Keywords: Thermogravimetric Analysis, High-Pressure TGA, HP-TGA, Polymer Degradation, Thermal Degradation, Fluoroelastomers, Thermal Stability
TA459
Abstract
High-performance polymers are a group of polymer materials that are often subjected to harsh environments such as high temperature, high pressure, and corrosive chemicals in their normal application. Thermogravimetric Analysis (TGA) is a proven method for accelerated lifetime testing of polymers. TA Instruments’ High-Pressure TGA (HP-TGA) enables users to investigate stability and lifetime of polymers under realistic working conditions, assessing not only the effect of temperature on material stability, but also the effects of high pressure and possibly corrosive atmospheres. The stability of a high-performance polymer is tested under realistic service conditions demonstrating the effect of pressure and atmosphere on material lifetime.
Introduction
High-performance polymers are known to retain desirable mechanical, thermal, and chemical properties when subjected to harsh environments such as high temperature, high pressure, and corrosive chemicals. High-performance polymers have the potential to replace traditional materials because of their strength-to-weight ratios and other economic advantages over aluminum or other metals. Performance polymers are used in aviation, automobile, and oil and gas industries as well as in renewable energy, electronics, and military applications. They are designed to resist a wide range of thermal, chemical, and physical stress [1-3]. Polymer degradation is an unwanted change in the properties of the polymer under the influence of one or more environmental factors, such as heat, chemicals, applied force or light radiation.
Degradation is often due to a change in the chemical and/or physical structure of the polymer, which in turn leads to a decrease in the desired properties.
Many analytical methods are used to test polymer products and their raw materials. Thermal, rheological, physical, and mechanical testing ensure that the materials comply with industry specifications and meet quality requirements. The same analytical methods are applied to assess the stability and lifetime of high-performance polymers under the same or even harsher environmental conditions as the material is exposed to in its application.
Thermogravimetric Analysis (TGA) is a proven method for accelerated lifetime testing of polymers. Short term experiments can predict in-use lifetime by assessing mainly thermal and oxidative stability of the materials. The combination of TGA with spectroscopic or chromatographic analysis of the decomposition products provides a more detailed understanding of the degradation mechanisms.
Standard TGA is usually performed at ambient pressure using inert atmospheres or air. However, high-performance polymer materials are particularly suitable for applications under harsh conditions. These materials must be tested under their service conditions to evaluate their stability and durability. These conditions include potentially corrosive, flammable, and explosive atmospheres as well as steam and high pressures.
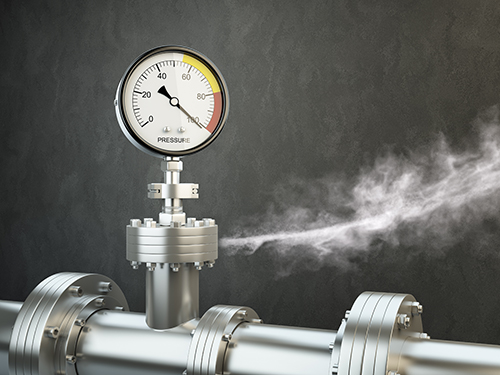
Experimental
The high-pressure TGA instrument used in this work was a Discovery HP-TGA 75. The HP-TGA 75 can be used for thermogravimetric analysis of up to 500 mg of sample material with a weighing resolution of 0.1 µg. Sample temperature can be controlled in the range from room temperature to 1100 °C and heating or cooling rates of up to 200 K/min can be applied. As a special feature of all Discovery HP-TGA series instruments, the pressure of the reaction atmosphere can be controlled from vacuum to 80 bar (1160 psi). It is possible to switch between three different reaction gases during a measurement if this is required to study reactivity caused by different gas atmospheres.
For thermal degradation testing at different pressures, an argon atmosphere was used. An argon gas-cylinder with purity grade 4.5 (>99.995%) supplied by Linde Gas was used as reaction gas. For measurement of oxidative stability, hydrocarbon free synthetic air (21% O2 in N2) was used as reaction gas [1-3].
