Keywords: Shape-memory polymer, DSC, DMA, transition temperature, cyclic test
TA399
Abstract
Shape-memory polymers (SMP) have received increasing attention because of their scientific and technological significance. These kinds of materials have the capability of changing their shape in response to an external stimulus, such as temperature or light. The ability of shape memory polymers to spontaneously recover from large deformations in restricted environments has been exploited in numerous applications, such as heat-shrink tubing, deployable aerospace structures, microsystems, and biomedical devices. It is important to develop quantitative mechanical analysis techniques to better understand the performance of these kinds of materials. In this paper, the thermo-mechanical response of a polyurethane based shape-memory polymer material was analyzed using a TA Instruments DMA. Two cyclic test procedures were developed for quantitative measurement of the thermal-mechanical properties.
Introduction
Shape-memory materials have been known for over half a century. Among them, shape-memory polymers have attracted the greatest interest due to their large strain recovery capability of up to 800% [1-5]. It is much greater than what is achievable with shape-memory alloys, which have maximum strain recovery below 8%. Besides the large strain recovery ability, shape-memory polymers hold other advantages over shape-memory alloys including being lightweight, low cost and having excellent processability. The unique properties of these kinds of polymers have been exploited in numerous applications such as heat-shrinking tubes for electronics or packaging films [6], smart fabrics [7,8], self-deployable aerospace structures [9,10], self-disassembling mobile phones [11], intelligent medical devices [12], and implants for minimally invasive surgery [13,14].
Shape-memory polymers have the capability of changing their shape upon application of an external stimulus. The shape memory property results from a combination of polymer morphology and specific processing. The shape memory effect requires two components at the molecular level: cross-links, which determine the permanent shape and so called “switching segments”, which are used to maintain the temporary shape. Most of the shape-memory polymers reported so far use heat as a stimulus [1, 15]. A change in shape caused by a change in temperature is called thermally induced shape-memory effect. The thermo-mechanical response of shape memory polymers is defined by four critical temperatures [16]. The glass transition temperature (Tg) or the melting temperature (Tm) are commonly used as the reference point for thermo-mechanical deformation and recovery. The deformation temperature (Td) is the temperature at which the polymer is deformed into a temporary shape. The initial deformation at Td can occur above or below the reference temperature, depending on the desired recovery response. The storage temperature (Ts) is less than or equal to Td and constitutes the temperature at which the temporary shape is stable over time. The recovery temperature (Tr), represents the temperature at which the material recovers its original shape during heating. Recovery can be accomplished isothermally by heating to a fixed Tr and then holding, or by continuously heating up to Tr.
