If atmospheric moisture and oxygen reach the inside of a battery, they can render the electrolyte useless and lead to increased flammability. Battery casings must therefore protect internal components against contamination while protecting them from adverse pressure changes or damage from impact. Casings are commonly made of aluminum or polymers, and additives like Ni-coated steels offer lithium-ion batteries excellent chemical resistance and corrosion protection.
Battery casings must be molded into their required shapes while maintaining chemical resistance and protection for the inner components. Researchers use rheology to optimize battery casings’ moldability and expedite production. Mechanical analysis offers insight to casings’ durability and lifetime, especially in applications like electric vehicles where batteries may encounter physical force in accidents. Thermal analysis, including Thermogravimetric Analysis (TGA) and Differential Scanning Calorimetry (DSC) measure casings’ thermal stability, heat capacity, melting temperature, and crystallinity. Adequate testing is crucial to ensure that battery casings can withstand demanding application conditions without jeopardizing battery safety and function.
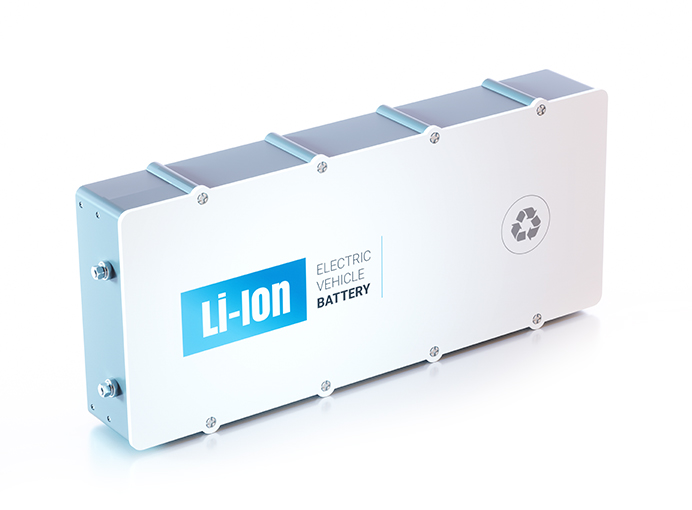
Instruments and Test Parameters
Material strength
- Young’s modulus, yield strength, ultimate strength, elongation at break
- Fatigue and durability, S-N curves
- Strength vs. temperature
Final assembly strength
- Flexural, bending or crush failure points
- Fatigue and durability, S-N curves
- Strength vs temperature
Mechanical properties of materials
- Storage modulus, loss modulus, tan delta
- Glass transition (Tg)
Batch-to-batch material repeatability
- Glass transition (Tg)
- Storage modulus, loss modulus, tan delta
Characterization of mechanical anisotropy
- Storage modulus, loss modulus, tan delta