Keywords: Flexural Fatigue, Composites Mechanical Strength, Thermal Stability, Woven Fiberglass Composites, ASTM D6272, Electronics
EF035
Abstract
This study investigates the influence of operating temperature on the flexural properties and fatigue life of two grades of Garolite woven fiberglass composites using an Electroforce 3330 load frame. Four-point bending monotonic and sinusoidal fatigue loading under two operating temperatures were performed on the specimens. Flexural strength, modulus, and fatigue life of the composites are measured and compared. The results demonstrate the temperature dependency of mechanical properties and fatigue life in bending loading. While the fatigue life of both grades of Garolite decreased significantly at the higher operating temperature of 100 °C, grade G11 maintained a greater fraction of its strength than G10. These experimental methods and findings can be advantageous to gaining a greater understanding of materials’ performance at different operating temperatures in various applications.
Introduction
Woven fiberglass composites are extensively used as structural support due to their higher stiffness-to-weight and strength-to-weight ratios compared to traditional materials such as metals, ceramics, and plastics.[1] Garolite is a well-known high-performance woven fiberglass composite made from woven glass cloth embedded in various thermosetting resins. It is primarily used in electronics, medical, aerospace, and marine applications due to its electrical insulating properties, dimensional stability, durability, and resistance to humidity. G10 and G11 are two grades of glass-epoxy Garolite laminates, primarily specified for their extremely high strength and thermal stability. While G-11 has a similar composition to G-10, different resin additives are used to retain its structural strength at elevated temperatures.
Temperature is one of the crucial factors that may affect the material performance of the composites. Previous studies showed that an increase in operating temperature decreases the strength of fiber-reinforced composite due to the decomposition of the resin and the weakening of the fiber bonding.[2] Therefore, the increasing application of Garolite, or composites in general, at higher temperatures requires a better understanding of their thermal stability. However, very few studies have examined the effect of temperature on the mechanical properties of Garolite under fatigue loading. Repeated or cyclic loading is inevitable in many applications, and because composites accumulate damages such as cracks and deformation, it is important to thoroughly evaluate the magnitude of lifetime reduction.[3] This study examines the mechanical properties of two commercially available Garolite composites, G10 and G11, at two different temperatures, specifically studying the effects of temperature on their fatigue behavior.
Experimental
Two commercially available woven fiberglass composites rectangular bars, G10 and G-11, with a cross-section of 25.4 mm X 3.2 mm (sourced from McMaster-Carr, IL USA) were tested to evaluate their structural stability at elevated temperatures. The material properties provided by the supplier are presented in Table 1.
Table 1. Material properties of Garolite composites.
G-10 | G-11 | |
---|---|---|
Tensile Strength (MPa) | 240-345 | 289-404 |
Flexural Strength (MPa) | 310-413 | 384-528 |
Max Temperature (° C) | 130 | 170 |
* no specifications for modulus or fatigue strength were provided |
Monotonic load-to-failure and cyclic fatigue-to-failure four-point bending tests were done on the specimens at room temperature (RT) and 100 °C. Tests were performed using a TA Instruments ElectroForce load frame, model 3330 with a force capacity of 3000 N, equipped with an oven with a temperature range of -150 °C to 350 °C (Figure 1).
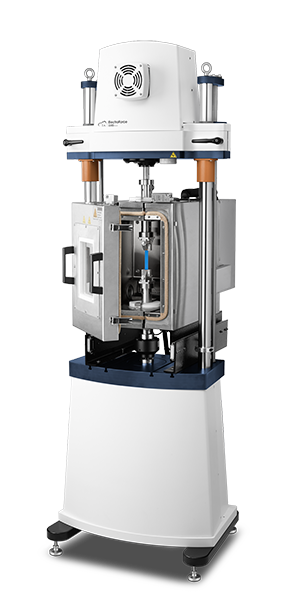
Sample geometry and testing conditions followed the requirements of ASTM D6272-17 standard.[4] The support span length was 54 mm with a load span of 18 mm (Figure 2) and samples tested were 100 mm long to provide sufficient overhanging length on each end of the supports. The testing faces of the specimens within the span length were not machined to avoid damage to near-surface fibers.
