Keywords: Oxidative Stability, Polyethylene Terephthalate
TA121
Summary
Oxidative stability is an important polymer property to fiber producers, since a polymer with low stability can cause processing problems. Differential scanning calorimetry (DSC) is an effective technique for rapidly evaluating the oxidative stability of polymers and enables fiber producers to determine optimum formulations.
Introduction
Many properties of a polymer fiber are dependent on the resin “recipe,” which includes copolymers such as diethyleneglycol or adipic acid, polymerization catalysts, and optical brighteners. These additives can affect the thermooxidative stability of the resin.
The concept of oxidative stability is important to fiber producers, since a polymer with low stability can undergo a drop in its molecular weight during the spinning process and also is more prone to the formation of gels. This can lead to a variety of problems, including discoloration, high plugging rates, broken filaments and texturing problems.
An increase in the oxidative stability of a polymer can be achieved by two means: addition of an antioxidant, or selection of standard polymer additives which promote oxidative stability in addition to their normal functions.
Differential scanning calorimetry (DSC) which measures heat flow into or out of a material as a function of temperature is an extremely effective technique for evaluating the effectiveness of various additives with regard to oxidative stability. The oxidation process is accompanied by significant heat evolution (1), and the high sensitivity of DSC makes possible the use of small samples. DSC has been used successfully to study the oxidation of a wide variety of products including lubricants (2), greases (3), fats and oils, polyolefins (4, 5) and rubbers (6).
To distinguish between stabilities resulting from various resin formulations, the DSC conditions need to be optimized. This may be done in three ways: (i) testing samples with a particle size which has a large surface-to-volume ratio, (ii) scanning at low heating rates, and (iii) increasing the partial pressure of oxygen. The TA Instruments Pressure DSC, which can provide pressure up to 7 MPa (1000 psig), is particularly useful for such studies.
Experimental
Polyethylene terephthalate (PET) is the most widely used polymer in the manufacture of textile fibers. In this study, the effects of different additives on the oxidative stability of PET were evaluated using pressure DSC at 5.5 MPa (800 psig) of oxygen.The PET samples were ground to produce a particle size of approximately 0.25 – 0.40 mm and filtered between two sieves of 20 and 30 mesh size. Approximately 8 mg of the filtered sample was placed in a tared aluminum pan, weighed, and crimped with a lid to assure good sample-pan contact. Five holes were punched in the lid to permit sufficient oxygen exposure.The sample was positioned in the PDSC cell and the cell closed.The flow lines were purged by pressurizing the cell to 0.34 MPa (50 psig) with dry oxygen, then discharging it carefully by opening the exit port at the rear of the cell. Additional purging was accomplished by pressurizing the cell to 50 psig while maintaining a flow of 50 ml/min through the cell outlet valve for 30 seconds. The cell was then slowly pressurized (1-2 minutes) to the operating pressure 5.5 Mpa (800 psig) while maintaining a flow of 50 ml/min through the cell.Once at 800 psig, the cell was heated to 150 ˚C and maintainedisothermally for 5 minutes to drive off any surface moisture.Following the isothermal hold, the cell was heated at 5 °C/min to 300 °C. During this heating, an exothermic transition occurred. The onset temperature of this transition provides an indication of the PET’s oxidative stability.
Results
Figure 1 is a typical trace obtained while heating the PET resin in a pressurized oxygen atmosphere. The trace shows that an exotherm occurs at approximately 225 ˚C. Polymer-analytical investigations indicate that this exothermal enthalpy effect is accompanied by strong degradation of the polymer (1).Following the initial exothermic degradation, the polymer under goes simultaneous melting and degradation. This results in a distinctive undulatory thermogram which may be used to characterize the oxidative stabilities of polyester resins. Figure 2 is a comparison of the stabilities of two PET resins which contain different levels of a calcium ester interchange(EI) catalyst. The resin containing the greater amount of the calcium catalyst exhibits a higher degree of oxidative stability as evidenced by its higher oxidative onset temperature.
Figure 3 is a comparison of the stability traces obtained for two PET resins, one of which contains an antimony polymerization catalyst, and the other, a calcium catalyst. The results show that the resin containing the calcium additive is significantly more stable, as reflected by its higher onset temperature and smaller initial oxidative exotherm.
Other ester interchange catalysts, such as zinc and manganese, have been observed to decrease the oxidative stability of PET (1). Thermal analytical studies have shown that increasing the concentration of diethylene glycol (DEG) significantly decreases the stability of PET (1 ).
If desired, the melting component of the oxidation thermogram can be subtracted out producing a trace showing only the exotherm associated with the oxidative degradation of the resin. This can be done by running a fresh sample under thesame conditions using a dry nitrogen atmosphere instead of oxygen.
The data in both oxygen and nitrogen should be normalized with respect to the sample mass, and can be easily done by dividing all the data points by the respective sample respective sample masses to report the Normalized Heat Flow signal.