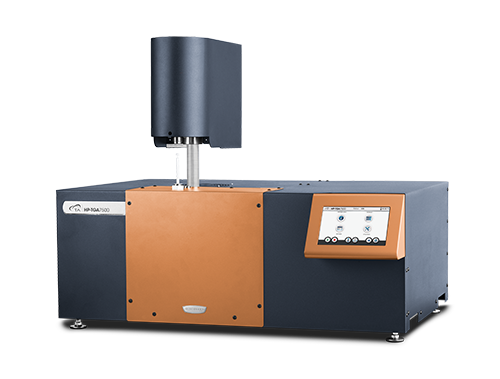
Results and Discussions
FKM is a family of fluorocarbon-based fluoroelastomer materials described in the ASTM International standard D1418 [1]. All FKMs contain vinylidene fluoride as a monomer [2]. Originally developed by DuPont, FKMs are today produced by many companies. Fluoroelastomers provide more heat and chemical resistance than neoprene or nitrile rubber elastomers. FKMs can be divided into different classes based on either their chemical composition, fluorine content, or cross-linking mechanism. Polymers of this type are considered relatively chemically inert and temperature resistant. Therefore, they are used in the chemical, automotive, aerospace, and energy industries. They are used for hoses, diaphragms, accumulator bladders, gaskets, O-rings and seals, all operating in especially harsh environments [3]. The typical service temperature of FKMs is between -20 °C and 230 °C. They can, however, withstand temperatures up to 300 °C for a short period of time. However, at high service temperatures, FKMs are weak, so the design must prevent any high loads.
Since FKMs have already been in use for decades, the material’s thermal and chemical stability has been tested extensively. However, the influence of pressure on the material’s degradation is not well studied yet. In this application note, the influence of pressure on the thermal stability and the oxidative stability of a commercial FKM was studied by high-pressure TGA.
Influence of Pressure on Thermal Stability of FKM
Approximately 20 mg of FKM sample material in an alumina (Al2O3) sample cup with 90 µl volume was placed in the Discovery HP-TGA. Argon was used as the reaction atmosphere. The thermal stability of the samples was tested by heating up to 1100 °C with a liner heating rate of 5 K/min. The same temperature profile was used in three tests at different pressures of 1 bar (= ambient pressure), 40 bar (580 psi), and 80 bar (1160 psi) to study the influence of pressure on the decomposition.
In figure 2, the TGA weight data for the three tests are plotted as function of sample temperature. At all pressures the FKM material decomposes in three steps. The decomposition temperatures of the steps depend on the pressure of the inert argon atmosphere.
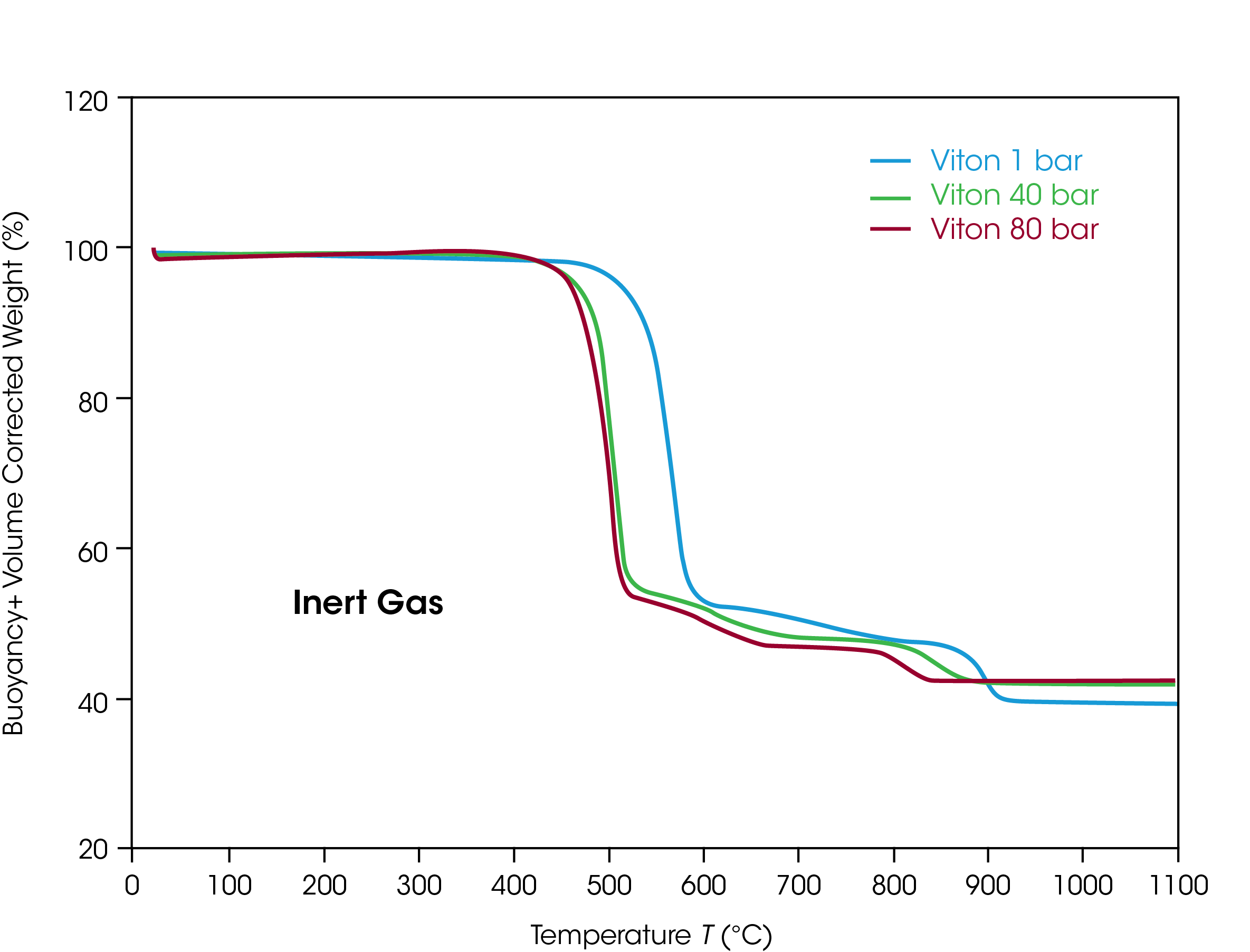
In table 1 the temperatures of the decomposition steps are summarized for each pressure. Decomposition of FKM takes place at lower temperatures when the pressure is increased from ambient to 40 bar. The differences between the temperatures range from 7 % to 11 % for the different decomposition steps. If the pressure is further increased to 80 bar, the decomposition temperatures do not change significantly compared to 40 bar.
Table 1. Onset temperatures of FKM decomposition in argon atmosphere at different pressures
Pressure | 1 Bar | 40 Bar | 80 Bar |
---|---|---|---|
