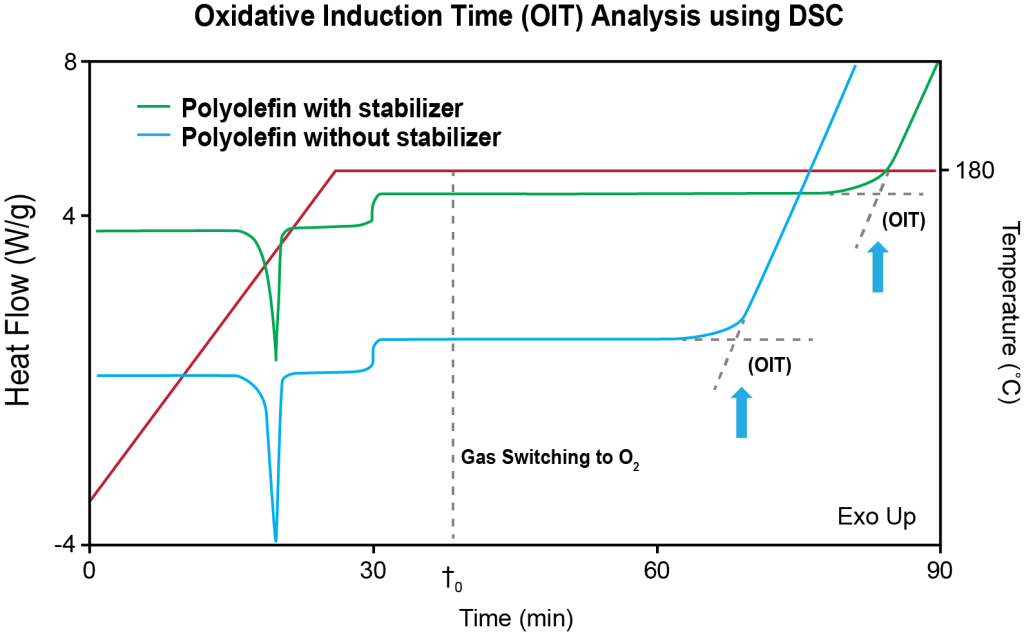
Answer the following questions with OIT & OOT results from your DSC:
- Feedstock evaluation: Can this resin be processed as-is? Are antioxidants needed for additional stability?
- Failure Analysis: Did this part antioxidant at sufficient levels suitable for the end-use conditions?
- End-of-Life recycling: How much antioxidant is needed to stabilize and process this batch of PCR?
Related Application Notes:
How does this resin flow?
The viscosity and viscoelastic behavior of polymer melts plays an important role when processing polymers using injection molding and extrusion techniques. At a basic level, the viscosity represents the material’s internal resistance to flow – resins with higher viscosity flow slower and take more time to fill the mold, increasing the cycle time and introducing the possibility of defects like short shots. As a result, it is critical to measure and carefully control the viscosity of the resin to ensure process stability and eliminate batch-to-batch variations.
For polymer melts, the viscosity profile depends on the rate of deformation, also known as the shear rate. At the high shear rates encountered in the extrusion and injection molding processes, the viscosity curve displays a shear-thinning behavior in the power law region – as the shear rate increases, the viscosity decreases. This shear rate dependence is influenced by the polymer’s molecular weight distribution and degree of branching.
While high shear rates are relevant to processing conditions, viscosity measurements at low shear rates are essential for revealing the resin’s molecular structure. The zero shear viscosity in the first Newtonian plateau directly correlates with resin’s molecular weight, and can be measured using rotational rheometers.
