How Rheology Ensures Effective Quality Control in the Pharmaceutical Industry
Calliste Scholl | Morgan Ulrich
May 21, 2025
Whether it’s the viscosity of hydrogels (for wound care or tissue regeneration) or the yield stress of topicals (like acne or antifungal creams), pharmaceutical manufacturers rely on rheology to monitor and eradicate defects in every batch, ensuring that when the treatment reaches the patient, it remains safe and effective.
A drug’s most basic function is to target and interact with a specific biological region or system in your body. How that drug gets there, and even the speed at which it’s released, depends on the rate and manner in which it flows under varying degrees of stress; this is why rheology plays a vital role in nearly every stage of a drug’s development, especially in quality control on the manufacturing floor.
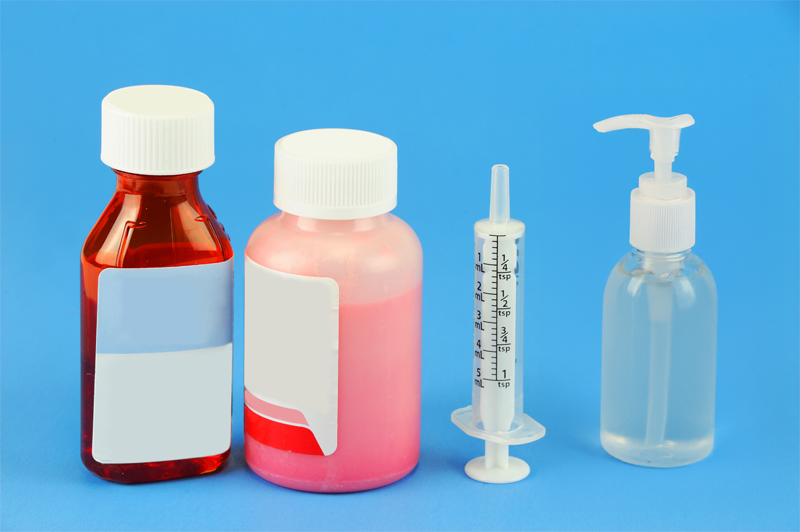
What is Rheology?
Rheology is a branch of science that studies and measures flow. Since a drug’s efficacy depends on how and where it moves into your body, manufacturers in the pharmaceutical industry must achieve consistency in the rheological properties exhibited by every formula or treatment they produce. Specifically, they need to understand and measure the interplay of two attributes:
Deformation: How a material changes when a force is applied. This data is essential to produce topical drugs (creams and lotions) that must remain shelf-stable until a rubbing or spreading motion allows skin absorption.
Flow: The measurement of a fluid’s movement from one point to another. It has an inverse relationship to viscosity. While topical drugs have a high viscosity at rest to maintain a thick, spreadable texture, vaccines require much greater flow so the substance can pass through the needle of a syringe.
Key Rheological Measurements in Pharmaceutical Quality Control
When contract manufacturers scale production, they need to minimize batch-to-batch variation. Part of that process involves measuring and monitoring these four rheological properties during the QC process:
- Viscosity: A measurement of a substances resistance to movement or its “thickness.” This can change under different levels of stress or temperature, affecting both a drug’s delivery mechanism (topically vs. orally, for example) and the environment in which it can be safely manufactured and stored.
- Yield stress: The minimum stress required for a substance to transition from solid-like to fluid-like behaviors. Understanding this threshold prevents ingredients in topical drugs from separating after they have been mixed.
- Shear thinning: A property in which viscosity decreases as shear rate and shear stress increase. This allows for smooth flow during application.
- Thixotropy: A reversible transition where apparent viscosity decreases under shear stress (due to stirring, pumping, shaking, etc.) but the product regains its structure when the stress is removed. Some nasal sprays exhibit thixotropic properties. Their viscosity decreases in order to “spray” out of the bottle, but regain viscosity as the fluid settles in the nasal cavity.
Why Rheology Matters in Pharmaceutical Quality Control
A drug typically takes over a decade to reach the market. When it does, it hasn’t just navigated a stringent and complex regulatory approval process; it has undergone rigorous testing to establish the method of application, manufacturing process, and even storage conditions. But none of that research and development guarantees a drug will be effective when it reaches the patient unless strict quality control measures are followed during its manufacture. That’s why, prior to the FDA’s approval of many drugs, the agency requires manufacturers to establish a lot release protocol – a set of quality control policies and mechanisms that assure production consistency.
Minute changes in facility equipment performance (or malfunction), the surrounding environment, and even the quality of ingredients can all change the rheological properties of a drug, which in turn may render it ineffective or even unsafe. For example, mucosal or buccal formulations require absorption inside moist cavities like the nose, mouth, gums, or the interior cheek to enter the bloodstream rapidly. If a batch of the drug is mixed improperly or overly disturbed, it can change the viscosity, ultimately preventing absorption at the point of care.