The normalized data from the nitrogen run can then be subtracted from the data obtained in oxygen. This results in the generation of a new data file showing the effects of oxidative degradation only. This is shown in Figure 4 for a PET resin containing 100 mg/g of a calcium catalyst.


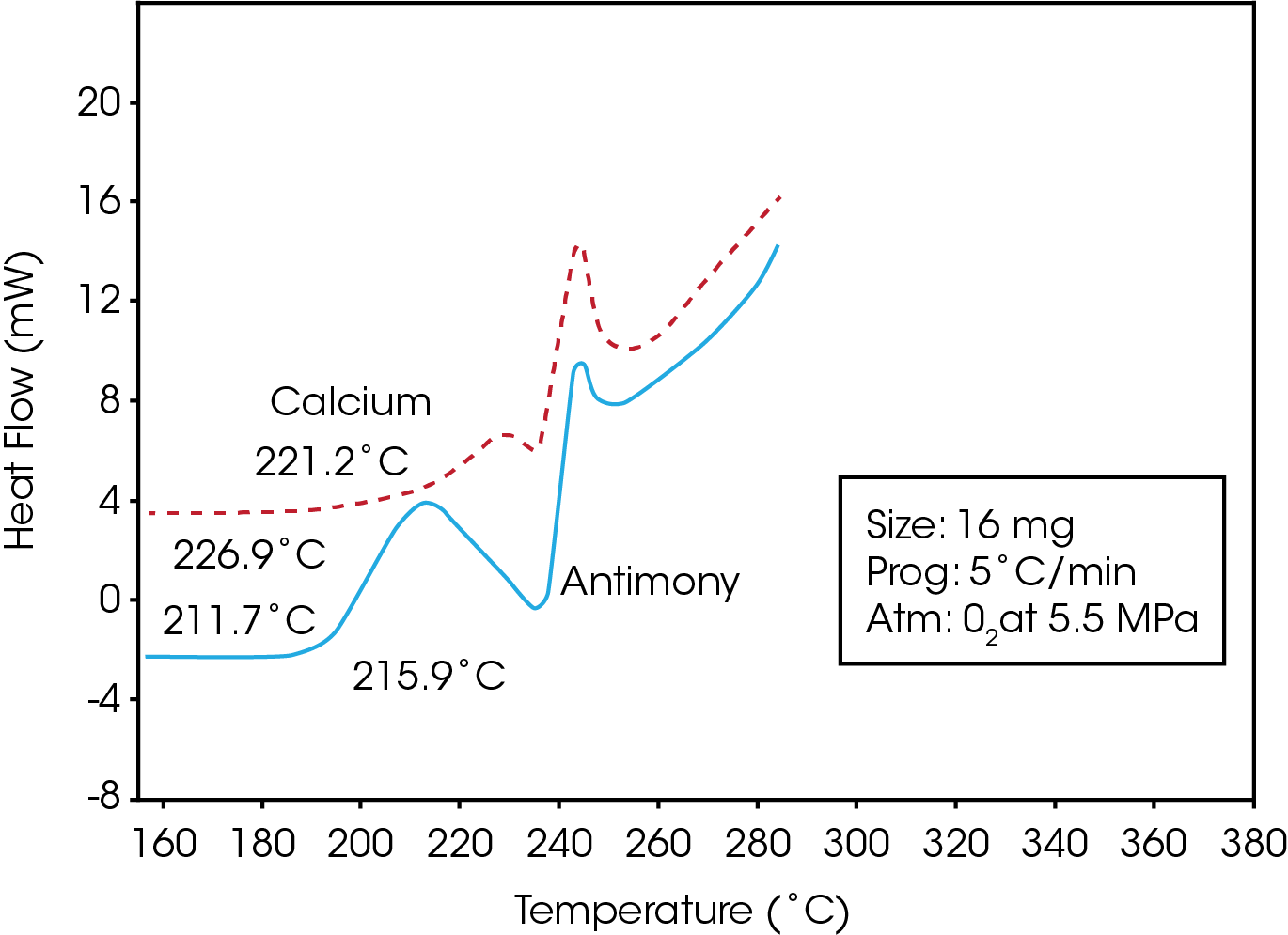

References
- H. Zimmerman, D. Becker, E. Schaaf, J. Appl. Polym. Sci., 35, 183, 1979.
- P. F. Levy, G. Nieuweboer, L. C. Semanski, Thermochim Acta, 1, 429 (1970).
- R. L. Blaine, Am. Lab., 6,18 (1974).
- J. B. Howard, Polym. Eng. Sci., 13, 429 (1973).
- H. P. Frank, J. Polym. Sci., Symp. No. 57, 311-318 (1976).
- M. A. Ponce-Velez, E. Campos-Lope, J. Appl. Polym. Sci., 22, 2485 (1978).
Click here to download the printable version of this application note.