Shape-memory properties can be quantified by cyclic thermo-mechanical tests. Measurements require both accurate strain control, as the sample is deformed, and accurate stress control, as the shape recovery is monitored. TA Instruments DMA is capable of performing these types of tests. In this paper, two cyclic testing procedures were developed for quantitative analysis of a polyurethane based SMP using the DMA.
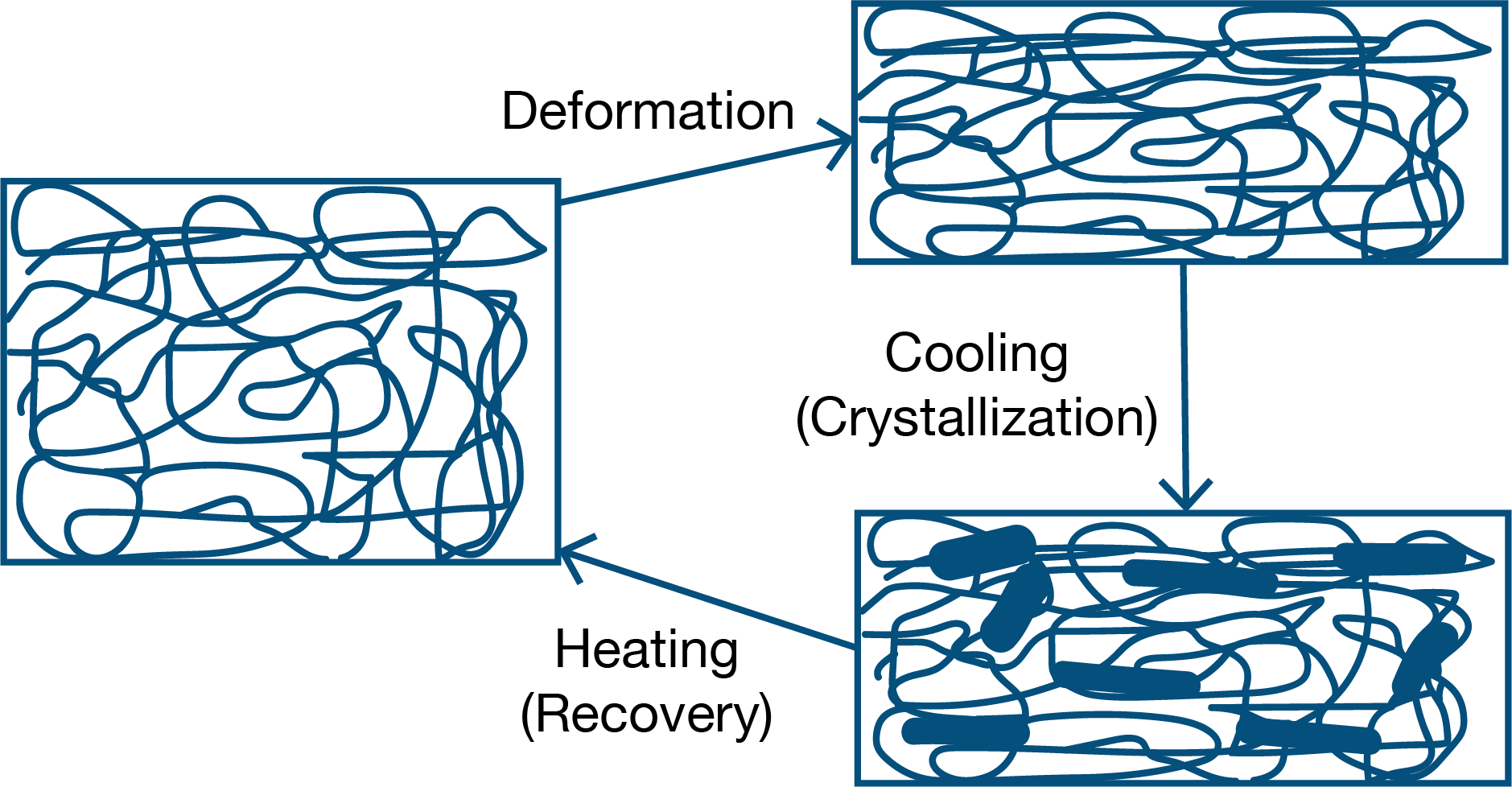
Experimental
A TA Instruments DMA with the film tension clamp was used for the thermo-mechanical property measurements. The shape memory polymer (SMP) material was a polyurethane based elastomer film, which was provided by a polymer research group in the US. The material was slightly crosslinked and contained flexible long chains. Initially, a dynamic temperature ramp test was performed from -70 °C to 80 °C with a heating rate of 3 °C/min at 1Hz. This test helps to investigate sample transition temperatures and modulus.
TA Instruments DSC with Tzero™ technology, such as the Discovery DSC 2500, can be used to study the crystalline behavior of the material. For this study, the sample was first heated to a temperature of 100 °C. A modulated test procedure was programmed from 100 °C to -80 °C then back to 100 °C with a heating and cooling rate of 1 °C/min and modulation of ± 0.11 °C every 40 seconds.
The thermo-mechanical cyclic tests were designed using Tm as the reference temperature. Two different cyclic test methods, a control strain method and a control force method, were designed using the DMA with the control software. Both methods are commonly used for analyzing the deformation-recovery properties of the SMPs. One can choose the method which is closest to the real application.
The control strain cyclic test was designed under DMA strain rate mode. As shown in figure 2, the sample is pre-heated to 70 °C, and then a large strain deformation (i.e. 100% strain) is applied. The strain is then held constant while the sample is cooled down to -10 °C. The strain is then released. The sample is then heated back up to 70 °C again, while the length recovery is monitored. This heat-cool-heat procedure is cycled multiple times.
The control force cyclic test is designed under DMA controlled force mode. Figure 3 shows the detailed procedure design. The sample is pre-heated to 70 °C. Then a force of 1.5N is applied to the sample. The force is held constant while the sample is cooled down to -10 °C. The force is released and the sample is then heated back up to 70 °C again. The recovery of sample length is monitored. This heat-cool-heat procedure is cycled multiple times.
