Overview
The following applications collectively contribute to cost reduction in lithium-ion battery manufacturing through the following interconnected strategies:
Optimized
Slurry
Formulation
Reduction
of Defects
Elimination
of Solvent
Use
Enhanced
Conductivity
Together, these insights enable manufacturers to achieve substantial cost savings through optimized formulations, reduced defects, improved energy efficiency, and enhanced battery performance.
Resources
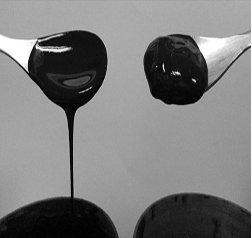
RH119: Rheological Evaluation of Battery Slurries with Different Graphite Particle Size and Shape – TA Instruments
This application note highlights several cost-saving benefits associated with using natural graphite in battery slurries, from reduced material costs, optimized slurry formulation (reducing waste & improving yield), and improved manufacturing efficiency (fewer defects leading to lower production costs).
Cost-Saving Benefits
Material Cost Reduction
Natural graphite is traditionally used to reduce costs compared to synthetic graphite. This makes it a more economical choice for large-scale battery production.
Optimized Slurry Formulation
By evaluating the rheological properties of slurries with different graphite particle sizes and shapes, manufacturers can optimize slurry formulations to enhance stability and flowability. This optimization can lead to more efficient manufacturing processes, reducing waste, and improving yield.
Improved Manufacturing Efficiency
Understanding the viscosity and viscoelasticity of battery slurries helps in fine-tuning the coating process during electrode manufacturing. This can result in fewer defects and higher quality electrodes, ultimately lowering production costs.
These insights can help manufacturers make informed decisions about material selection and process optimization, leading to significant cost savings in battery production.
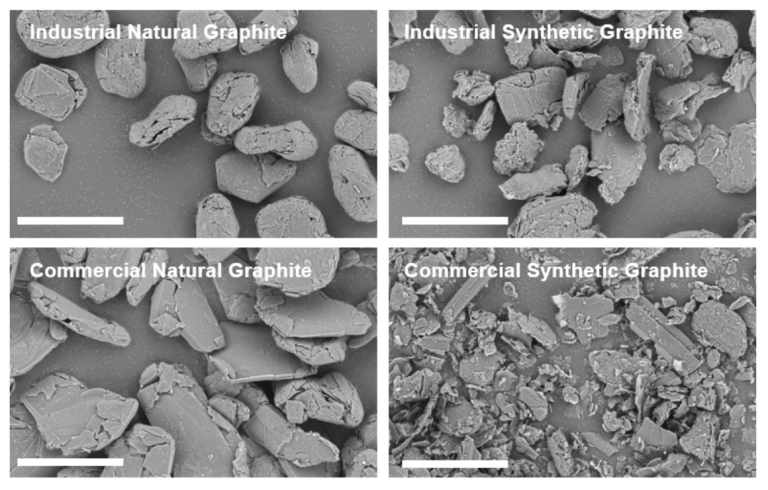
RH125: Powder Rheology of Graphite: Characterization of Natural and Synthetic Graphite for Battery Anode Slurries – TA Instruments
This application note discusses the importance of characterizing graphite powders used in lithium-ion battery anodes, leading to the following cost-saving benefits:
Graphite as a Key Material
Graphite is the most common active material for lithium-ion battery anodes due to its high energy density, power density, and long cycle life. Its abundance and low cost make it a dominant choice.
Optimization of Manufacturing Processes
Powder Properties: Understanding the powder properties of graphite helps in optimizing traditional slurry or dry processing techniques for electrode manufacturing. This optimization can lead to reduced material waste and improved efficiency.
Synthetic vs. Natural Graphite: Synthetic graphite has superior purity and thermal stability but is more expensive. Natural graphite is cheaper, and manufacturers can blend or use either source to balance cost and performance.
Reduction of Defects
Powder Shear Strength and Cohesion: High cohesion in powders can lead to aggregates forming during storage, resulting in inhomogeneous slurries and potential defects in anode coatings. Characterizing these properties helps in reducing aggregates and achieving better flow, thus minimizing defects and improving battery performance.