The monotonic test was performed at a displacement rate of 0.03 mm/s, and sinusoidal cyclic fatigue loading was conducted at a frequency of 10 Hz. All fatigue experiments were conducted under force control using an R-ratio of 0.1. For the high-temperature tests, the oven was heated from room temperature to 100 °C, held for 30 minutes prior to the loading, and maintained throughout the test. The monotonic test results were used to establish the maximum stress levels for the fatigue tests. The maximum stress applied during the fatigue testing ranges from 25 to 95 % of the flexural strength.
Four-point bending test with a larger region of maximum stress concentration helps reduce variation of results because of the localized imperfection in the composite materials. The maximum stress and strain between the two load spans (load span of one-third of the support span) are calculated by equations 1 and 2, respectively. [4]
S=PL / bd2 (1)
ε = 4.7Dd / L2 (2)
where S is stress in the outer fiber throughout the load span, P is the load at a given point on the load-deflection curve, L is the support span, b is the width of the beam, d is the depth of the beam, ε is the maximum strain in the outer fibers, and D is the maximum deflection of the center of the beam. Flexural strength is defined as the maximum stress prior to the material failure, and modulus of elasticity is the ratio of stress to strain within the elastic region.
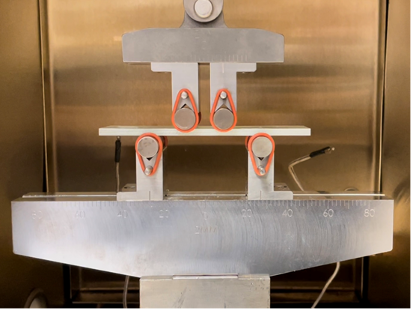
Results and Discussions
Results of the monotonic four-point bending tests are shown in Figure 3. Representative stress-strain responses of the G10 and G11 composites at two temperatures of RT and 100 °C are presented in Figure 3a. For each condition, three repetitive tests were performed. All repeated tests exhibited replicable stress-strain curves and the results showed consistent failure behavior between the samples. The stress builds linearly until it reaches the maximum strength and drops after failure.
At room temperature, G11 composites exhibit a higher flexural strength of 487.1 ± 9.9 MPa compared to G10 with failure stress of 409.0 ± 2.4 MPa (Figure 3b). Although both composites are tested within their operating temperature, there is a significant drop in flexural strength at a higher temperature of 100 °C. However, G11 performs significantly better with retaining ~80% of its structural strength, while G10 retains only 68% of its strength. It is noteworthy that the flexural modulus of both composites decreases at the higher operating temperature, despite being below the supplier specified maximum operating temperature. While the experimental results at room temperature are in agreement with the material properties reported by the supplier in Table 1, there is a degradation of the structural strength of both composites at 100 °C, well below the reported maximum operating temperature.
