Keywords: DMA, Composites, Thermosets, curing, glass transition (Tg)
TA473
Problem
The end-use properties of thermoset composite materials such as brake linings are dependent on the degree of cure achieved during processing. Various thermal analysis techniques can be used to monitor the cure level in thermosets. Differential scanning calorimetry (DSC), for example, can determine cure level based on the amount of additional curing (with associated heat evolution) that occurs on further heating. Cure level can also be determined from the glass transition temperature (Tg) of the material using DSC or thermomechanical analysis (TMA). Unfortunately, in reinforced or heavily filled composites, detection with these techniques may be difficult.
Solution
Dynamic mechanical analysis (DMA), which measures the modulus (stiffness) and damping properties of materials, provides a more sensitive alternative for determining the Tg in composites. DMA’s sensitivity is based on the significant change in modulus (several decades) and damping which occurs at the Tg. Figures 1-4 show the DMA results for two composite brake lining materials. [DMA Conditions: Vertical clamps; sample size 41 x 14 x 3.6mm3 (normal); frequency 1 Hz; oscillation amplitude 0.2mm; heating rate 3ºC/minute from ambient to 200ºC]. The Tg’s for both materials are easily observed as the peaks in the damping (loss modulus) profiles. Several conclusions are possible from these results:
- Material 1 has a higher Tg than Material 2 in the “as received” condition, as well as a higher modulus before and after the Tg, probably due to different matrix polymers and/or different reinforcement composition and orientation.
- Reheating Material 1 does not increase the Tg as much as reheating material 2. Hence, Material 1 is initially more fully cured.
- The damping profile for Material 2 has a bimodal distribution indicating two different polymers are present.
- Reheating Material 2 causes the modulus before and after Tg to increase and the high temperature damping peak to shift to a higher temperature, indicating that Material 2 is not initially fully cured. The temperature decrease observed for the low temperature damping peak on reheating may indicate some thermal degradation.
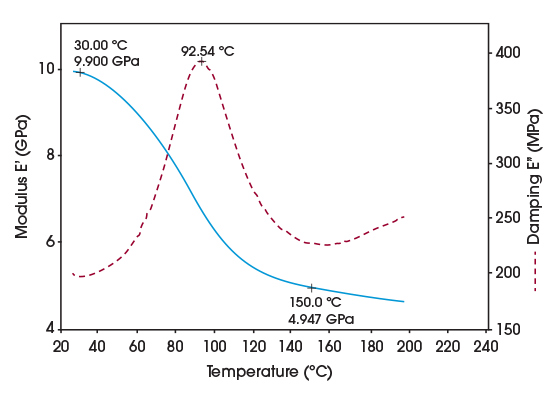
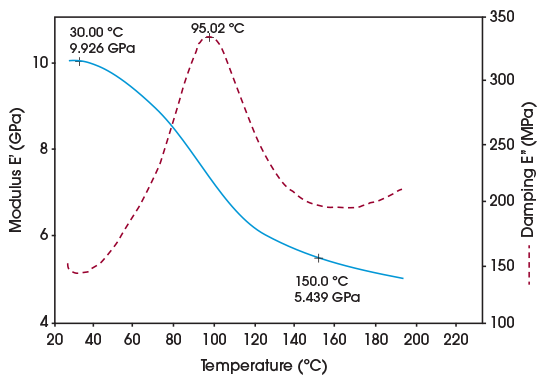
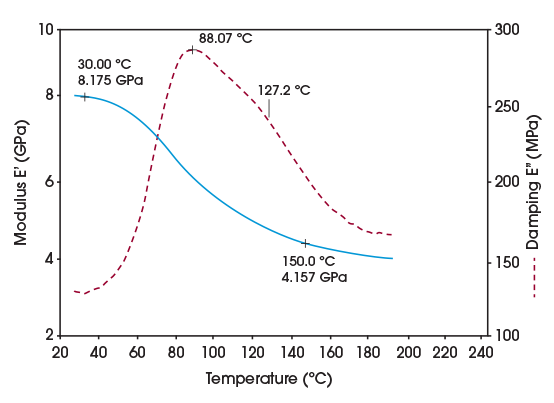
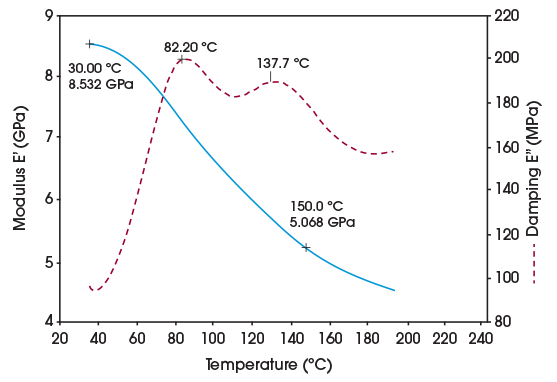
Acknowledgement
This paper is based on studies by Jon Foreman in TA Instruments’ Applications Lab.
Click here to download the printable version of this application note.