Keywords: TMA, DSC, Thermal Analysis, Dimensional Change, Phase Transitions
TA120
Summary
Thermomechanical Analysis (TMA) has traditionally been used to measure dimensional changes of solid materials. However, the technique can also be extended to the evaluation of liquid samples, providing an alternative thermal technique to Differential Scanning Calorimetry (DSC ) for determining phase transitions and glass transition temperatures.
Introduction
Thermal analysis methods are especially useful for the petroleum industry. Experiments are fast, reproducible, and require small quantities of sample (milligrams). Traditionally, DSC and DTA have been standard methods for this industry detecting glass transitions, specific heat, wax dissolution, crystallization temperature, melting, oxidative stability and decomposition transitions. DSC has been used in characterizing crude oils, refined oils, and a variety of finished products including lubrication oils, paraffin wax, petroleum, asphalt and petroleum coke (1-5). TGA which measures weight changes, has been used to study the composition and thermal stability of petroleum products.
While TMA, which monitors a material’s dimensional change with temperature, traditionally has been used to evaluate solid petrolem-based materials such as paraffin wax and asphalt, it can also be extended to include the characterization of low temperature properties of liquid petroleum samples. New generation TMA’s with increased sensitivity (100 nm), better cooling capabiliy, and precise and reproducible sample/probe alignment are particularly ideal for these applications.
Experimental
In the standard TMA configuration, the sample is positioned on a quartz stage and a moveable probe is placed on the top of the sample. The dimensional changes occurring as a function of time, temperature or force are monitored by a linear variable differential transformer (LVDT) attached to the probe. The furnace, surrounding the sample stage and probe, provides heating/cooling during the measurement. A thermocouple adjacent to the sample monitors sample temperature so that the dimension change can be followed as a function of temperature. There are several available probes (expansion, penetration, macroexpansion, hemispherical) which can be used to vary probe contact and force on the sample in order to obtain optimum results.
There is another TMA configuration (tension mode) for measuring the stress/strain properties of films and fibers. In this configuration, the sample is suspended in the vertical direction between the probe and stage assembly using stainless steel clamps or crimped-on aluminum spheres.
Both of these configurations are useful for evaluating liquid samples. Two specific experimental methods are described below.
Method 1: Absorption of a Liquid on Fiber
This measurement is based on saturating an absorptive fibrous substrate with liquid sample. The TMA is set up in the fiber tension mode. Cleaved aluminum balls are crimped on the ends of a cotton fiber, which has been soaked in liquid until saturated. Care must be taken to remove any excess liquid from the aluminum balls before positioning the fiber between the sample holder and probe.
For the petroleum products studied here, the TMA furnace was cooled to -150 °C, before adding a 5 gram load to the mounted fiber. The TMA furnace was programmed to heat the material at a rate of 5 °C/min under a helium purge adjusted to a flow rate of 100 ml/min. The sample temperature was monitored using the sample thermocouple positioned midway on the fiber.
Method 2: Penetration of a Solidified Sample
This measurement is based on cooling the liquid sample below its freezing point and conducting a penetration experiment. The onset of penetration marks transition temperatures. Specifically, the TMA is configured with a hemispherical probe and a DSC pan is used to contain the liquid sample.
For petroleum products, the TMA furnace was cooled to -150 °C before the probe was lowered to the top of the sample and a 5 gram load was applied. The sample was heated at a rate of 5 oC/min, in a helium environment adjusted to a flow rate of 100 ml/min.
Results
The utility of the two TMA liquid sample methods is demonstrated in the measurement of the melting transition of highly pure water. Both the fiber tension method (Figure 1) and the penetration method (Figure 2) similarly identify the transition temperature as 0.0 °C.
A blank run using just the cotton fiber shows no transition over this temperature range except that of a trace of moisture absorbed from air during the experiment.
A plot of the first derivative is also shown for each of these thermal curves. As the complexity of the sample and number of transitions increase, the usefulness of the derivative (dimensional change per unit of time) to identify and separate transitions increases dramatically. The relative differences in the derivatives between thermal curves can be directly related to compositional differences between the samples.
When using the fiber tension method, the load is not applied until the temperature is below all of the transitions. This ensures that the substrate (cotton fiber) bears no tension until the sample liquifies. Therefore, all dimensional displacements observed are attributed to changes in the sample, not the substrate.
When using the penetration method, the most dramatic displacement occurs as the sample liquifies and the probe totally penetrates the sample to the bottom of the sample pan. Any smaller displacement before full penetration is the result of transition of the sample in the solid state.
Analyses of five petroleum samples (two engine oils, a crude oil, a petroleum distillate and a pure hydrocarbon) are shown in Figures 3 through 12. The transitions observed by TMA are characteristic of the individual samples:
- The glass transition temperature (Tg) of engine oil #1 is observed at -66 °C to -70 °C, and wax dissolution occurs at – 42 oC to -36 oC (Figures 3 and 4).
- The Tg of engine oil #2 is observed at -64 °C, while a larger amount of wax (as compared to oil #1) is evidenced by the second transition at -39 °C to -44 °C (Figures 5 and 6).
- The Tg of the crude oil is located near -58 °C and wax dissolves at -10 °C (Figures 7 and 8).
- VM&P Naphtha, a multicomponent petroleum distillate with a boiling range of 240 to 330 oF, has a series ofcharacteristic melting temperatures between -117 °C and -52 °C. These are indicative of the components and relative content of this aliphatic hydrocarbon mixture (Figures 9 and 10).
- The melting point of pure heptane is seen as a highly reproducible, sharp transition at -85.3 °C. This agrees well with other methods used to determine this melting temperature (Figure 11 and 12).
Figures 13 and 14 illustrate the excellent reproducibility obtained for both TMA methods. For the samples evaluated here, the fiber tension mode appears to be the more sensitive method for detecting subtle transitions.
Figure 15 is the DSC curve for engine oil #2. This curve illustrates that the TMA results not only agree well with the DSC results, but in addition may be easier to interpret.