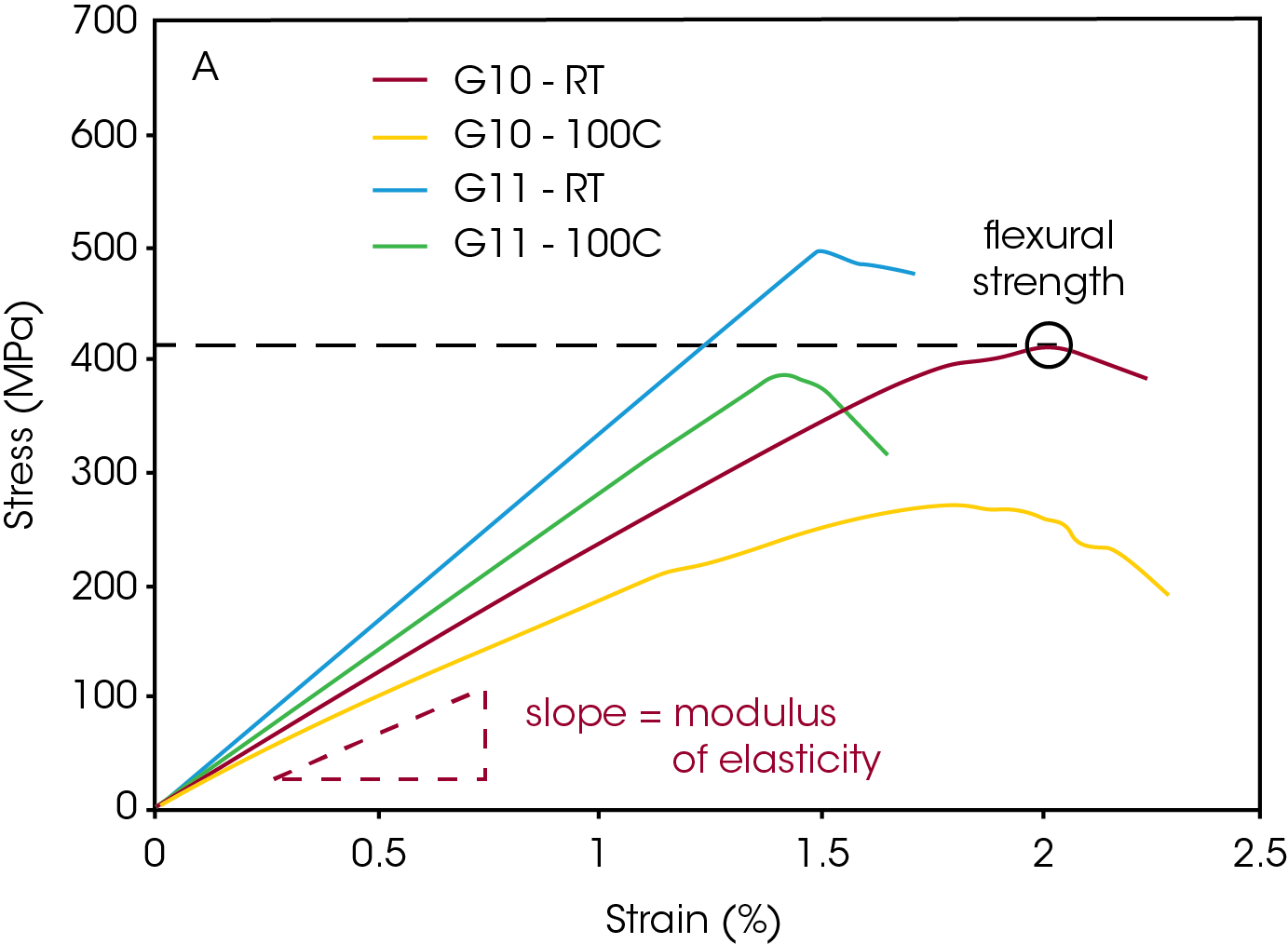
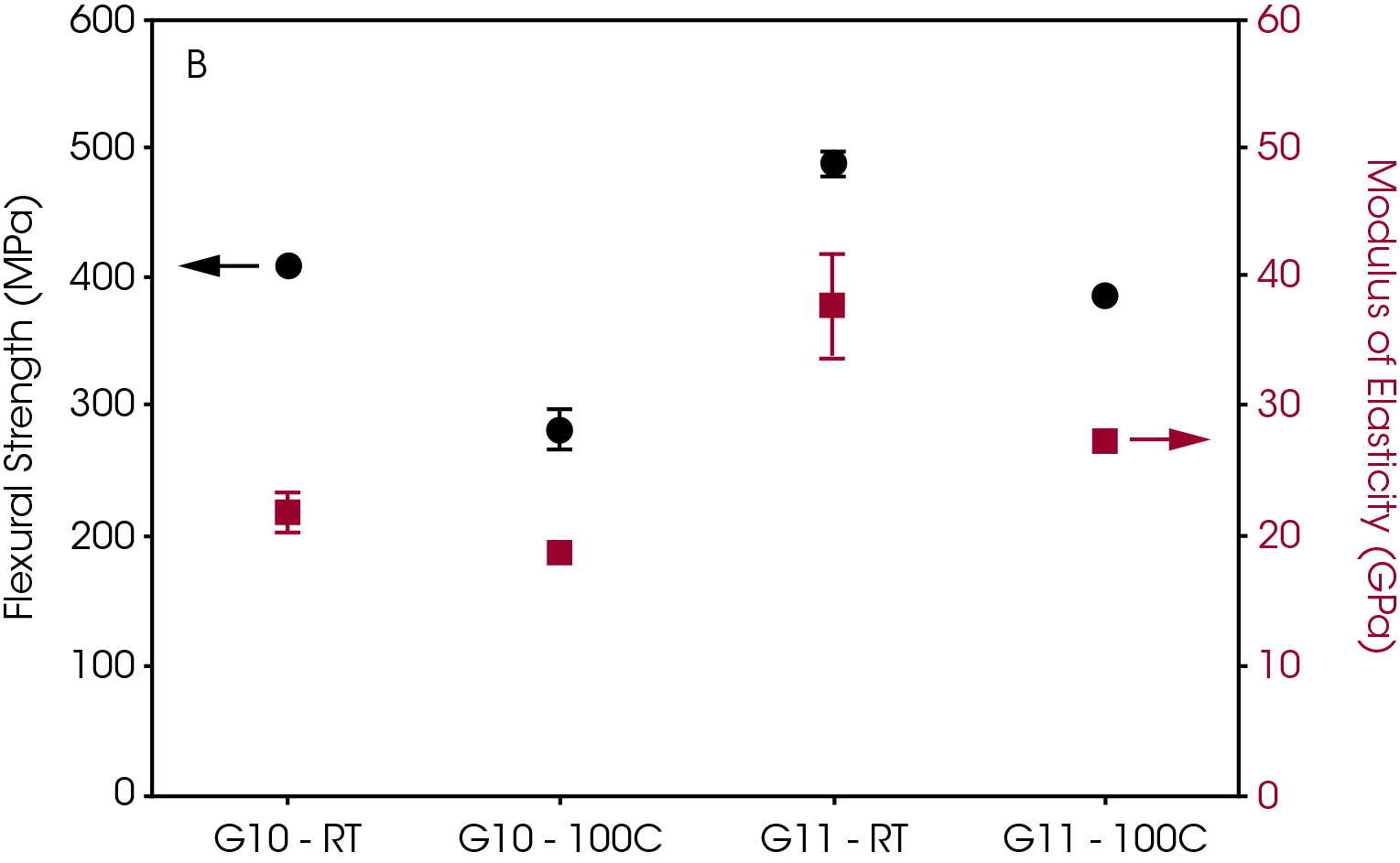
Four-point bending fatigue tests were conducted with continuous loading to accumulate damage in the composite material system and evaluate the life cycles until failure at various stress levels. The initial fatigue experiments have been performed at 95% of the average flexural strength (proportional limit) stress attained from the monotonic tests. Sufficiently high fatigue stress levels, which ranged from 25% to 95% of the proportional limit stress, were used to ensure that failure occurred during cyclic loading. Considering the loading ratio of 0.1, the upper surface in contact with the loading span was submitted to compressive stresses, while the other surface in contact with the support span was submitted to tensile stresses. The fatigue life of each sample is characterized as the number of cycles to final failure.
Figure 4 shows the fatigue life (cycles to failure) as a function of the maximum fatigue stress (S-N curve) for each composite at two temperatures. The S-N curves demonstrate a comparison between the fatigue performance of each composite at different temperatures. Results show that the cycles to failure decrease as the stress increases in all cases; however, at room temperature, the G11 performs significantly better in fatigue life compared to G10. Furthermore, G11 retains a higher number of the fatigue life cycle at continuous operating temperatures of 100 °C. For example, for fatigue stress of 200 MPa at a temperature of 100 °C compared to room temperature, there is a 91% reduction of fatigue life in G10, while there is only a 46% reduction for G11. All samples failed at less than 2M cycles even at stress levels as low as 25% for Flexural Strength, therefore longer-duration experiments with lower stress levels are required to adequately evaluate material strength for applications where real-life cyclic loading could extend beyond 2M cycle.