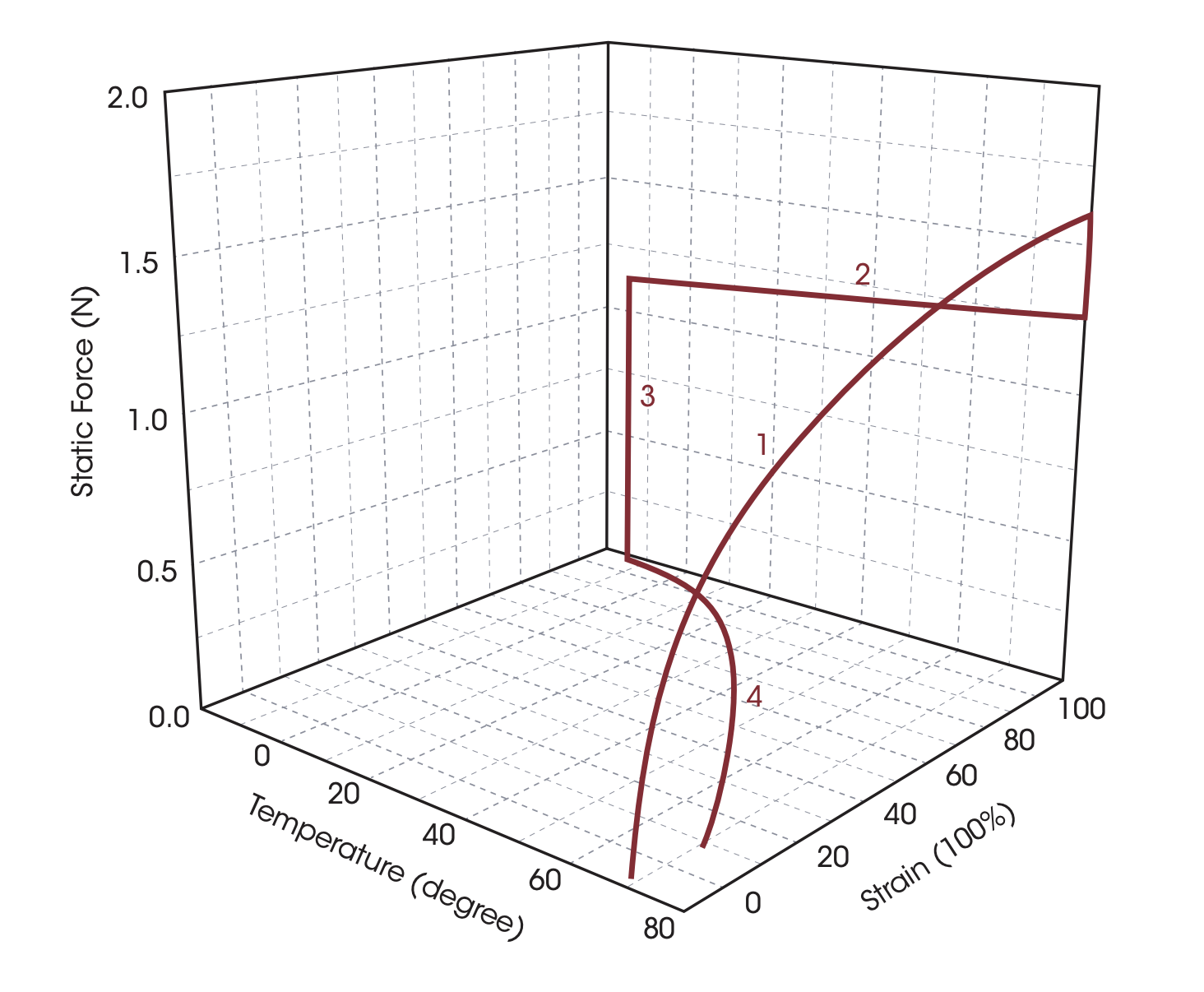
Test Mode: Strain Rate
Procedure:
- Set force 0.01N
- Equilibrate at 70 °C
- Isothermal for 10 min
- Ramp strain 50%/min to 100%
- Isothermal for 10 min
- Ramp 5 °C/min to -10 °C
- Isothermal for 10 min
- Set force 0.01N
- Isothermal for 20 min
- Ramp 5 °C/min to 70 °C
- Isothermal for 60 min
- Repeat segment 4 for 5 times
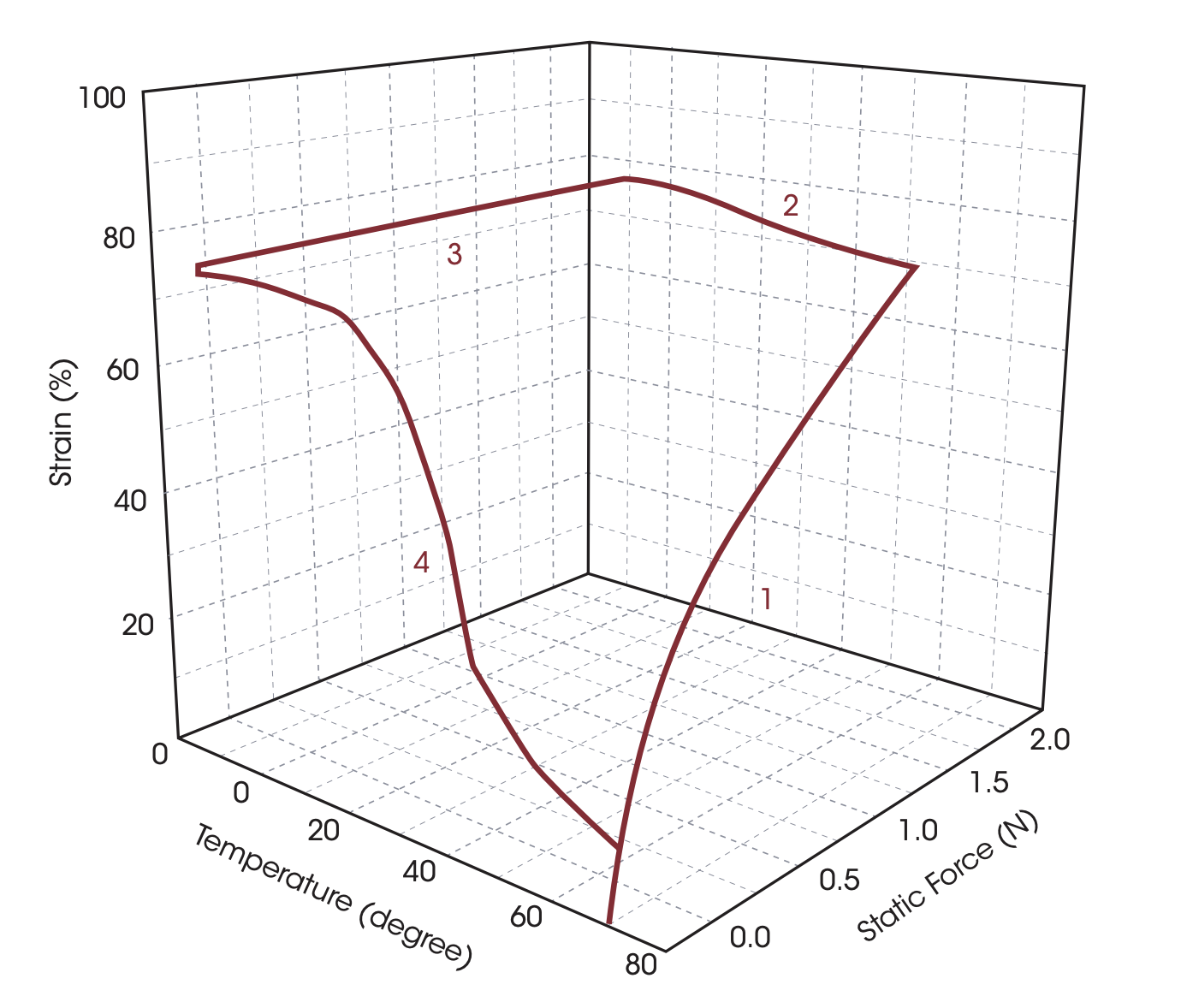
Test Mode: Controlled Force
Procedure:
- Data storage off
- Set force 0.001N
- Equilibrate at 70 °C
- Isothermal for 10 min
- Data storage on
- Ramp force 0.5 N/min to 1.5 N
- Ramp 5 °C/min to -10 °C
- Isothermal for 60 min
- Ramp force 0.5 N/min to 0.001 N
- Isothermal for 30 min
- Ramp 5 °C/min to 70 °C
- Isothermal for 60 min
- Mark end of cycle 0
- Repeat segment 6 for 4 times
Results and Discussions
The DSC test results are shown in Figure 4. The sample was initially cooled from 100°C down to -80 °C with a cooling rate of 1 °C/min. An obvious crystallization peak is observed with the peak temperature shown at -11.5 °C in the cooling curve. The formation of the crystal phase inside the SMP material makes it possible to lock the polymer chains into a certain temporary shape. Upon heating, the amorphous phase in the SMP shows a glass transition at temperature of -42° C. The crystal phase started to melt at higher temperature and the melting peak shows at 23.8 °C in the heating curve. All crystals were completely melted at temperature higher than 40 °C.
Figure 5 shows the change of the storage modulus (E’) as a function of temperature in a DMA dynamic temperature ramp experiment. The glass transition temperature measured based on the onset of the storage modulus curve showed at – 38.7 °C. Since this material is partially crystallized and slightly crosslinked, the decrease of storage modulus after the Tg was less than two decades. There is a second significant modulus drop which appeared at temperature of 48.3 °C. This decrease of the modulus associates with the melting of the crystal phase inside the polymer. Due to the existence of crosslinking network, after the melting, the material still retains certain mechanical strength. The storage modulus of this material is greater than 5 MPa at temperature greater than 80 °C. Since DSC and DMA use different mechanisms to measure and to describe Tg and Tm, the measurement results are not observed at the exact same temperatures.