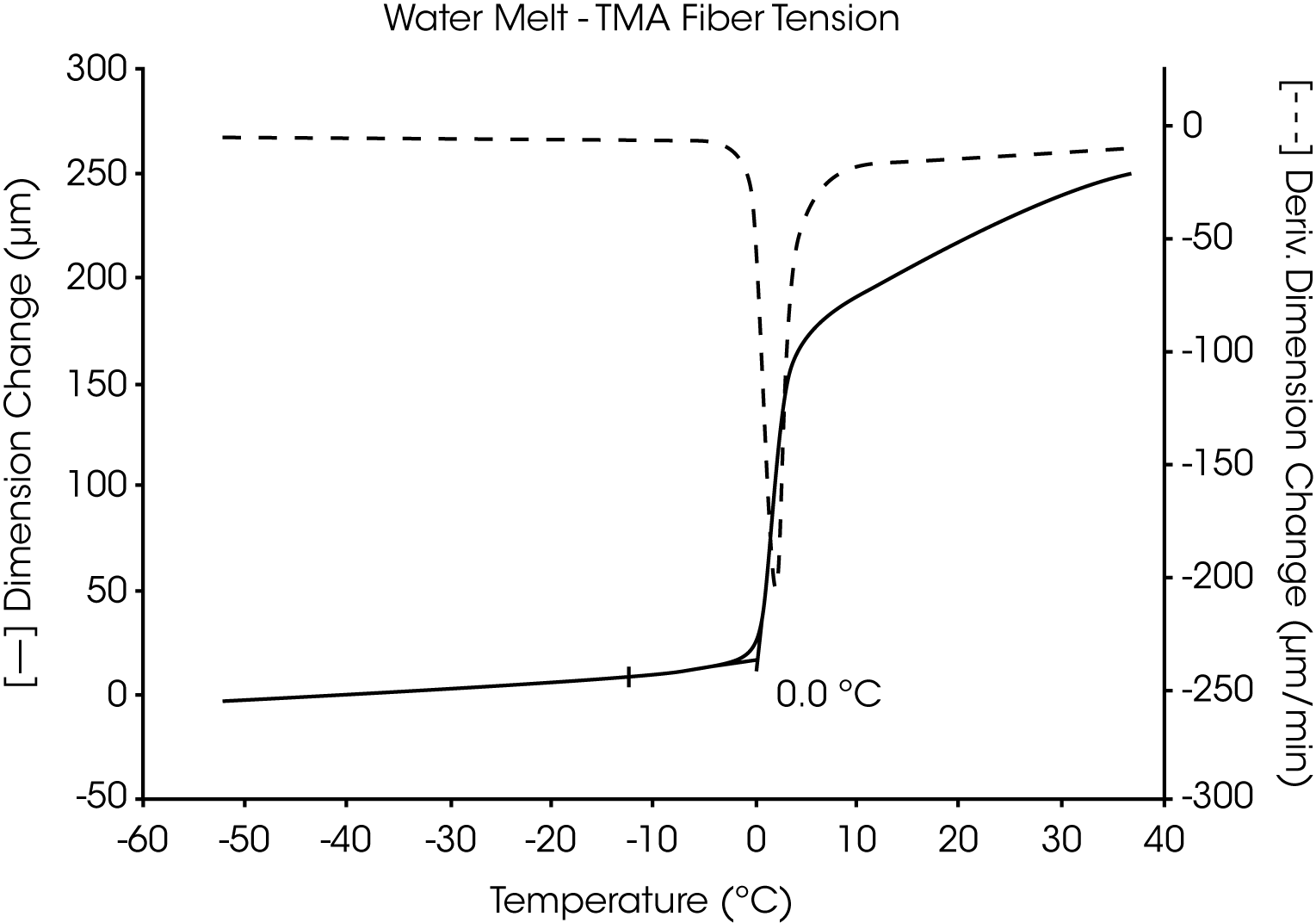
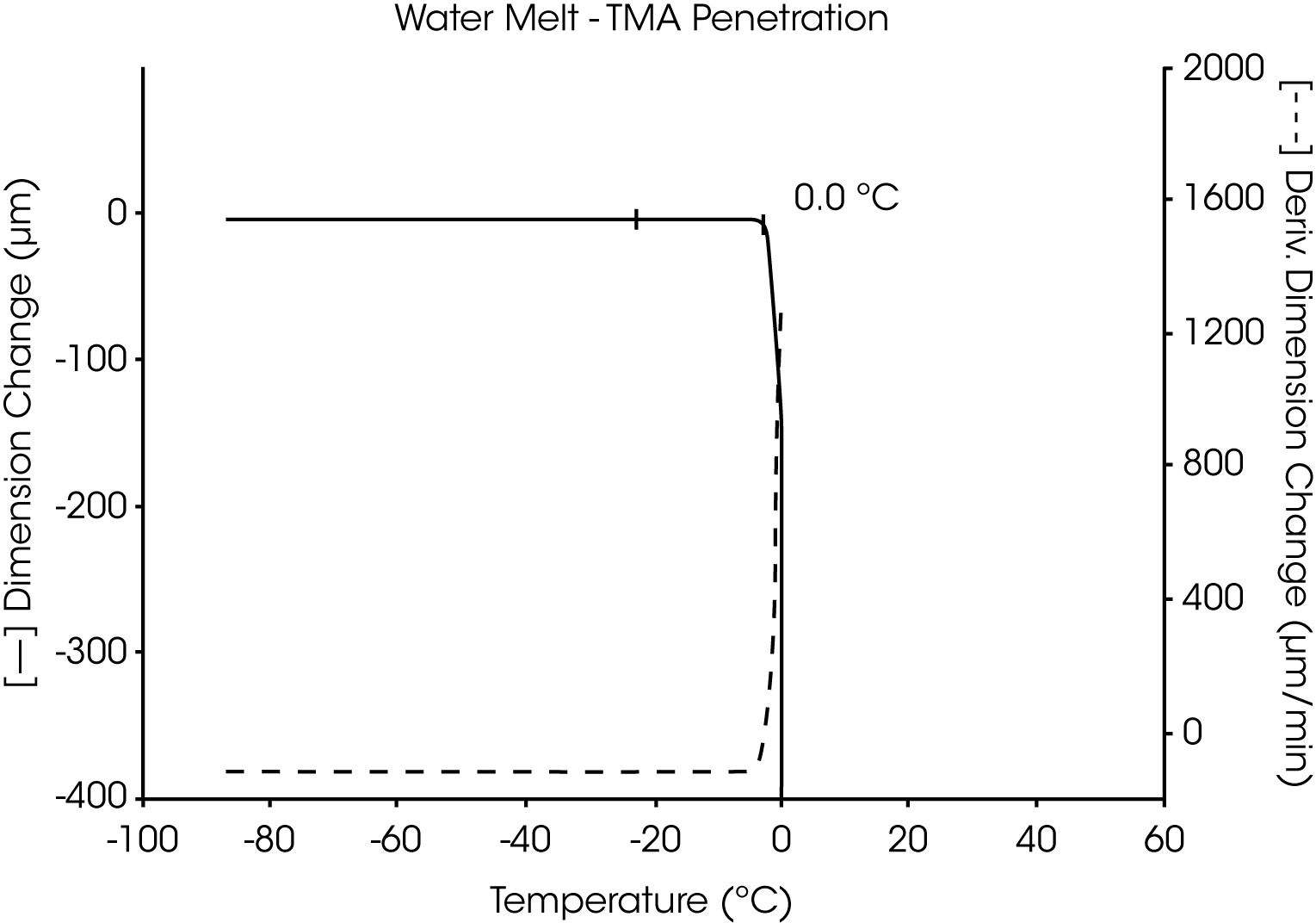
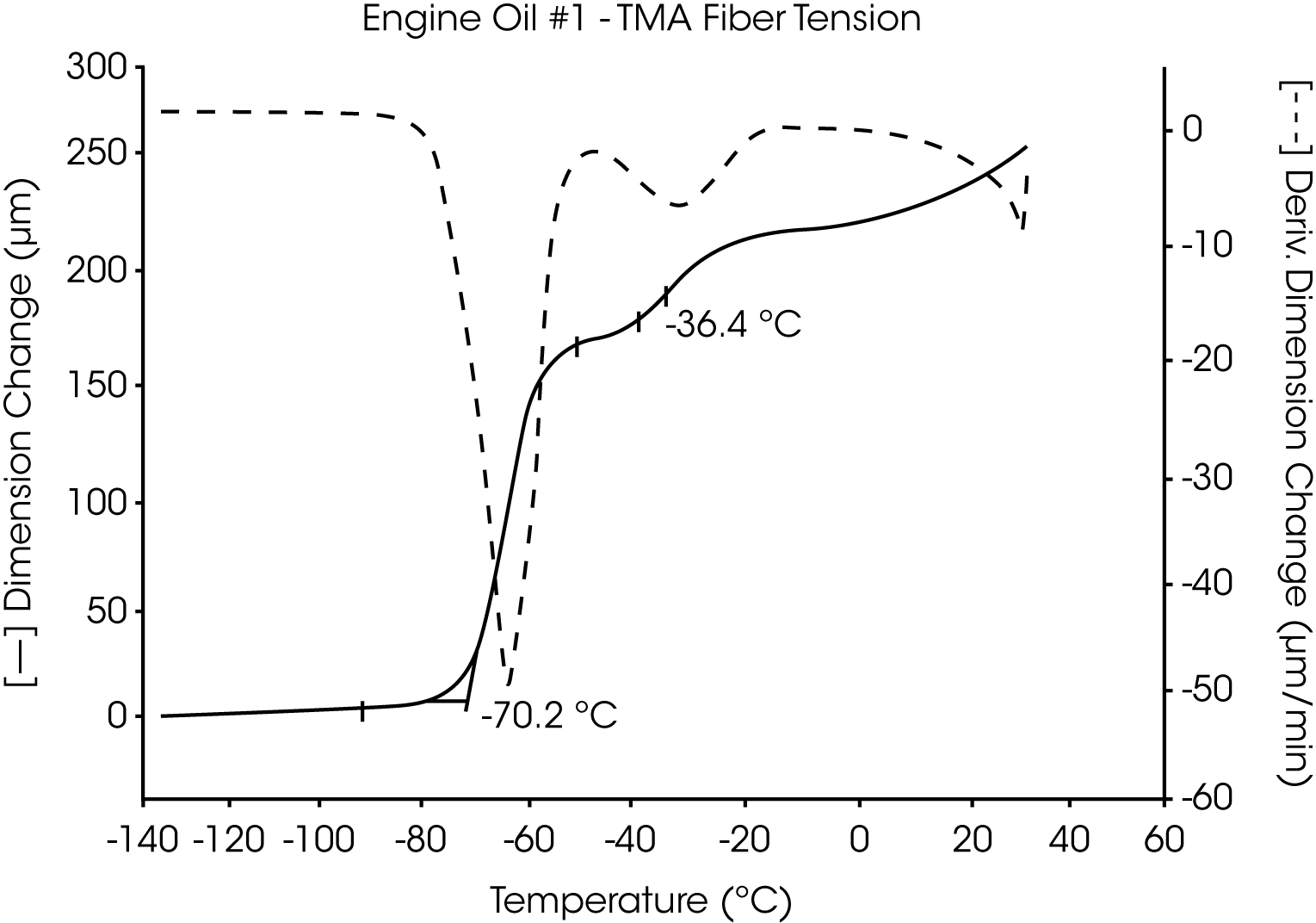