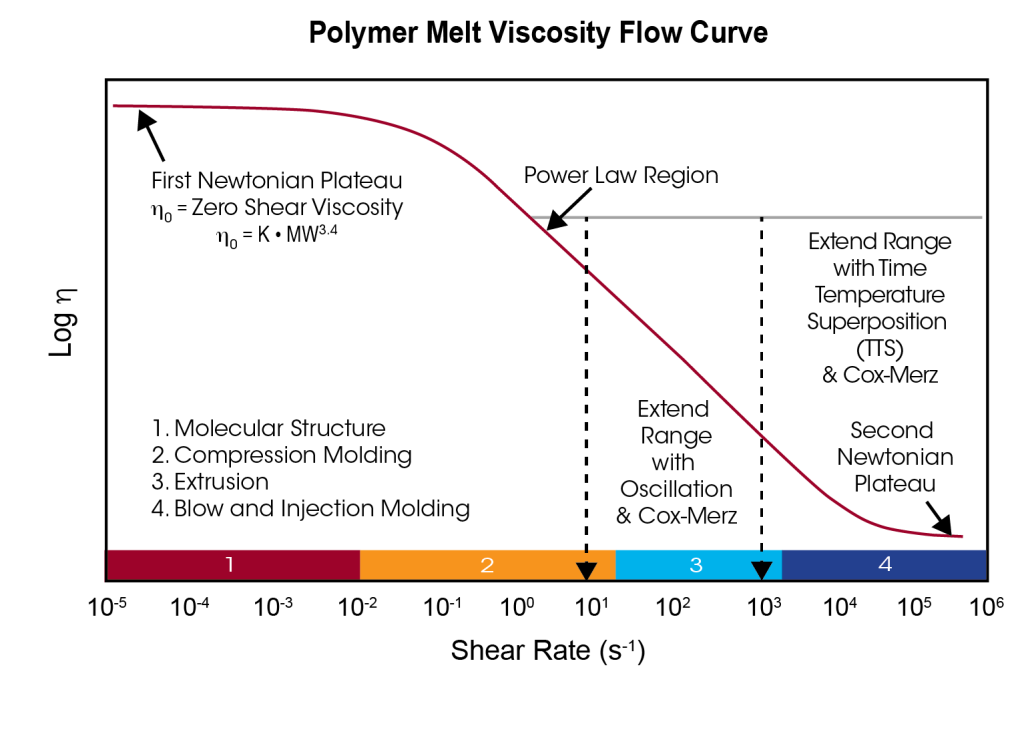
How is viscoelasticity related to Molecular Weight/ Molecular Weight distribution?
Oscillatory tests on rotational rheometers provide valuable insights into a polymer’s viscoelastic properties by probing the polymer’s structure through small deformations over a range of time scales. The results provide the polymer’s Storage Modulus (G’), Loss Modulus (G”) and complex viscosity (η*) as a function of the oscillation frequency and can be used to better understand the dynamics of polymer relaxation. These parameters are strongly influenced by resin’s molecular weight, molecular weight distribution, and long chain branching structure. Compared to melt flow indexers or capillary rheology, the viscoelastic profile from rotational rheology testing is particularly sensitive to the presence of high molecular weight contamination that can cause processing issues.
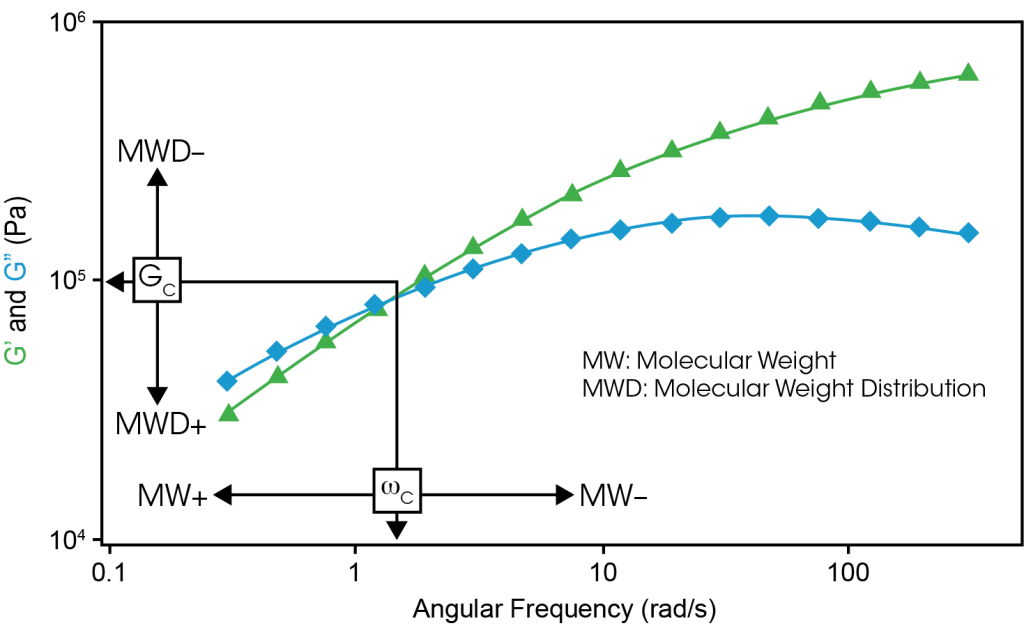
Answer the following questions with viscosity and viscoelastic measurements from your rotational rheometer:
- Feedstock evaluation: How is the viscoelastic profile affected by batch-to-batch changes in the resin’s Molecular Weight/ Molecular Weight Distribution?