Figure 6 shows the results of a six-cycle deformation-recovery test under control strain analysis mode. The sample was initially stretched to a large deformation (i.e. strain of 100%) at a temperature of 70 °C. The DMA was capable of holding this strain constant while cooling the sample to a lower temperature. At -10 °C, sample started to crystallize. The force that was required to hold a 100% strain decreased significantly. When the force was released to zero at temperature of -10 °C, a slight strain recovery of less than 2% was observed. More than 98% of the deformation was locked in shape. As the sample was heated up to 70 °C, some initial strain increase was observed, which was due to sample thermal expansion. As the temperature was increased up to above 20 °C, a significant strain recovery was observed. During the first deformation-recovery test cycle, the total recoverable strain was 62% while 38% of the deformation was permanent. The percentage of strain recovery can be quantified with the following equation:
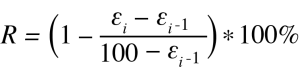
Where εi is the recoverable strain in each cycle. Based on this calculation, the percentage of strain recovery in the second and third cycle were 94% and 97%, respectively.
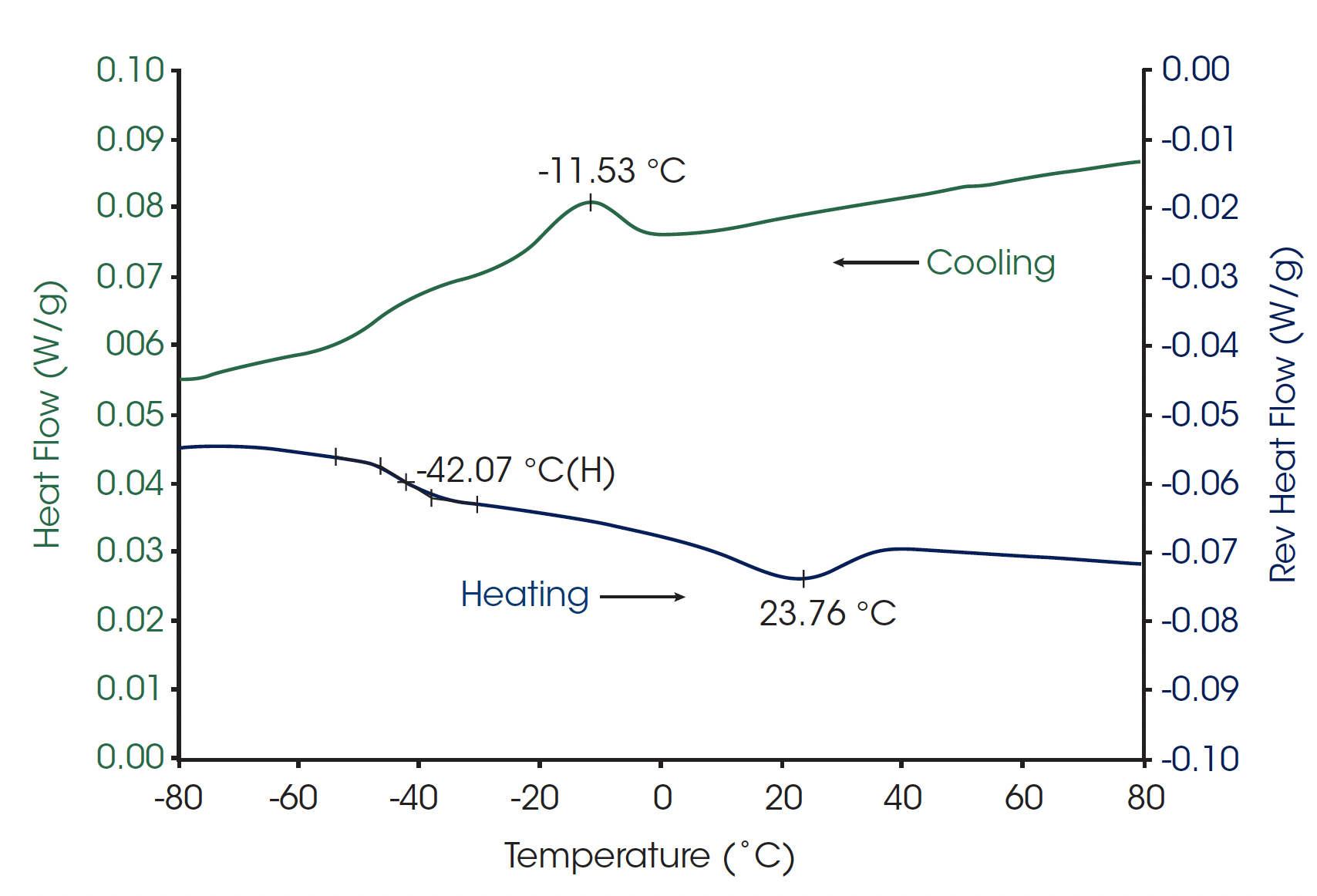
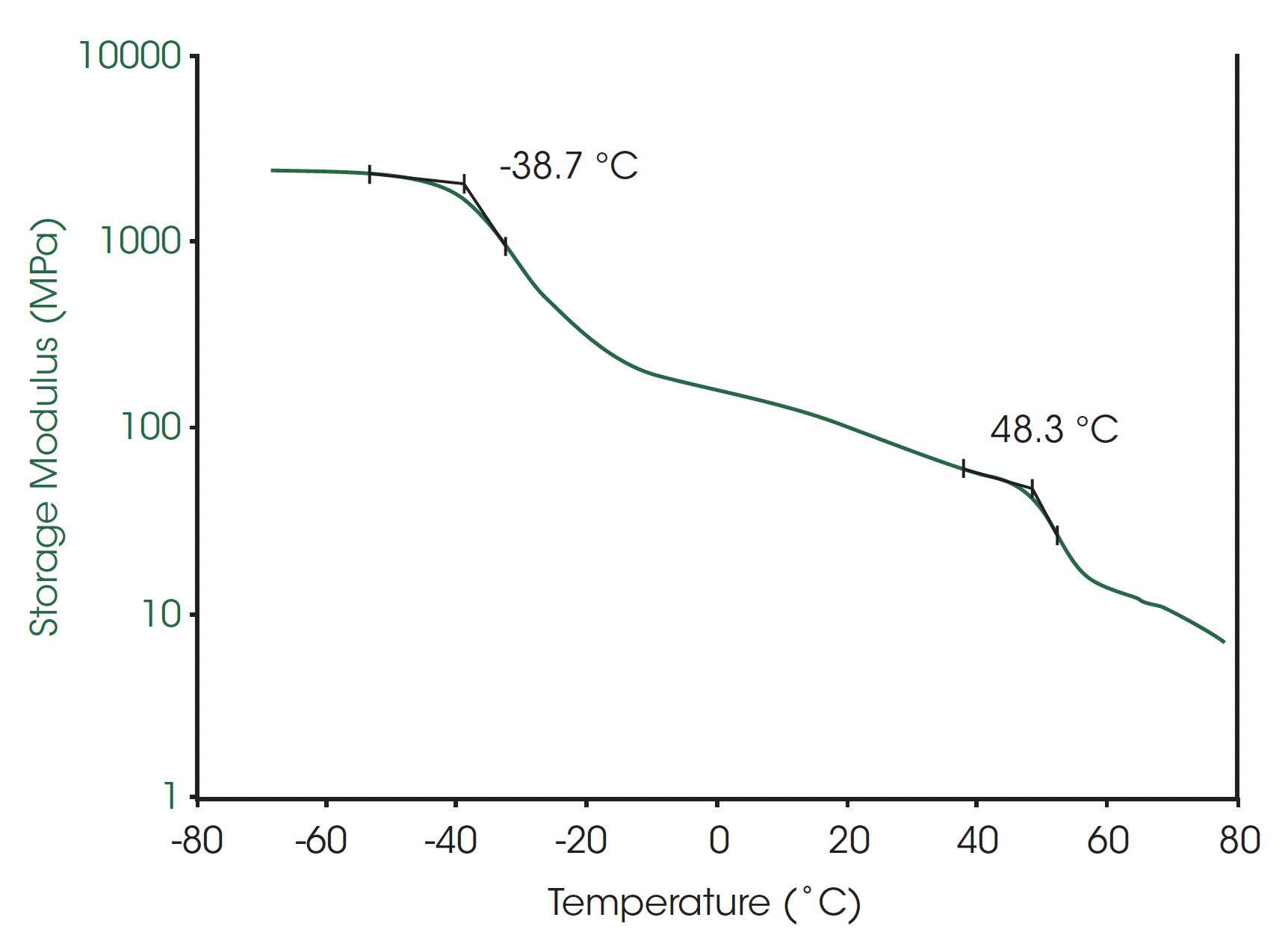
Figure 6 shows the deformation-recovery cyclic test results under control force mode. As can be seen from figure 6, since a static force of 1.5N was applied to the sample at 70 °C and the force was held constant during cooling, a certain amount creeping on the sample was obtained during the cooling process. Therefore, the final deformation should be recorded as the maximum achieved strain before unloading the force. The percentage of strain recovery can be calculated using the following equation:
Where εfi is the maximum achieved strain, εri is the recoverable strain in each cycle, and is the recoverable strain in the previous cycle. Based on the test results, the percentage of strain recovery in the first thermo-mechanical cycle was 72%, and above 95% for the rest of the cycles.