Step 1 | 515 ºC | 457 ºC | 453 ºC |
Step 2 | 654 ºC | 556 ºC | 544 ºC |
Step 3 | 822 ºC | 773 ºC | 743 ºC |
A typical finding in high-pressure thermal stability testing is that the decomposition temperatures at the different steps change differently. While the temperature of the first step is 7 % lower at high pressure compared to ambient, the change in the second step is 10 % and only 4 % in the third step. Another typical finding in high-pressure TGA is that the residual weight of the material after decomposition is higher at higher pressure. This effect is considered the result of the higher resistance of volatile components from the sample to evaporate into the higher-pressure gas atmosphere.
Key insight from the high-pressure TGA testing of the thermal decomposition behavior of FKM is that the material degrades at lower temperatures if the pressure is increased. This must be considered if FKM is applied as a sealing material in applications at high pressures.
Influence of Pressure on Oxidative Stability of FKM
For testing the oxidate stability of FKM, approximately 20 mg of FKM sample material in an alumina (Al2O3) sample cup with 90 µl volume was analyzed in the Discovery HP-TGA. Synthetic air was used as the reaction atmosphere. The thermal stability of the sample was tested by heating up to 1100 °C with a liner heating rate of 5 K/min. The same temperature profile was used in three tests at different pressures of 1 bar (= ambient pressure), 40 bar (580 psi), and 80 bar (1160 psi) to study the influence of pressure on the oxidative decomposition.
In figure 3 the TGA weight data for the three tests are plotted as a function of sample temperature. The decomposition at ambient pressure in air is quite like the decomposition in argon. This proves the good stability of FKM against oxidative decomposing. The decomposition changes, however, if the pressure is elevated. At 40 bar and 80 bar the oxidative decomposition of FKM in air happens at much lower temperatures compared to argon. The oxidative stability of the FKM material is found to be lower if the pressure is higher.
The difference between the decomposition temperature for the first step in argon at low and both higher pressures is 7 %. In air the temperature difference at 40 bar is already 13 % and at 80 bar it is 17 %. Oxidation seems to be more accelerated than thermal decomposition with increasing pressure. Additionally, there is a difference between the oxidative decomposition at 40 bar and at 80 bar, as in the case of thermal decomposition in Ar.
Key insight from the high-pressure TGA testing of the oxidative decomposition behavior of FKM is that the material degrades at lower temperatures if the pressure is increased, and this trend prevails if pressure is increased further. This must be considered if FKM is applied as a sealing material in oxidative applications at high pressures.