- Processability: Does the resin have the right viscosity at all shear rates relevant to the manufacturing process?
- End-of-life: End-of-life recycling: How do contamination and MW variation in the recycled resin impact processing?
Related Application Note:
Does this resin possess sufficient melt strength for blow molding?
Manufacturing processes such as blow molding, film blowing, thermoforming and fiber spinning involve the application of an extensional deformation to polymer melts; the deformation process is comparable to a balloon or bubble gum being blown into a sphere. Successful products depend on the ability of the polymer melt to sustain large deformation without breaking or collapsing and can be quantitatively described by the extensional viscosity.
Compared to shear viscosity, extensional viscosity measurements are extremely sensitive to the molecular structure. Polymers with high degree of Long-Chain Branching (LCB) display a strain-hardening effect during elongational deformation, especially at increasing speeds. This behavior indicates a higher melt strength during extensional processes, which helps to stabilize a bubble and prevent collapsing, or avoid thin fibers breaking. Conversely, polymers with a linear morphology (no branching) often fail to process successfully.
This critical performance differentiation is not adequately detected by traditional flow measurements. Extensional viscosity measurements can be easily made on rotational rheometers using the Extensional Viscosity Accessory (EVA).
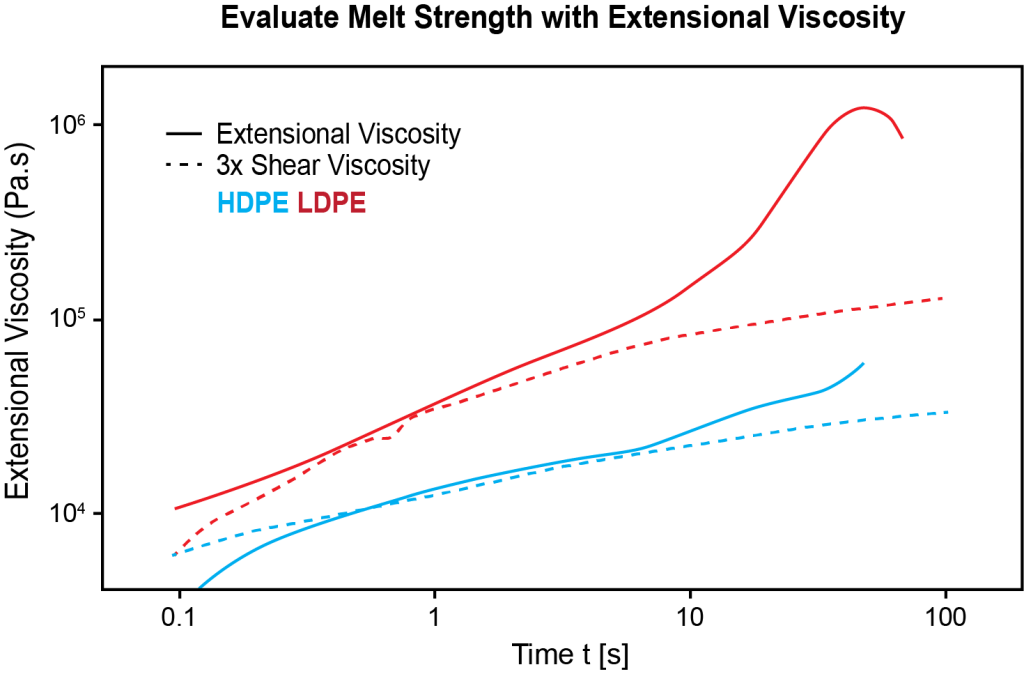
Answer the following questions with extensional viscosity measurements:
- Processability: What is the melt strength of this resin? How much stretching can the bubble withstand before it breaks?
