A battery separator allows lithium-ions to flow while keeping the cathode and anode physically separated from one another, thereby preventing short circuits. Separator material selection is crucial for battery performance, especially under high temperatures. Polyethylene (PE) is a common separator material that softens at high temperatures, thus shrinking its pores, disrupting the flow of Li+ ions and preventing thermal runaway.
Thermal analysis enables researchers and engineers to develop separators that resist melting, decomposition, or becoming brittle, while investigating separators’ ability to shut down thermal runaway. Thermal Mechanical Analysis (TMA) verifies that the separator shuts down safely without melting. Dynamic Mechanical Analysis (DMA) offers insight into the mechanical stability and longevity of the separator under extreme temperatures. Differential Scanning Calorimetry (DSC) measures separators’ phase transitions while Thermogravimetric Analysis (TGA) measures thermal stability and supports composition determination. Together, these techniques offer a comprehensive analysis of a separator’s qualities and behavior under use conditions.

Instruments and Test Parameters
Differential Scanning Calorimetry
Quality control
- Melting temperature (Tm)
- Heat of fusion
- Glass transition (Tg)
Phase transition
Mechanical stability
- Thermal expansion and shrinkage
Separator safety
- Meltdown temperature
Material strength
- Young’s modulus, yield strength, ultimate strength,
elongation at break - Strength vs. temperature
- Decomposition temperature
Composition determination
- Organic content
- Inorganic content (residue)
- Decomposition products
- Evolved gas analysis, TGA-MS, TGA-FTIR, TGA-GCMS
- Storage modulus
- Glass transition (Tg)
Batch-to-batch repeatability
- Glass transition (Tg)
- Storage modulus, loss modulus, tan delta
Characterization of mechanical anisotropy
- Storage modulus, loss modulus, tan delta
Application Examples
TMA thermal expansion of battery separator to identify the orientation effect
In a lithium-ion battery, the separator, a permeable microporous membrane, is an essential component that prevents physical contact between the two electrodes, thereby preventing short circuits, but still allowing lithium ion transfer, which is essential to the function of the battery. The Discovery TMA 450 can measure the dimension change and the potential failure temperature of the separator. The high sensitivity of the dimension change measurement can detect both thermal expansion and shrinkage in different separator orientations. The sample was cut into 24 mm length and 2 mm uniform width and loaded on film and fiber probe. The temperature was ramped at 3˚C/min from -70˚C to 200˚C under nitrogen purge.
Conclusion:
The TMA 450 measured the thermal expansion of the separator and identified an orientation effect in both the X and Y directions. It is important to understand the orientation effect to prevent undesired expansion or shrinkage that can lead to mechanical failure in batteries.
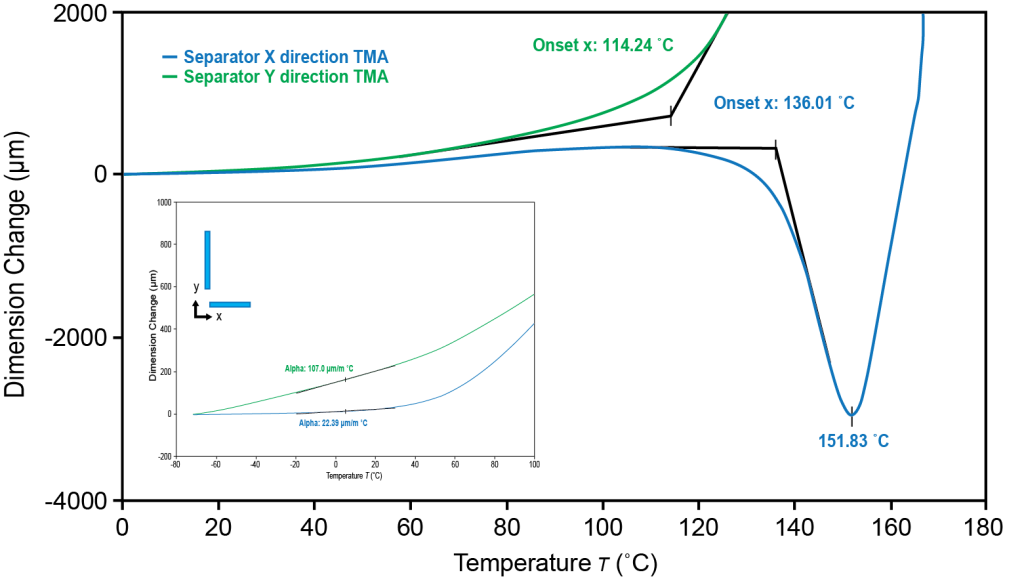
What Thermal Events Lead to Thermal Runaway?