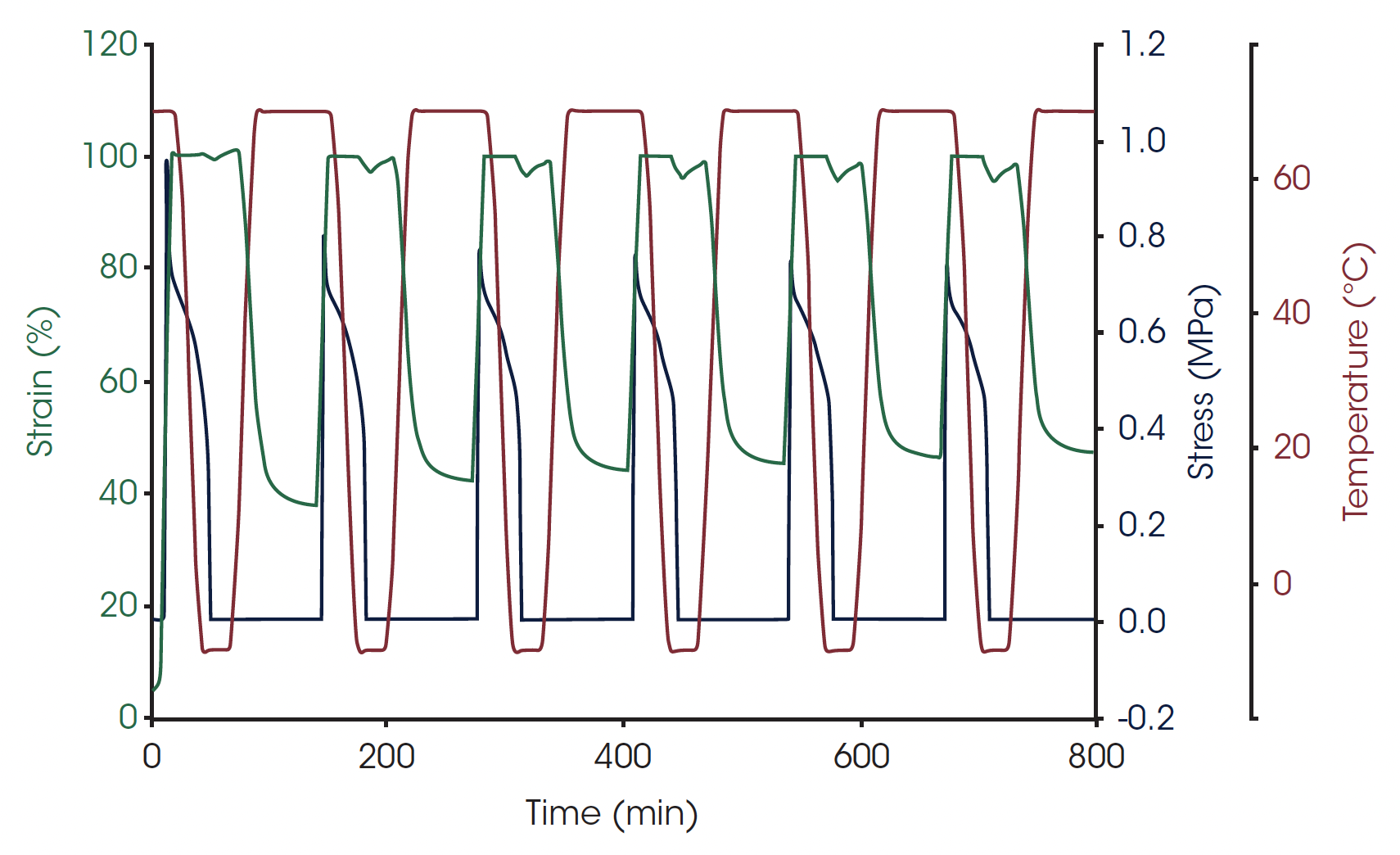
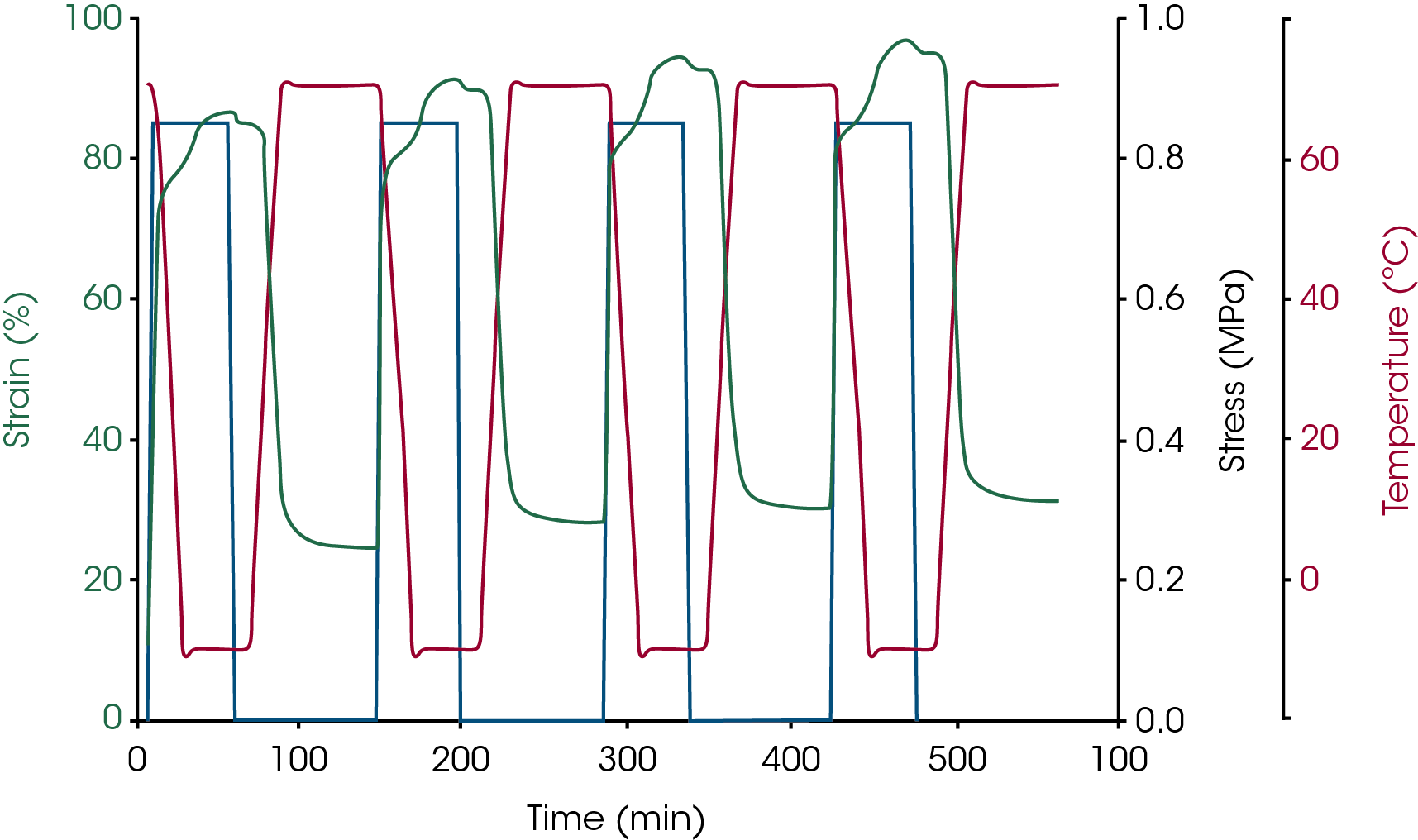
Conclusions
The unique property of shape memory polymers is that they have the capability of storing and recovering a large deformation. A common method for analyzing the mechanical properties of these kinds of materials is on a DMA through stress- strain – temperature cyclic test. The cyclic type of test can be performed either under control strain mode or under control force mode. These kinds of measurements require the DMA to have both accurate stress and strain control. TA Instruments DMA tester is a powerful dynamic mechanical analyzer, which can be used to perform cyclic tests for shape memory materials and provide accurate stress and strain control and measurements.
References
- Behl M., Lendlein A., Materials Today, (2007) 10, 4, 20-28
- Liu C., Qin H., Mather P.T. Journal of Materials Chemistry,(2007) 17, 1543-1558
- Mather P.T., Luo X., Rousseau A. Annu. Rev. Mater. Res.(2009) 39, 445-471
- Kim B.K., Lee S.Y. Polymer, (1996) 37, 26, 5781-5793
- Dietsch B, Tong T. J. Adv. Mater. (2007) 39, 3–12
- Charlesby A., Atomic Radiation and Polymers, Pergamon Press, New York, (1960), 198