- End-of-life: Do the processing parameters need to change for this batch with recycled resins? What additives are needed to process this batch of recycled resins into a film? (e.g., chain extenders)
How do process conditions affect the product’s crystallinity?
Semi-crystalline thermoplastics like Polyethylene (PE), Polypropylene (PP), and Polyethylene Terephthalate (PET) find extensive use across a range of applications, including in packaging materials. Semicrystalline polymer morphology is marked by the presence of locally ordered, crystalline regions interspersed between disorganized, amorphous regions. The presence of these crystalline domains within the structure confers desirable end-use properties including increased strength, wear performance, and chemical resistance. However, it is vital to carefully control the processing conditions to achieve the required levels of crystallinity in the product since high crystallinity can lead to brittle products, reduce optical clarity, or result in warpage and shrinkage defects.
Crystallization is the process of converting an amorphous, higher-energy structure into an organized, lower-energy, solid crystalline structure – this transition releases energy and can be accurately measured using Differential Scanning Calorimetry (DSC) as an exothermic peak. DSC tests are commonly performed in 3 distinct steps involving a heat-cool-heat cycle. The first heat cycle evaluates the material as received and imparts a uniform, well-defined thermal history to the materials.
Once melted, the cooling cycle of a DSC curve provides information about crystallization – the temperatures at which crystallization starts and ends, and a quick overview of crystallization kinetics. Additional insights into crystallization kinetics can be obtained through more detailed isothermal tests. The amount and speed of crystallization can be controlled through the deliberate addition of nucleating agents; however, crystallization rates can also be affected by dyes, colorants, or contaminants in recycled resins that can serve as nucleating agents. Since crystallinity has a direct impact on product performance, careful measurement and control of crystallinity is critical to avoid product failures in the end-use application.
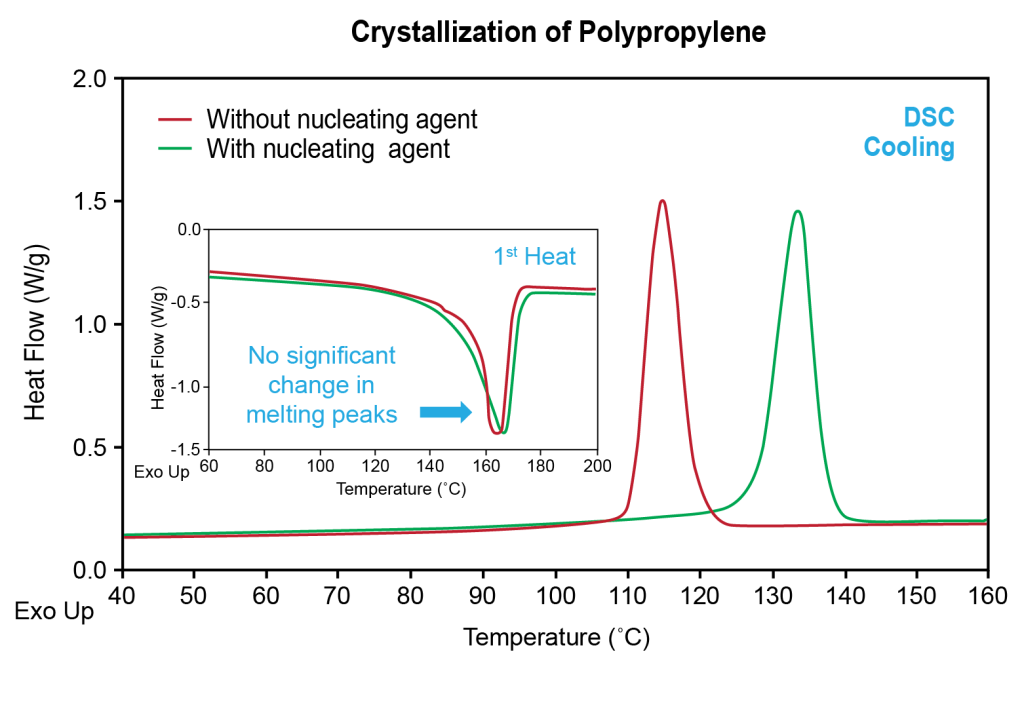
Answer the following questions with results from your DSC:
- Processing: What cooling rates are needed to achieve the required crystallinity? Are nucleating agents needed?