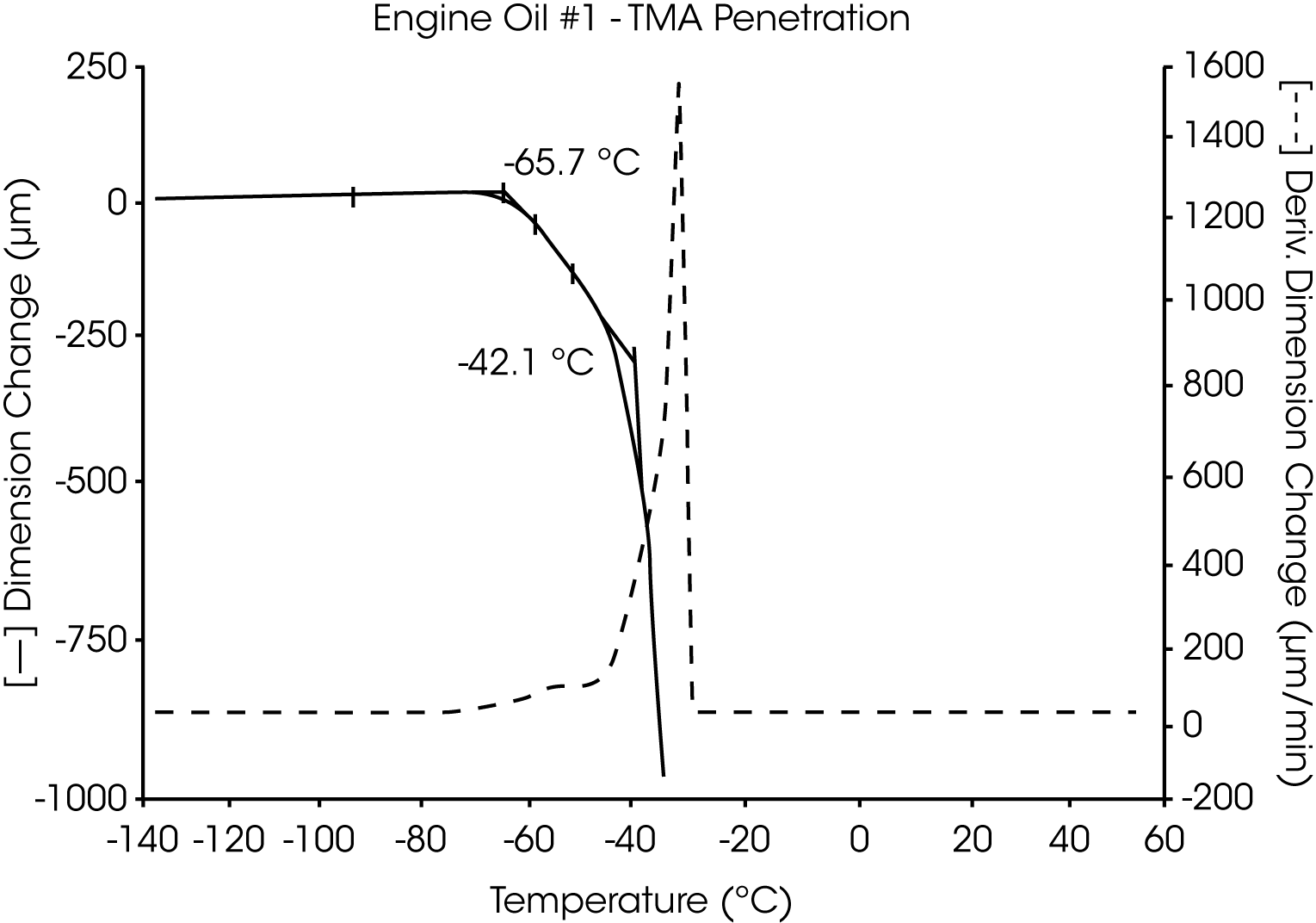
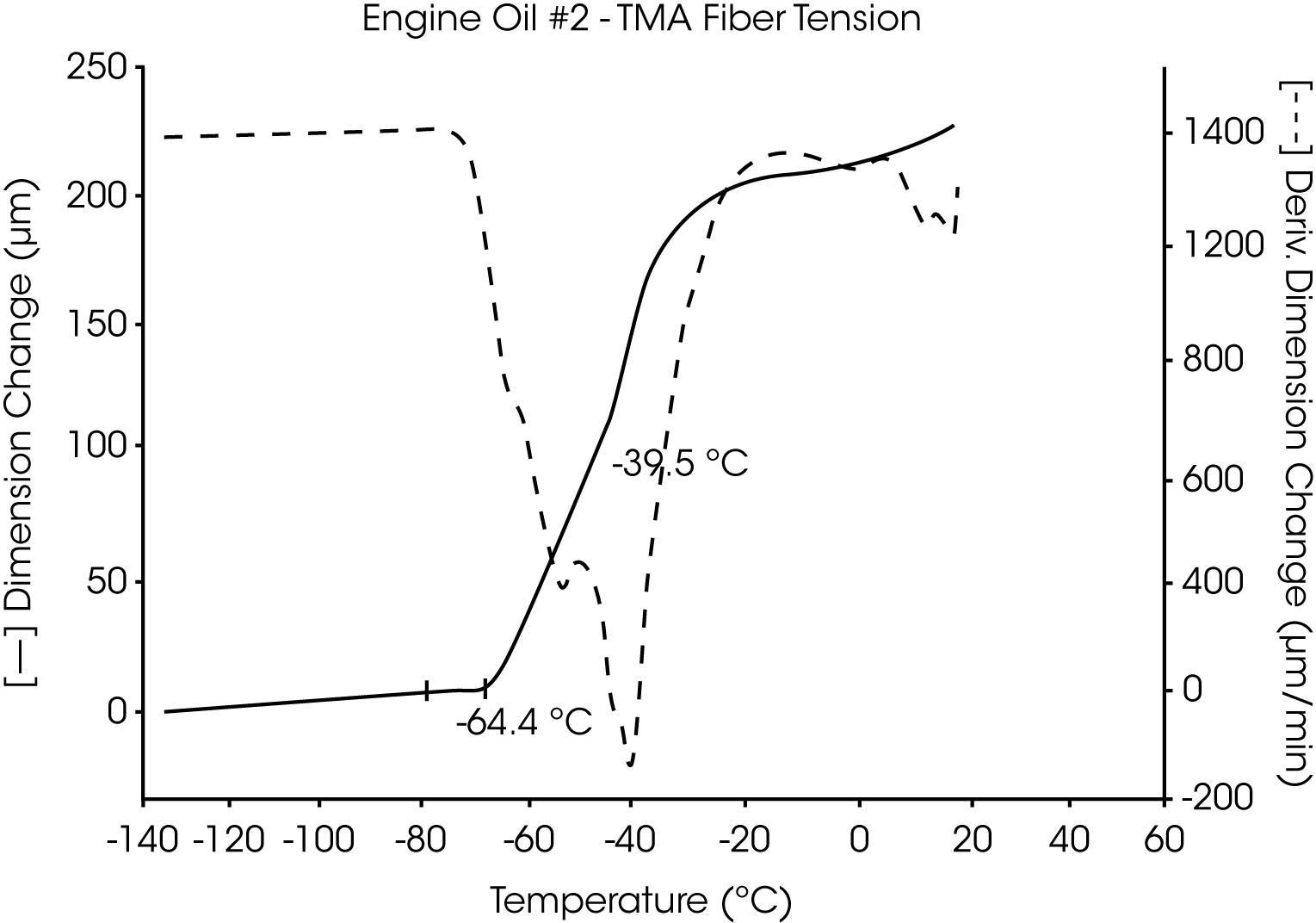
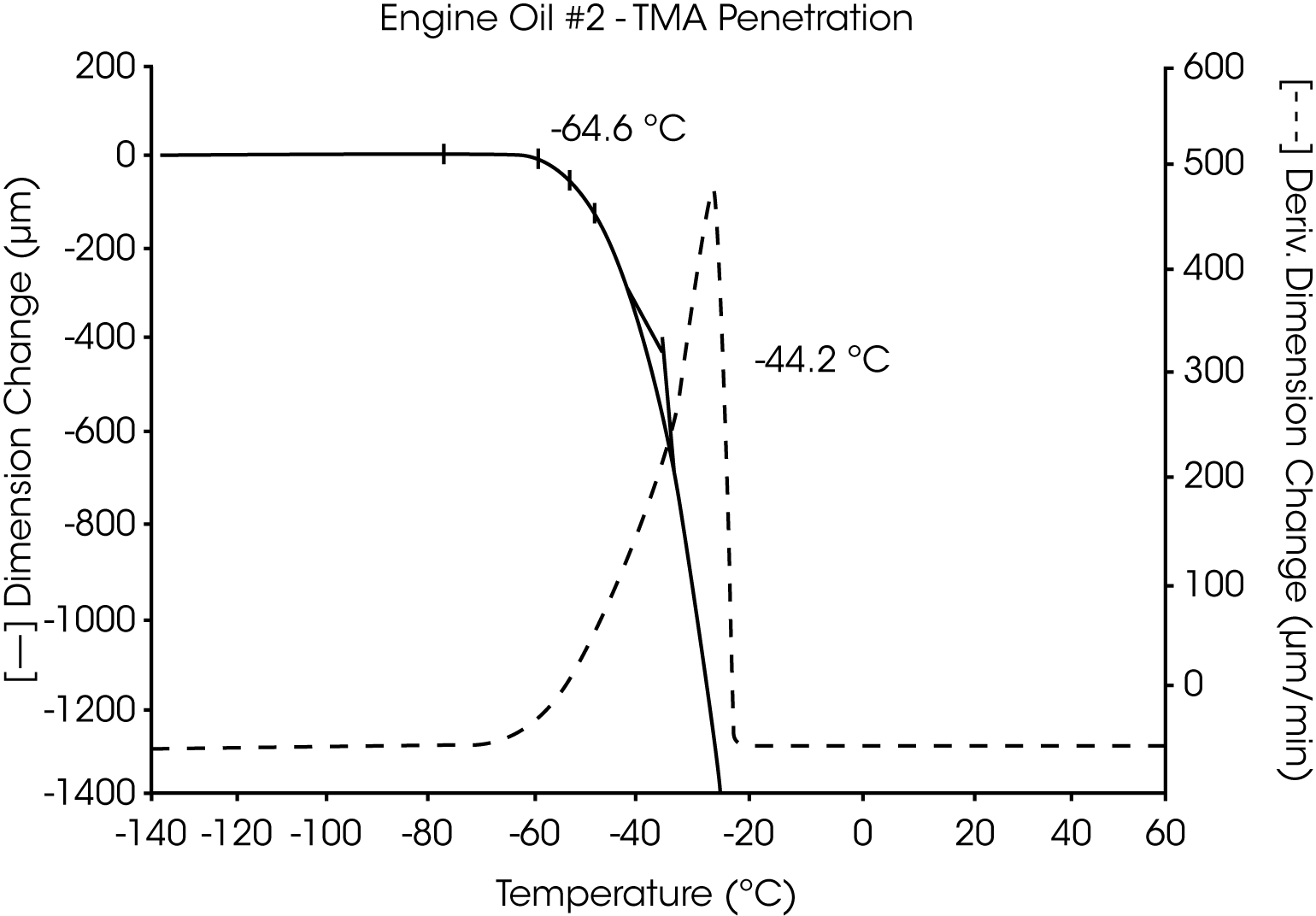
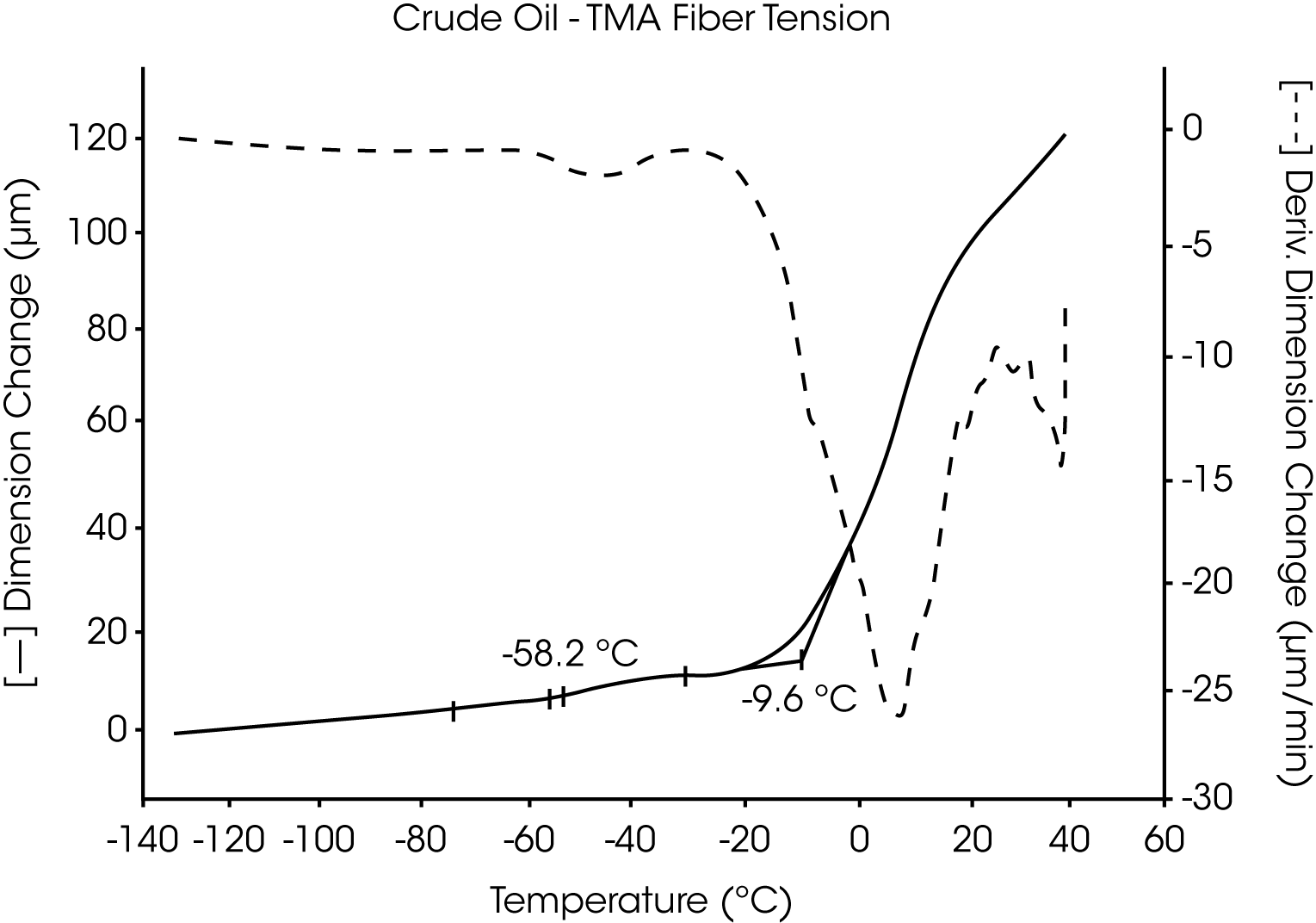