Only consistent analysis using specialized instruments like rheometers can catch defective batches before they reach the pharmacy. Across varying categories of pharmaceutical products, here’s why rheological quality control matters:
Topical and Dermatological Treatments
Most common skin conditions are treated using topical application in the form of creams, lotions, or gels. The final formulations of these products need to be shear-thinning for a few reasons:
- They need to maintain a high viscosity at rest, after the ingredients have been mixed during production, to stop sedimentation (the separation of ingredients with differing textures over time at rest).
- Despite a higher viscosity at rest, the substance needs to increase flow as a patient or doctor removes it from its packaging, either through a pump, squeezed through a tube, or even scooped with a finger.
- A smooth texture and easy spreadability upon application simply feels more pleasing, which means the patient is more willing to adhere to correct use.
Shear-thinning substances are challenging to manufacture because every batch needs to be mixed within an acceptable range of force. Too little and the ingredients will separate at rest (sedimentation), too much and the texture of the formula won’t be viscous enough upon application. Quality control measures–like an oscillation test using a rheometer–prevent overmixed or defective topicals from reaching the pharmacy shelves.
Hydrogels
Hydrogels are increasingly used in biomedical and pharmaceutical applications because of their ability to retain a significant amount of water within a network of interlinking polymers while exhibiting solid-like behavior. That structure is ideal for in vivo treatments, like tissue scaffolds or contact lenses.
Because of their rheological properties, hydrogels are especially effective as topical drug delivery systems. The substance is spreadable yet retains enough structure to directly target a specific area without dripping or fast absorption. For example, Astero, a topical pain reliever, relies on its hydrogelic properties to control the release of lidocaine over an extended period of time, rather than the immediate absorption of a lower viscosity substance.
But these very qualities make hydrogels uniquely sensitive to temperature and force; just leave Jell-O out in the sun or stir it with a spoon to see how it irrevocably transforms. That’s why an instrument like a rotational rheometer can check that a specific batch exhibits the proper attributes at rest and hasn’t yet reached a specific yield stress before leaving a production facility.
Oral Suspension
This dosage form acts like a snow globe, where the active pharmaceutical ingredient is suspended (but not fully dissolved) in liquid. And just like a snow globe, particles may settle at the bottom of the container unless the surrounding liquid is viscous enough at rest to “hold” the API in place. If not, the drug must be shaken before it’s given to the patient in order to evenly distribute the concentrated dosage.
This is one of the least invasive and easiest dosage forms to administer to patients because a liquid is easier to swallow than a pill and less painful than a needle. That’s why pediatric medicine (like infant ibuprofen) is commonly manufactured in this form.
Yet, during the manufacturing process, the viscosity of the liquid, as well as the force used to mix the formula, can alter the concentration of the API from batch to batch. Preventing these changes requires consistent analysis of the drug’s viscoelastic behavior using a rheometer.
Manufacturing Processes and Packaging Design
As a drug or treatment moves closer to commercialization, sponsors and contract manufacturers must build and refine processes that establish consistent quality at scale. Typically, this is codified and approved by the FDA via a Lot Release protocol. Rheology is integral to the process, setting acceptable thresholds – such as the shear rate for mixing emulsions to achieve full suspension without compromising the texture.
For topical treatments, the packaging itself can also play a role in application. Take Astero, the pain-relieving hydrogel for wound care, which relies on a specialized pumping bottle to release the exact dose. That’s only possible because designers studied the material’s flow rate, which dictated how much force is required to release the precise amount.
Rheology on the Factory Floor
Most pharmaceutical manufacturers aren’t experts in rheology. Their domain expertise lies in high-volume production, not necessarily in the fundamental physics of deformation and flow.
That’s why efficient, adaptable, and easy-to-use instrumentation is critical to accelerate the quality control process. A CDMO that has built a GMP-compliant facility for mass production of a life-saving drug needs high testing throughput and quick onboarding to keep each lot release on schedule.
The Discovery Core Rheometer is uniquely designed to meet the demands of pharmaceutical quality control. Its fundamental strength is in the ability to measure a range of shear rates at different temperatures, rather than the single value offered by a traditional viscometer. But critically, because of its intuitive design, it allows for high throughput. Manufacturers can test at the level of scale required to keep production lines moving. And its RheoGuide software ensures user-friendly operation for all experience levels.
Learn more about how the Discovery Core Rheometer accelerates and simplifies rheology testing in this brief product demo.
Other Resources
- Blog – Advance Formulation Performance with Rheology Studies
- Blog – Rheology Theory and Applications
- Blog – Viscometer vs Rheometer: Discover Why a Rheometer Offers More Than Just Viscosity Measurement
- Application Note – Predicting Performance of Pharmaceutical Lotions Through Rheological Characterization
- Product – Discovery Core Rheometer