- End-of-life: How can the crystallinity of products made with PCR be matched with those from virgin materials?
Related Application Notes:
How does the product perform?
Understanding the product performance under final end-use application conditions helps guide product formulation, process optimization, and plays an important role in troubleshooting and failure analysis. For plastic products, the mechanical properties are closely tied to the end-use product performance and can be evaluated through a combination of different mechanical testing techniques that provide information on the material’s modulus. Depending on the type of deformation, additional information and insights can also be obtained.
- Monotonic testing: Unidirectional deformation to failure under an applied load – test materials under conditions of increasing load (e.g., Stress-strain curves)
- Fatigue testing: Understand damage and failure from repeated loading – test materials and finished products under conditions of increasing cycling (e.g., S/N curves)
- Dynamic Mechanical Analysis (DMA): Study solid viscoelastic properties as a function of temperature and deformation frequency (e.g., Glass transition temperature (Tg), Time-Temperature Superposition (TTS))
DMA testing investigates the temperature dependance of a solid specimen’s mechanical properties under bending, compression, or tensile deformation. It provides quantitative information about the material’s viscoelastic properties through the Storage Modulus (E’), Loss Modulus (E”) and tan(δ) (damping factor). When polymeric specimens are heated, they undergo transitions that are reflected in these mechanical parameters. DMA is one of the most sensitive techniques available to measure glass transition and beta transition temperatures, since it picks up on subtle changes in local polymer mobility brought about by the increased temperature.
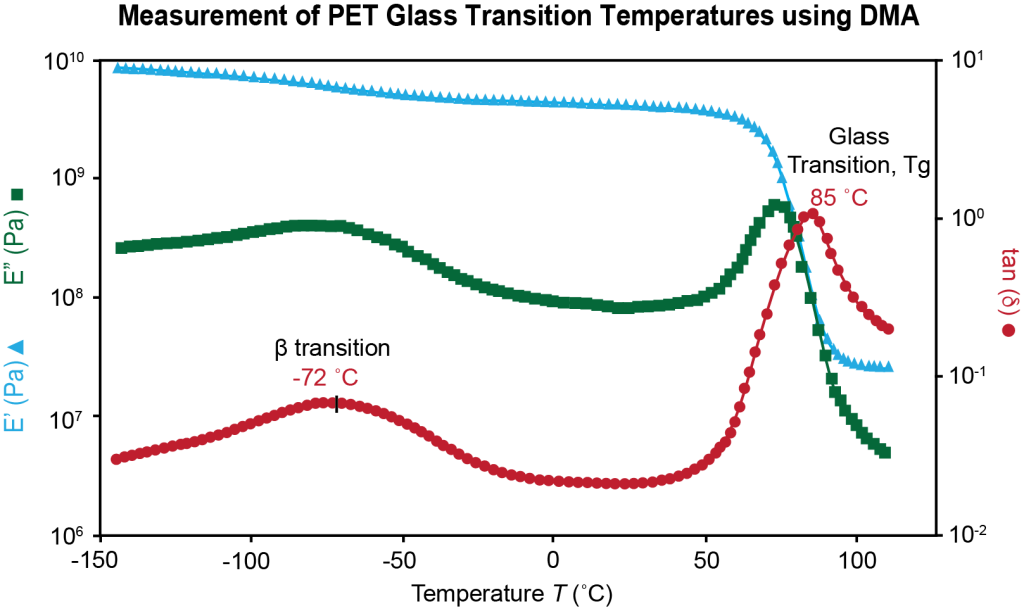
Answer the following questions with results from your DMA:
- Processing: Was this batch of resins blended uniformly to achieve miscibility?
- Product performance: Does this product have the right mechanical strength/ stiffness for the intended end-use environmental conditions (temperature, relative humidity)?
- End-of-life: Do products produced with recycle resin match the mechanical properties of those made with virgin resins?