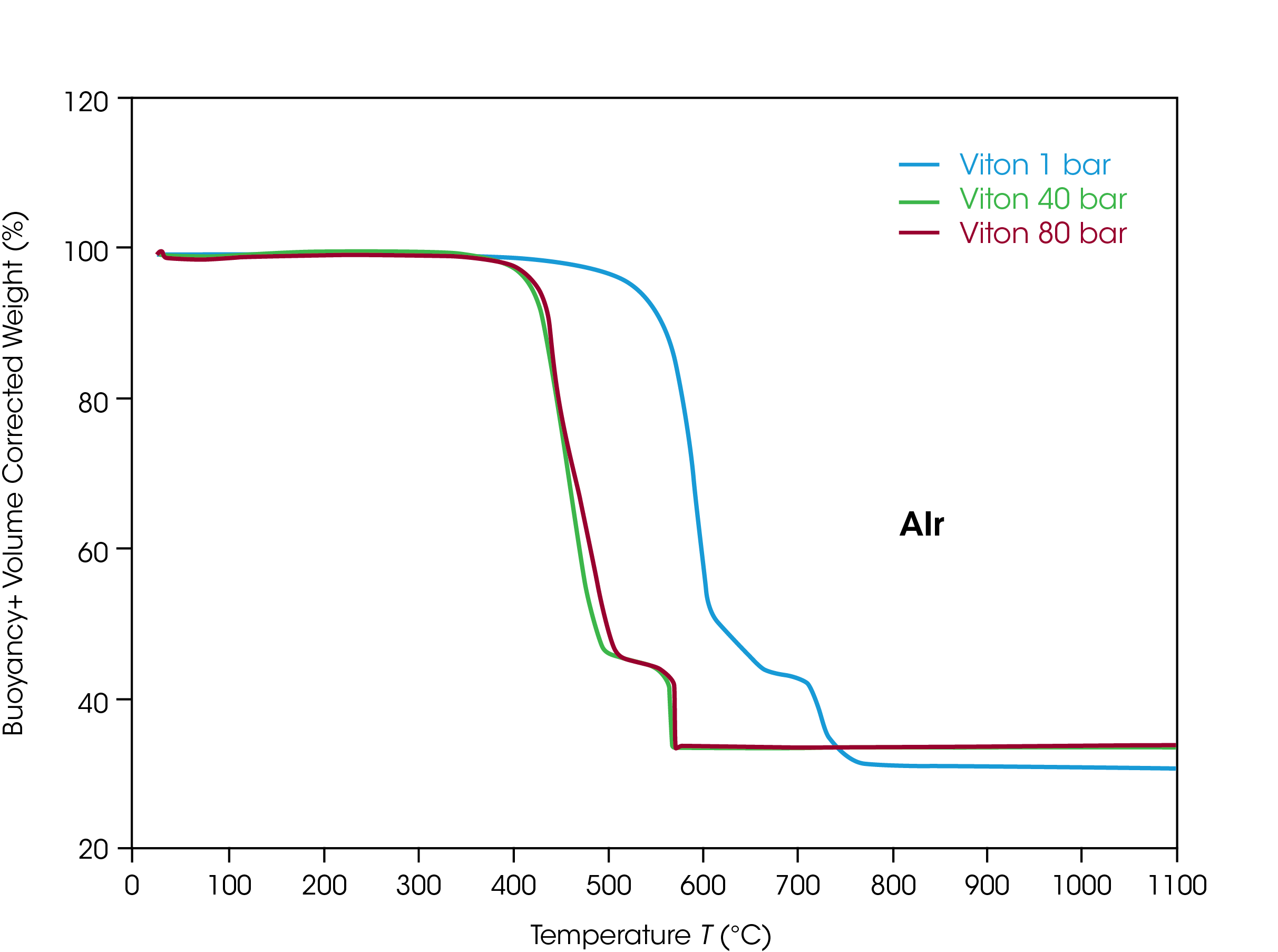
Conclusions
The thermal and oxidative stability of a commercial FKM material was found to depend strongly on the pressure of the reaction atmosphere applied. Thermal decomposition starts at elevated pressures at temperatures of up to 10 % lower than at ambient pressure. Oxidative degradation started at higher pressures at up to 17 % lower temperatures than at ambient pressure.
This finding supports that high-performance polymers used under harsh conditions should be tested for lifetime and stability against thermal and oxidative decomposition under application relevant conditions. If the material is applied at high pressures, the stability must be tested at high pressure to ensure adequate performance without unwanted decomposition. Discovery HP-TGA is an easy-to-use high-pressure TGA which allows performing such tests with a low extra effort compared to running a standard TGA experiment.
References
- ASTM D1418 – 21 Standard Practice for Rubber and Rubber Latices—Nomenclature, www.astm.org.t
- Jiri George Drobny, Fluoroelastomers Handbook (Second Edition), William Andrew Publishing, 2016.
- www.Polymerdatabase.com
Acknowledgement
This paper was written by Dr. Thomas Paschke, Product Marketing Specialist at TA Instruments.
Click here to download the printable version of this application note.