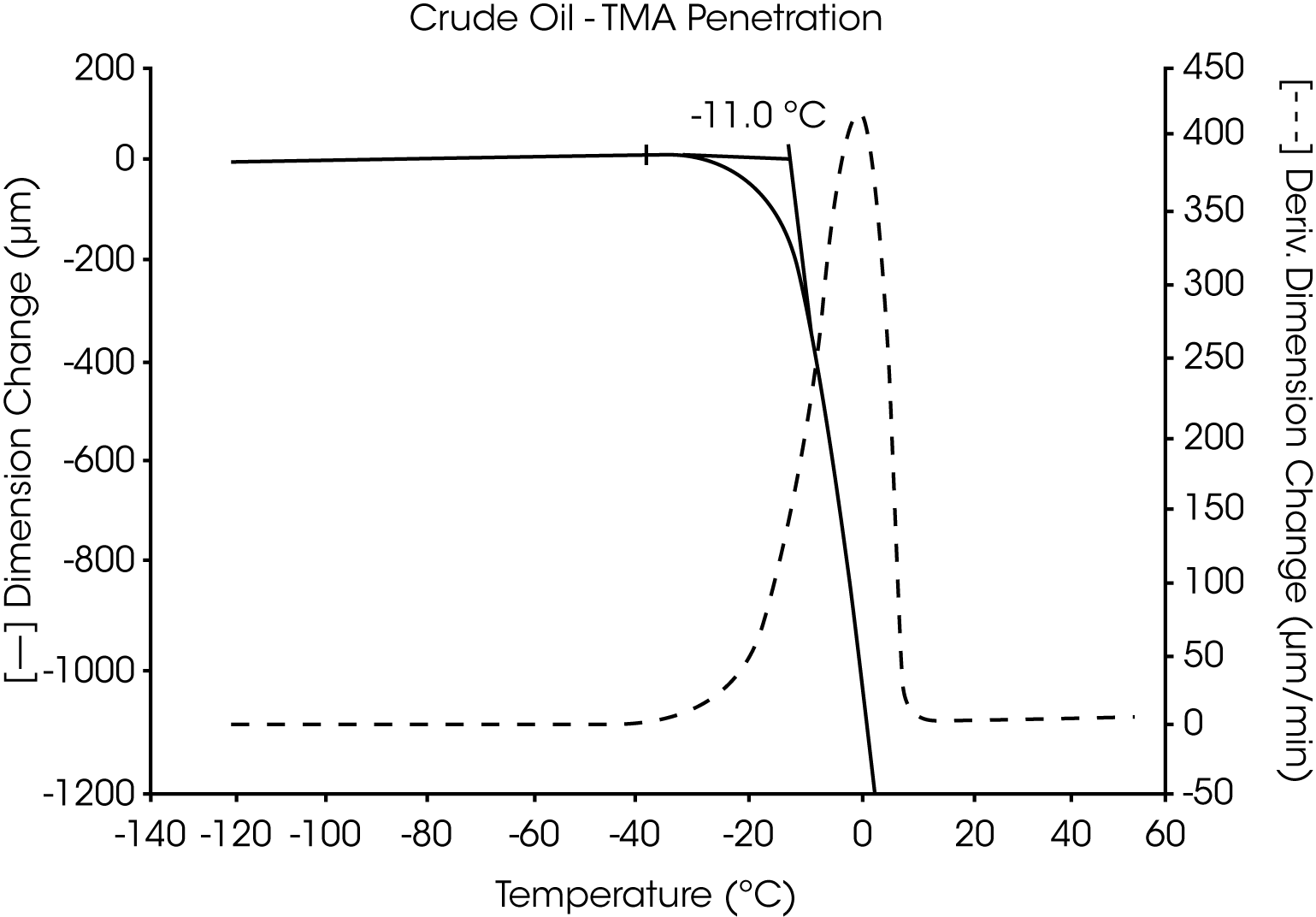
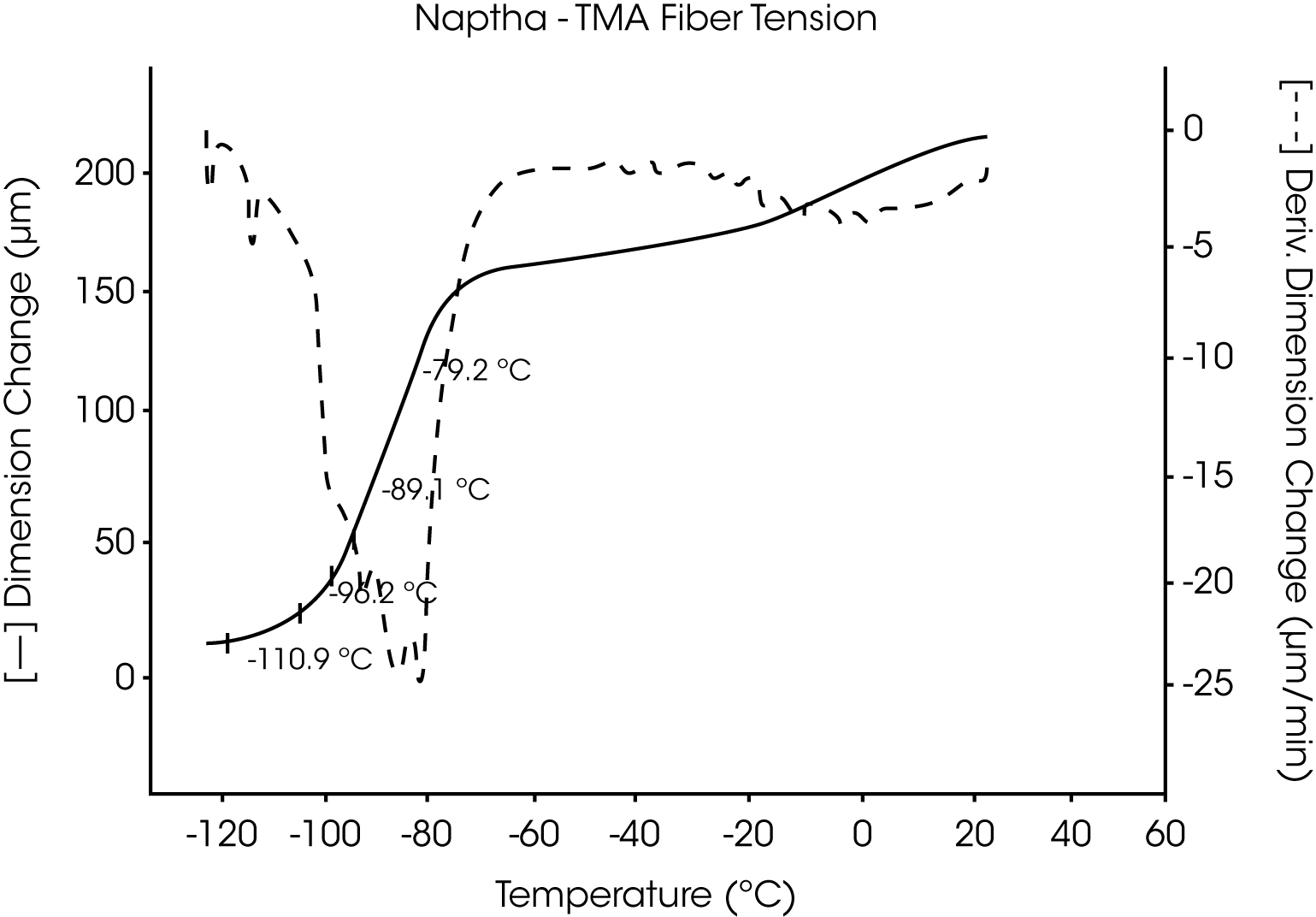

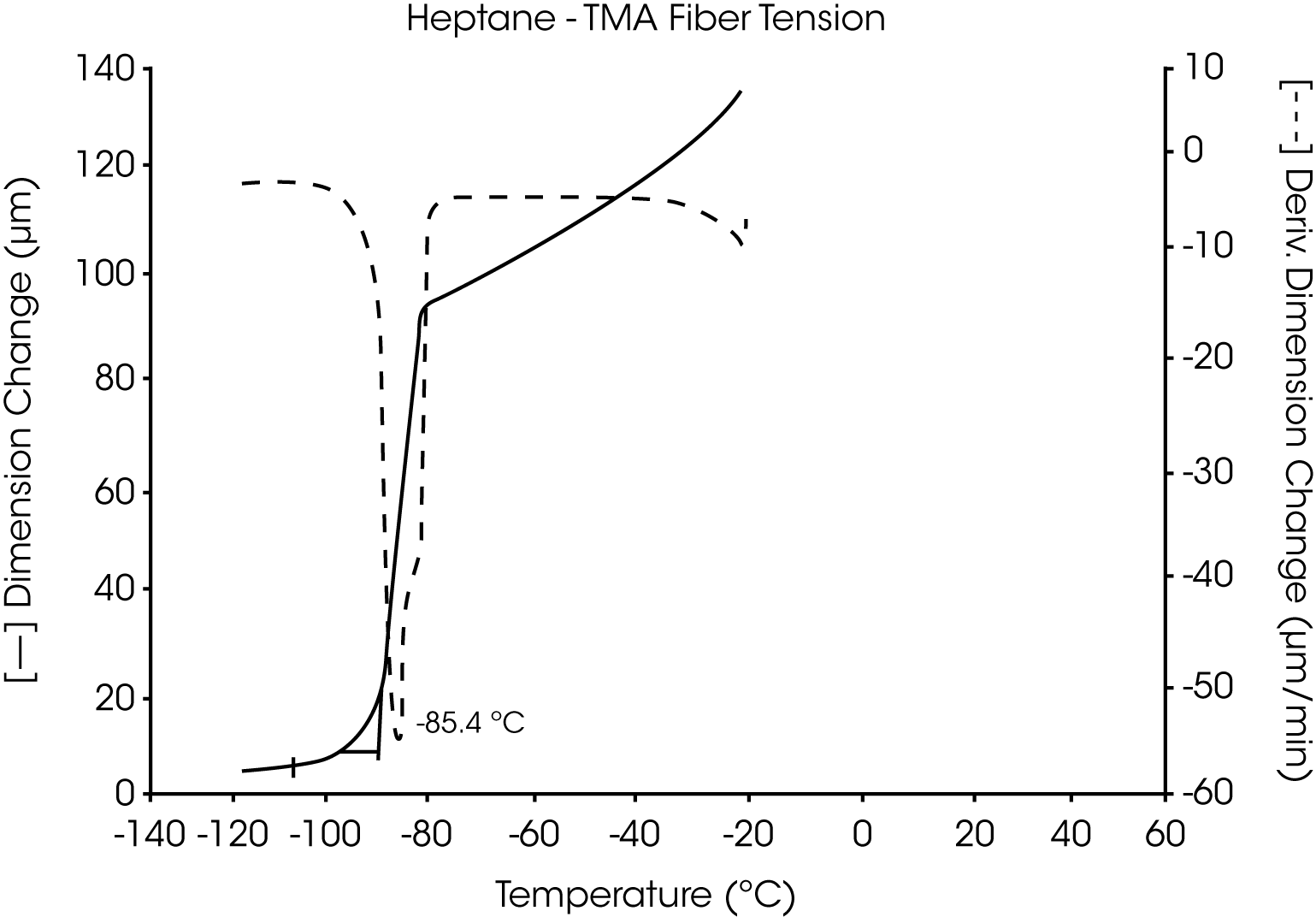
