Keywords: Rubber, Butadiene, Mixing, RPA
RT004
Background
Traditional rubber testing methods, such as Mooney viscosity and Moving Die Rheometer (MDR) cure testing, have been used for several decades to monitor the mixing quality of rubber compounds. However, as elastomeric product performance becomes more demanding and highly engineered materials are required to meet these demands, testing methodologies with greater sensitivity to differences in viscoelastic properties are essential.
Physical and structural properties of raw polymer lots including molecular weight, molecular weight distribution, and the degree of long-chain branching are amongst the most influential parameters linked to changes in bulk compound and flow behavior. Differences in the polymer architecture directly impact processability and flow behavior such as flow rate, die swell, melt stability, recoverable shear, and internal stresses in blow molding, injection molding, sheet forming, cable jacket extrusion, among other production processes.1-3 Rheological characterization utilizing a rubber process analyzer (RPA) provides a quick and easy method to measure these properties, delivering a means to understand polymer structure and develop bulk structure-property relationships. These methods can provide production engineers and compounders with invaluable, predictive information regarding the processability of raw polymers and elastomeric compounds, which can be used to expedite and efficiently develop solutions to processing problems.
This note demonstrates how an RPA can be used to characterize the viscoelastic properties of two samples before and after a simulated mixing process to understand the effect of mixing on the molecular architecture.
Methods
The RPA elite (TA Instruments, New Castle, DE) is an advanced, rotorless rotational shear rheometer dedicated to the complete viscoelastic characterization of polymers, rubber, and rubber compounds at all stages of manufacturing. The RPA elite provides invaluable data related to the viscoelastic behavior of materials in the pre-cure state, through the curing process, and the final cured state. Samples are sealed in a biconical die and compressed under high pressure forces, as is standard in the rubber industry. This design provides a closed testing cavity which prevents melt fracture at the sample edge, and compressive forces to prevent sample slippage during testing. Both features are imperative for obtaining accurate data in the non-linear regime, particularly during large amplitude oscillatory strain (LAOS) testing. The viscoelastic properties of polybutadiene rubber (BR) compounds were obtained with the RPA using standard oscillation testing. Strain sweeps were performed from 0.1° to 90° degrees of arc using an appropriate frequency of oscillation of 1 Hz. These tests were performed at a temperature of 90° C. Approximately 5.5 grams of material (+\- 5%) frequency of oscillation of 1 Hz. These tests were performed at a temperature of 90° C. Approximately 5.5 grams of material (+\- 5%) was utilized and compressed in the testing cavity using a clamping pressure of 4.5 bar. Samples were allowed to relax for 10-15 minutes in the testing cavity before viscoelastic measurements were performed in order to allow ample time for any internal stresses experienced during the loading process to dissipate.

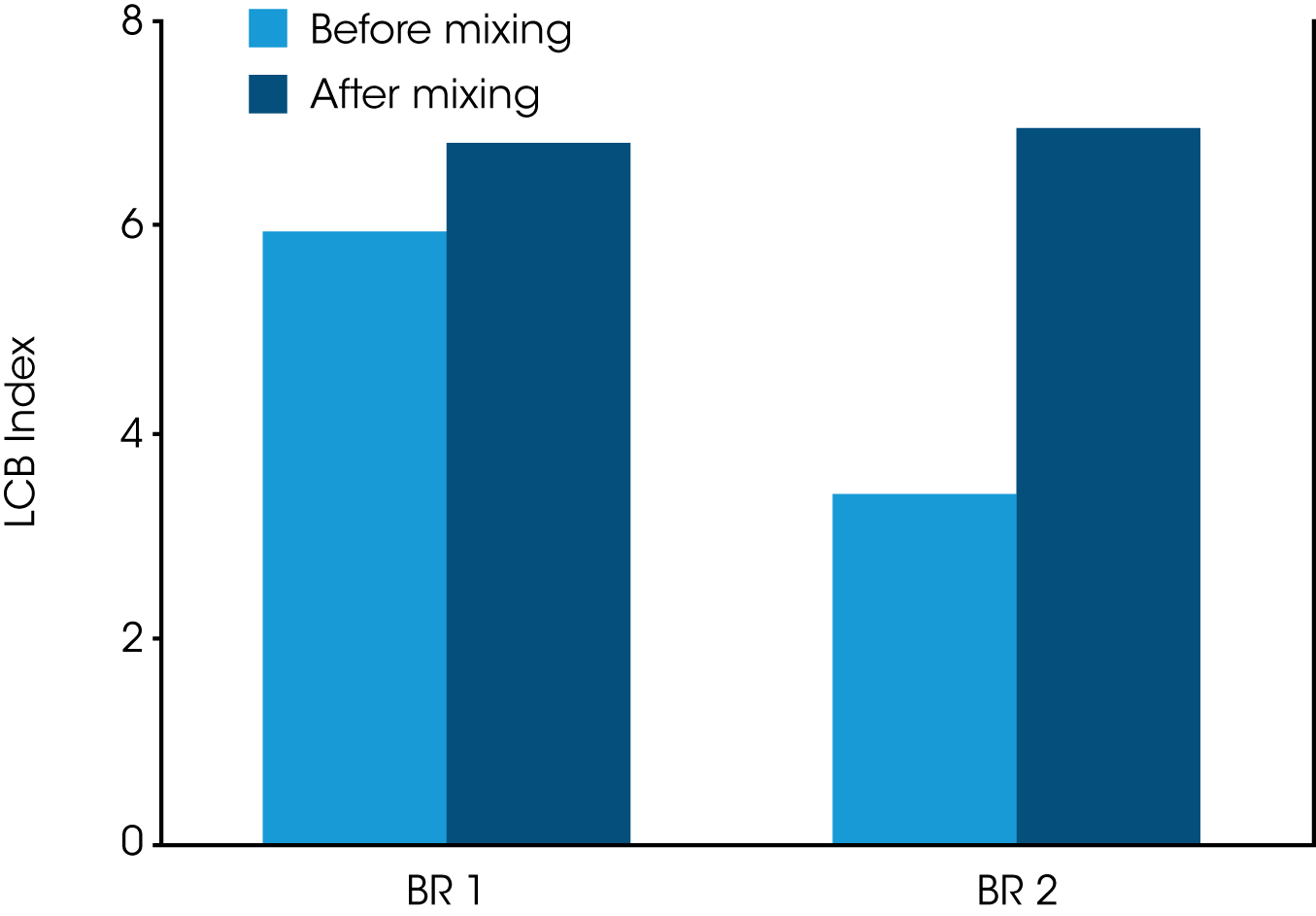

Results and Discussion