While there are remaining questions about the thermal runaway process in batteries, current understanding suggests that it is initiated by the following series of events. The exothermic reactions leading to thermal runaway interact destructively with every inner component of a Lithium-Ion Battery (LIB) as the battery’s temperature continues to rise; some elements are early casualties while most directly speed up heat accumulation as they fail.
The first component to begin breaking down is the Solid-Electrolyte Interphase (SEI), which generally starts around 80-120°C (176-248°F). At this point, Thermal Runaway can be slowed, but is no longer reversible once the anode is exposed to the electrolyte. Exothermic reactions occurring at the reactive anode surface add more heat into the system until it reaches the next critical temperatures.
The separator is the next component affected, and it fails in two stages. Around 120-150°C (248-302°F) the separator begins to melt and causes a small short-circuit, followed by a more serious internal short circuit when the separator breaks up near 220-250°C (428-482°F).
The following reactions happen quickly and directly following the previous temperature range; the cathode material, binder, and electrolyte all begin decomposition, which drastically raises the temperature of the battery cell to temperatures about 800°C (1472°F). These reactions have gas products which increase the pressure within the LIB.
Aside from quick heat generation, the cathodic reactions have a disastrous byproduct of oxygen which is flammable. Depending on the exact conditions, the immediate result is either “Heat + Oxygen = Fire” or “Heat + Gas = Rupture/Explosion”. Of course, not all materials are made equal and may fall high or low on these ranges – or even outside of these temperatures in the future – so it is essential to make the safest possible choice of materials for a given battery with proper testing.
TGA Thermogram Highlighting Thermal Instability of Graphite Anode Material
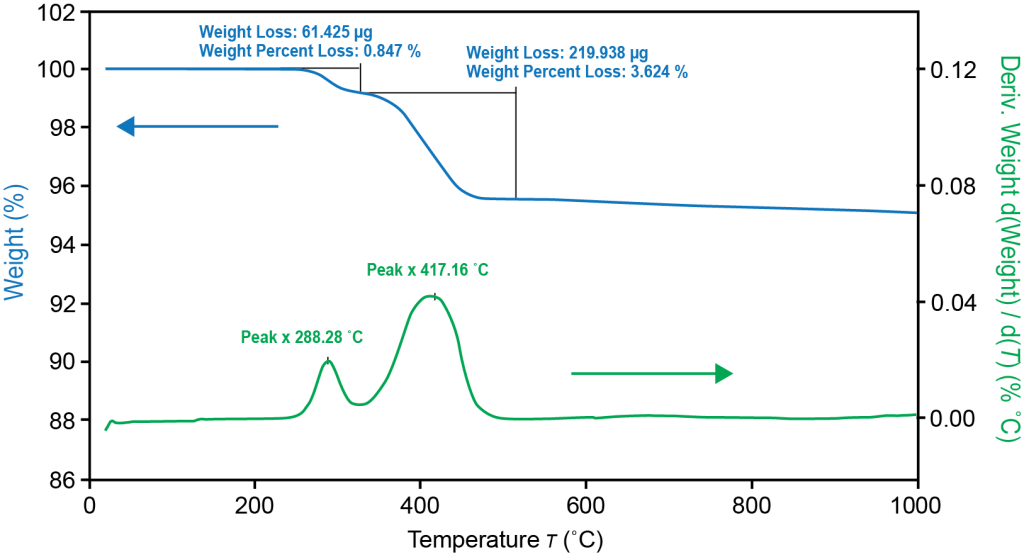
To avoid thermal runaway and select battery materials with optimal heat tolerances, battery researchers turn to Differential Scanning Calorimetry (DSC) and Thermogravimetric Analysis (TGA):
DSC: DSC measures the heat flow into or out of a material as a function of temperature or time. Phase changes interrupt the heat capacity relationship between temperature change and heat absorbed or released and are visible on graph output. It allows for testing in a variety of conditions ranging from safe operating temperature to thermal abuse.
TGA: TGA measures mass of a sample as a function of temperature or time. Generally speaking, a more thermally stable material can reach a higher temperature before any change in mass occurs.
Answer the following questions with results from your DSC:
- The material’s melting temperature, Tm
- The material’s glass transition temperature, Tg
- The lowest phase change temperature of various materials that comprise the battery.
Answer the following questions with results from your TGA:
- The temperature at which a material begins decomposition.
- The amount of sample mass lost to thermal or oxidative decomposition at a given temperature.
- The rate of decomposition reactions (both oxidative and thermally induced) at a given temperature.
- The maximum thermally stable temperature of the various materials that comprise the battery.