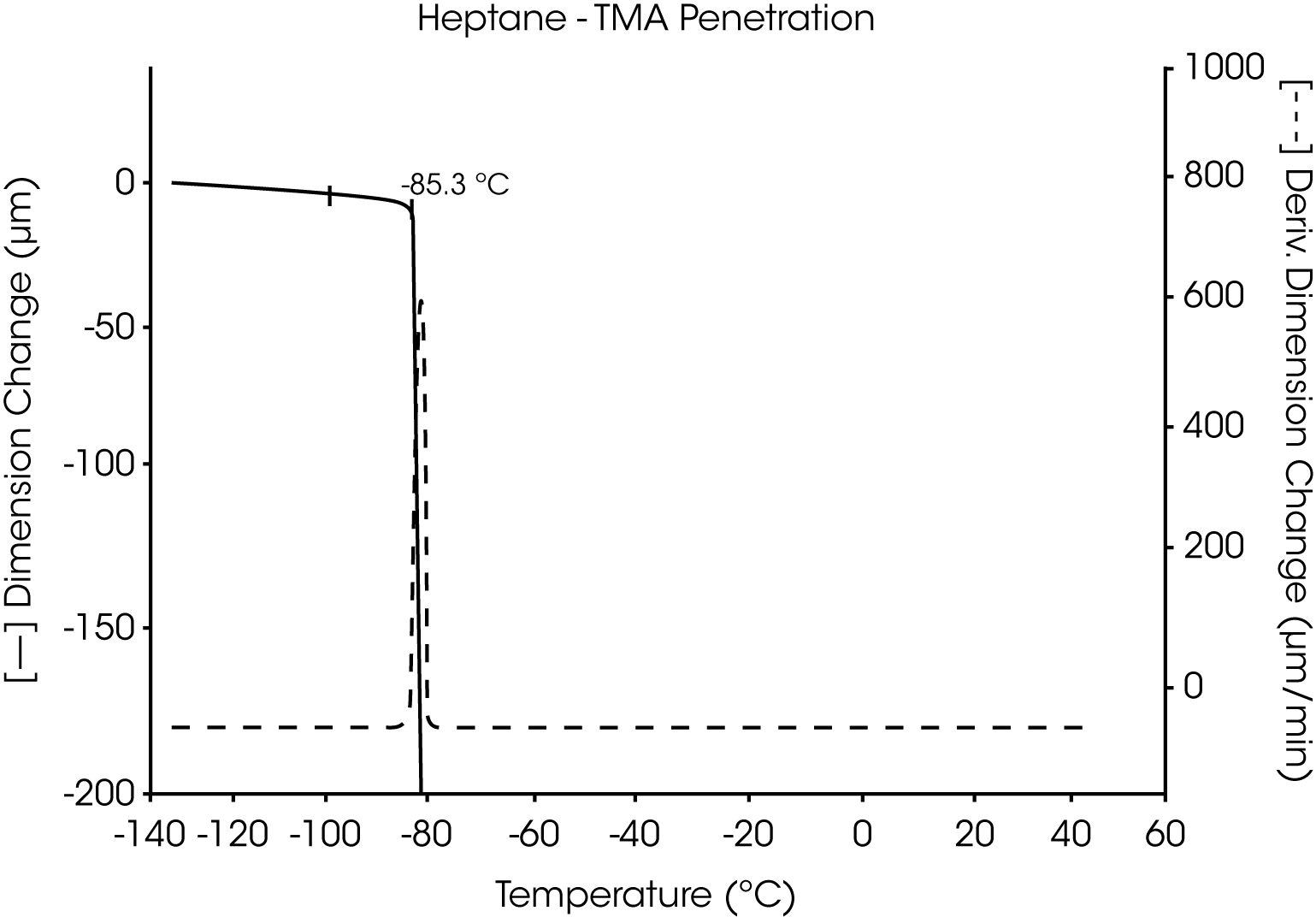
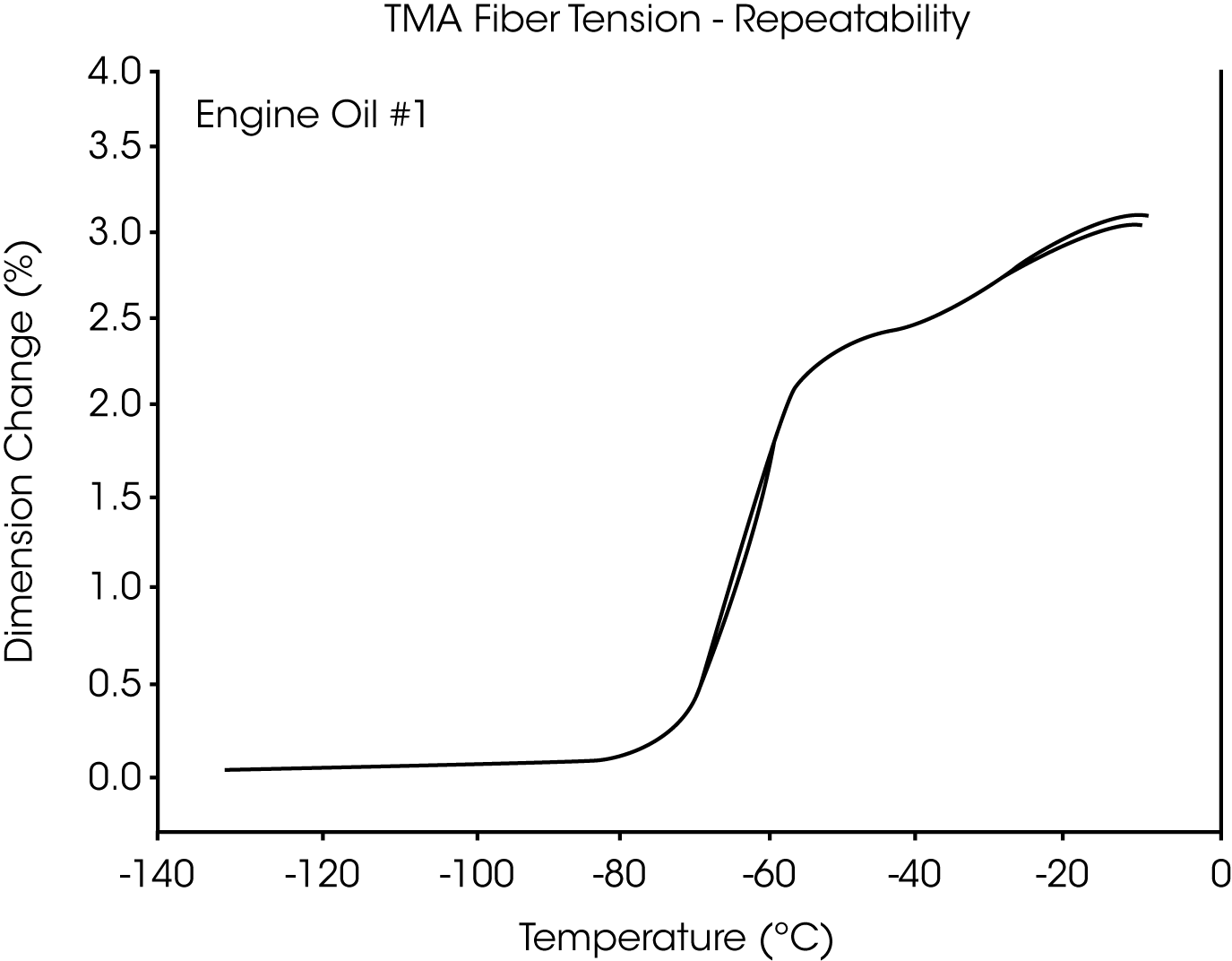
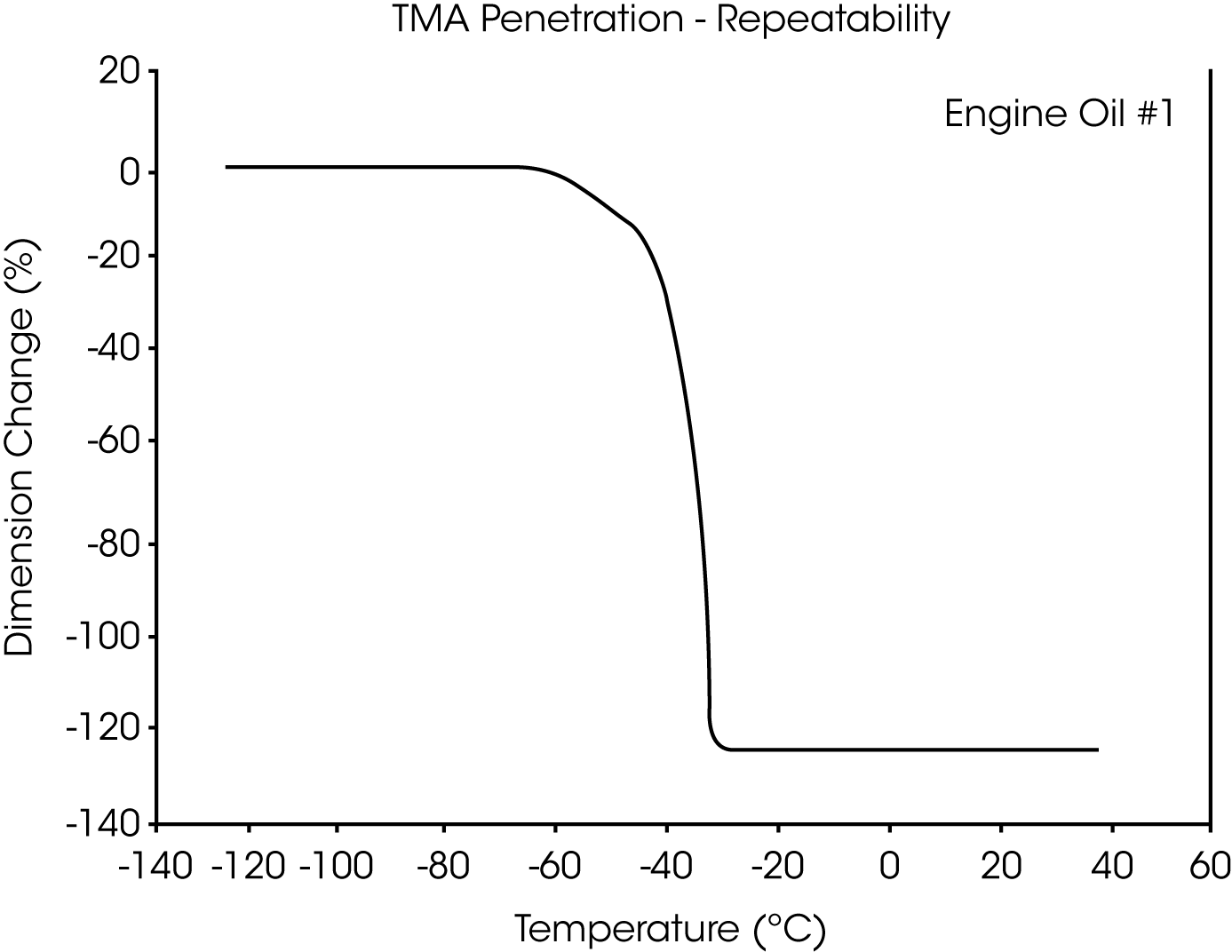