- Hu J., et al., J Dong Hua University Engl. Ed. (2002), 19, 89
- Mondal S., Hu J. L., Indian J. Frbre Textile Res., (2006), 31, 66
- Campbell D., et al. Elastic Memory Composite Material: An Enabling Technology for Future Furable Space Structures. In 46th AIAA/ASME/ASCE/AHS/ASC Structures, Structural Dynamics and materials Conference, Austin, Texas, 2005
- Toensmeir, Patrick A. Radical Departure. Aviation Week & Space Technology, may 23, (2005), 72-73
- Hussein H., Harrison D. Investigation into the use of engineering polymers as actuators to produce automatic disassembly of electronic products. In Design and Manufacture for Sustainable Development 2004, Bhamra T., Hon B., eds. Wiley-VCH, Weinheim, (2004)
- Wache H.M., et al. J Mater. Sci.: Mater. Med. (2003), 14, 109
- Lendlein A., Langer R., Science (2002) 296, 1673
- Metcalfe A., et al. Biomaterials. (2003), 24, 491
- Lendlein A., Kelch S., Angew. Chem. Int. Ed. (2002), 41, 2034-2057
- Gall K., Dunn M. L., Liu Y.P., Applied Physics Letters, (2004), 85, 2, 290-292
Click here to download the printable version of this application note.