Efficient Material Handling
Flowability and Cohesion Testing: The Powder Rheology Accessory for TA Instruments HR Rheometers can characterize the cohesion and flowability of graphite powders. This information helps manufacturers optimize material handling and processing, reducing the energy required for mixing and improving overall efficiency.
Comprehensive Rheology Solutions
HR Rheometer: The HR rheometer provides a complete solution for battery rheology needs, from graphite powder characterization to formulated slurries. This comprehensive approach ensures consistent quality and performance, reducing the need for costly rework and quality control issues.
By leveraging these insights and tools, manufacturers can achieve significant cost savings through optimized processing, reduced defects, and efficient material handling.
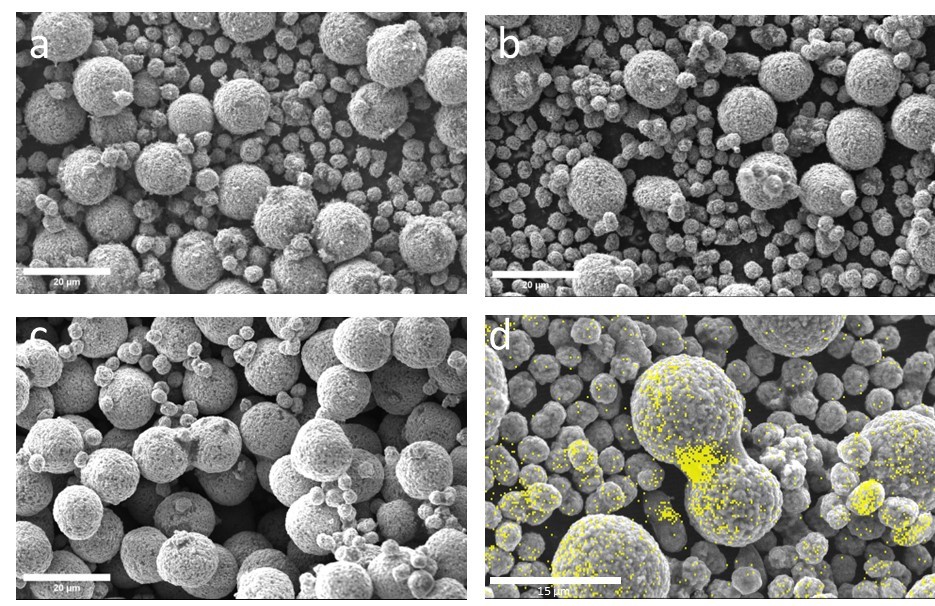
RH136: Shear and Flow Properties of an NMC Based Dry Cathode Powder – TA Instruments
This application note highlights several cost-saving benefits associated with the characterization and optimization of NMC-based dry cathode powders for lithium-ion batteries, including reduction in solvent use, energy efficiency.
Cost-Saving Benefits
Reduction in Solvent Use
Environmental and Cost Impact: Traditional slurry-based electrode processing methods require significant amounts of solvents, which are costly and environmentally harmful. Dry powder coating techniques eliminate the need for solvents, reducing both environmental impact and material costs.
Energy Efficiency
Drying Steps: The elimination of solvent use also removes the need for extensive drying steps, which account for over 40% of the overall energy consumption in electrode manufacturing. This reduction in energy usage translates directly into cost savings.
Optimization of Binder Content
Flowability and Energy Consumption: By optimizing the polymeric binder content (PVDF) in the NMC powder, manufacturers can improve flowability and reduce the energy required for mixing and processing. Higher PVDF content acts as a physical binder, enhancing the uniformity of the cathode coating and reducing defects.
Improved Manufacturing Efficiency
Powder Handling: Characterizing the shear and flow properties of NMC powders helps in optimizing powder handling and processing. This optimization leads to more efficient manufacturing processes, reducing time and labor costs.
Reduction of Defects
Consistent Quality: Understanding the rheological properties of NMC powders ensures consistent quality and performance in the final product. This consistency reduces the need for costly rework and quality control measures.
By leveraging these insights and optimizing the dry powder coating process, manufacturers can achieve significant cost savings through reduced material and energy usage, improved efficiency, and minimized defects.