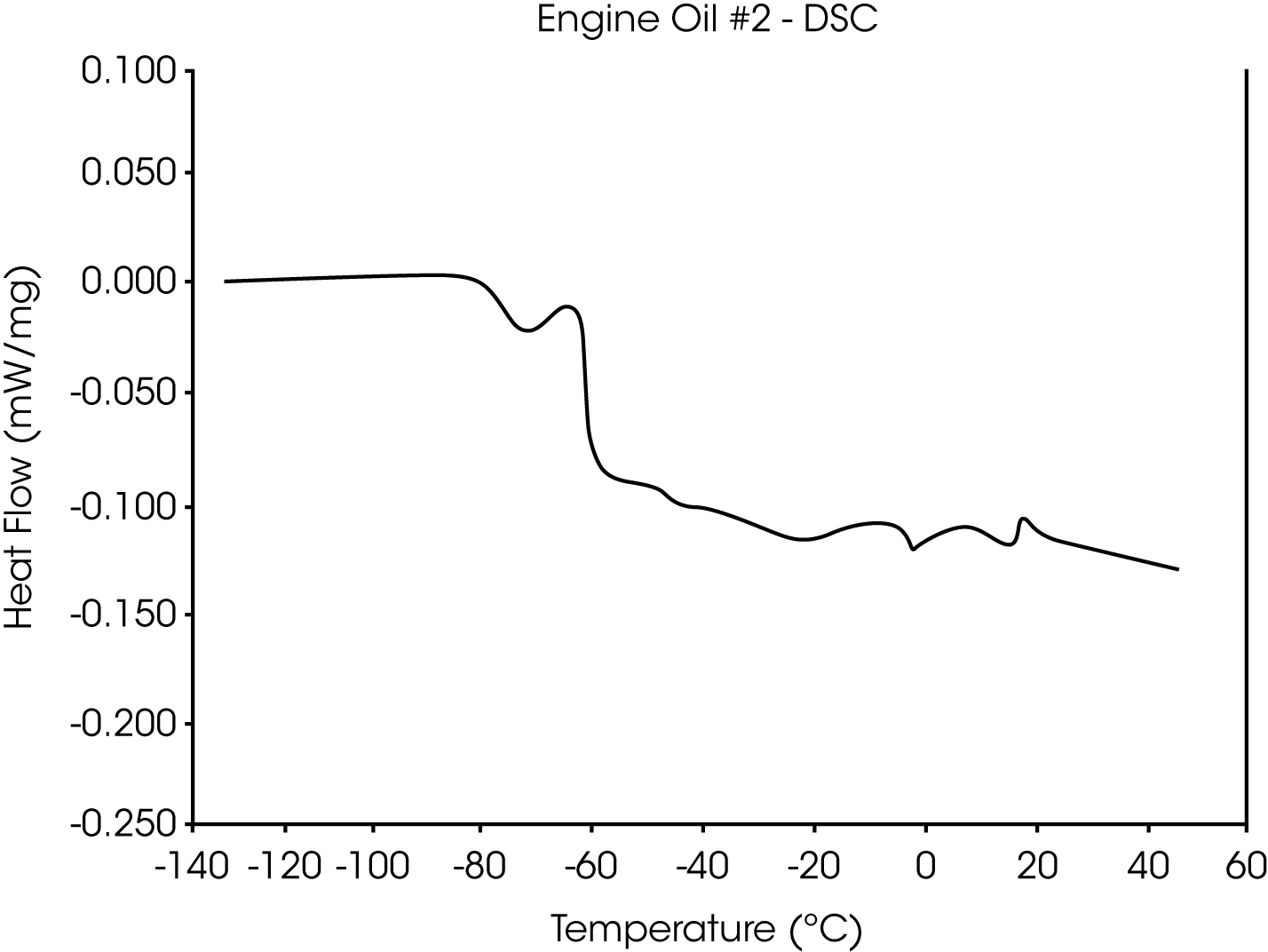
References
- Blaine, R. L., Am. Lab., January, 1974
- Kalmutchi, G., Rev. Chim. (Burcharest), 27(1), 67-70, 1976.
- Noel, F. and Cranton, G.E., Am. Lab., 11(6), 27-50, 1979.
- Wesolowski, M., Thermochim. Acta, 46(1), 22-45, 1981.
- Walls, S. R., Anal. Proc. (London), 22(2), 44-46, 1985.
Acknowledgement
Click here to download the printable version of this application note.