For some polymers, such as BR, styrene-butadiene rubber (SBR), and nitrile rubber (NBR), it is important to understand the degree of structure change experienced when subjected to shear and temperature, such as in a mixing process. In this case, the RPA can be used to stress the polymer under high shear and temperature, mimicking the mixing procedure, then further evaluate the change of the polymer structure by measuring the viscoelastic properties. With the proper testing method, the RPA can be used to characterize a material before the mixing process, simulate a mixing procedure, and then characterize the material after the mixing simulation, all in one test. Two samples of BR containing the same specifications of 45 MU, (cis-1,4 content > 96%) were obtained from different suppliers. The mixing process was simulated in the RPA by applying an oscillatory strain of 400% at 1 Hz over 10 minutes at 150°C. The viscoelastic properties were measured using an amplitude sweep before and after the simulated mixing process. The tangent delta and long chain branching (LCB), index at 1000% strain before and after the simulated mixing process are shown in Figure 1. Tangent delta is equivalent to the ratio of the loss modulus to the storage modulus and an excellent indicator of damping and flow properties. The LCB index is an empirical calculation related to the polymer architecture, where a positive value indicates branched architecture and a negative value indicates a linear architecture. The viscoelastic properties for BR 1 were not significantly changed during the RPA simulated mixing step, with the tangent delta remaining around 2.5 and the LCB index increasing by less than 1. However, the tangent delta for BR 2 after the RPA simulated mixing step decreased from over 4 to below 3 and the LCB index increased from less than 4 to over 7, indicating a significant change in polymer architecture due to the mixing process. The changes in BR 1 for tangent delta and the LCB index were small; less than 3% and 15%, respectively. In comparison, the tangent delta increased by 50% and LCB index by more than 100% for BR 2, shown in Figure 2. The decrease in tangent delta and increase in LCB index correspond to an increased degree of branching after the mixing step. It is known that for some butadiene rubber samples, a shear-induced reaction4 can occur on the carbon-carbon double bond on the backbone which can create long chain branches in the polymer, depending on the stabilization method used during synthesis. These results indicate that of these two butadiene rubbers, BR 2 is less stable than BR 1, and more susceptible to changes in architecture as a result of high shear in the mixing process. Quantifying and measuring the changes in polymer architecture due to the mixing process can help process engineers screen early in the manufacturing process and make adjustments as needed.
Summary
The RPA can be used to simulate the mixing process by inducing shear at a controlled temperature. Viscoelastic testing before and after the simulated mixing step can be used to measure the stability of butadiene rubbers and identify a lack of polymer stability due to an increase in long chain branching. Understanding the behavior of a material as it is processed is becoming more important since a wider variety of synthesis techniques with varying catalysts are now being used, which can lead to an array of viscoelastic properties from supplier to supplier and even batch to batch. Testing data from an RPA can be used to identify variations in polymer architecture, providing insight to the flow behavior so production parameters can be optimized in advance and waste can be reduced.
References
- Barnes, H. A. “An Introduction to Rheology”, Elsevier, 1989.
- Macosko, C. W. “Rheology: Principles, Measurements and Applications” VCH Publishers, New York, 1994.
- Tschoegl, N. W. “The Phenomenological Theory of Linear Viscoelastic Behavior”, Chapter 9, pages 443-483. Springer-Verlag, 1989.
- Kraus, G.; Rollmann, K. W., Behavior of cis-Polybutadiene During Mastication, Rubber Chem. Technol. 1965, 38, 493
Acknowledgement
Click here to download the printable version of this application note.