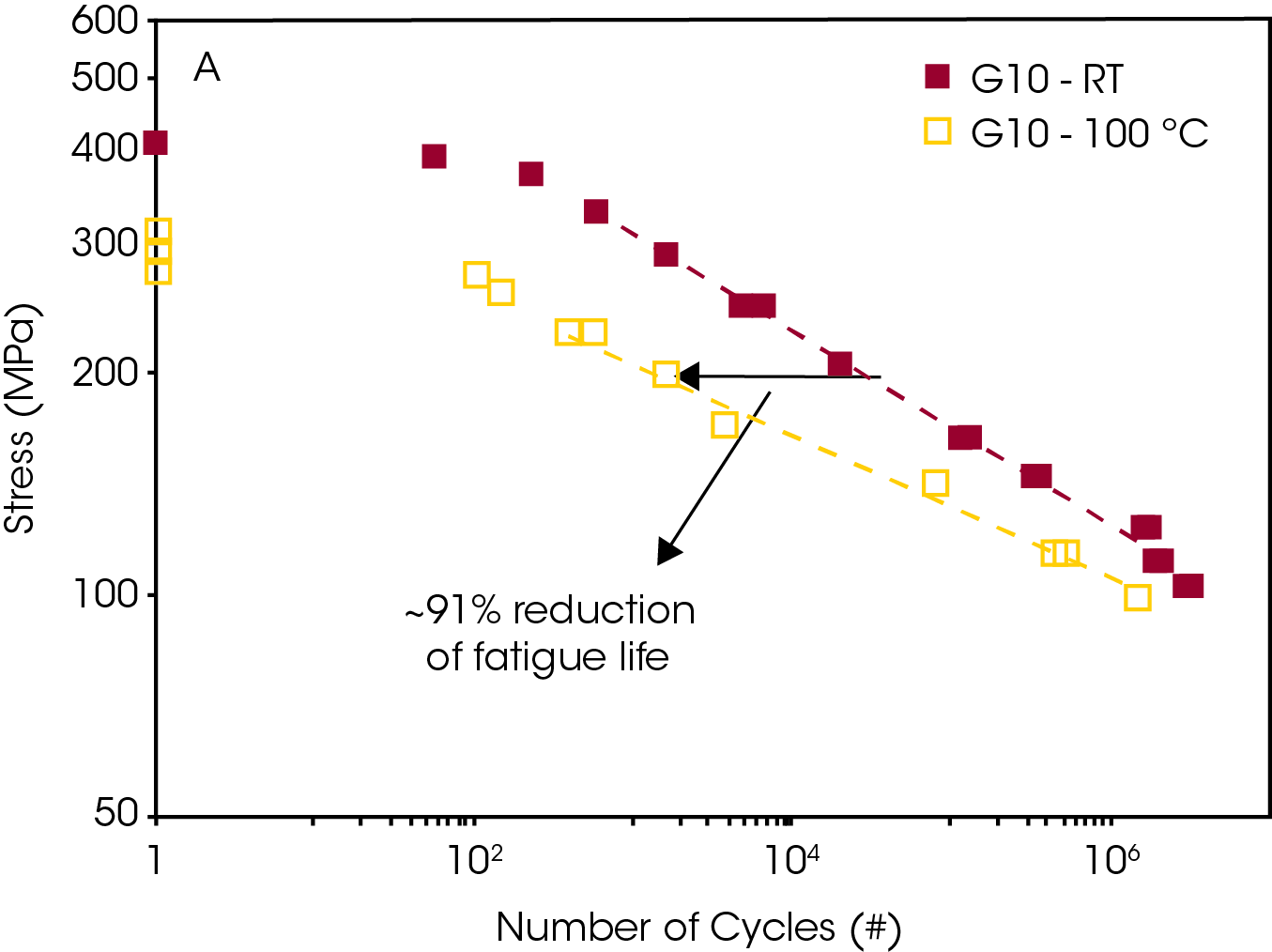
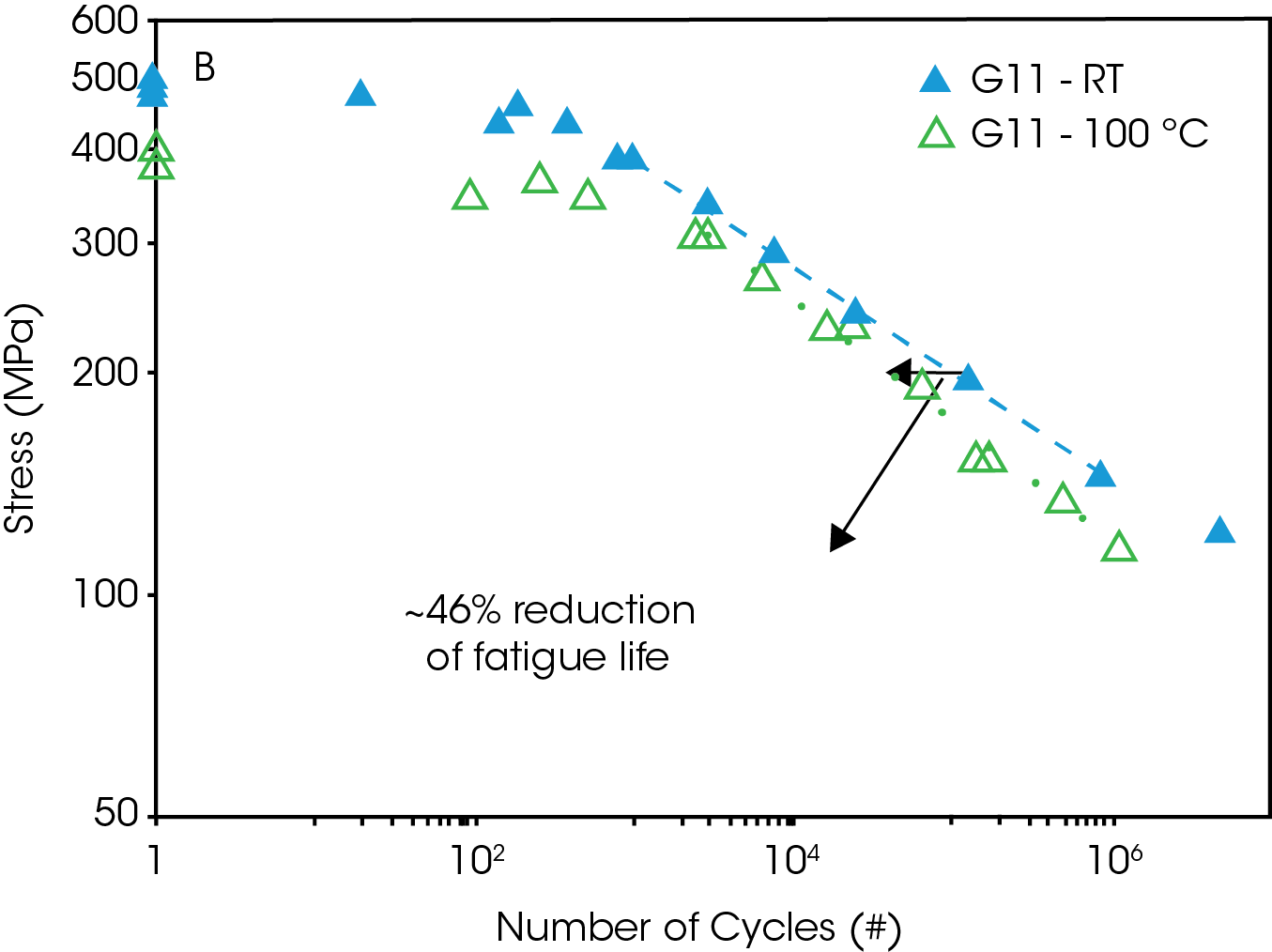
Conclusions
The monotonic load-to-failure and cyclic fatigue-to-failure tests in four-point bending were performed on two grade Garolite composites (G10 and G11) at two different temperatures RT and 100 °C. G11 demonstrates higher flexural strength compared to G10 at room temperature and maintains a higher strength at 100 °C. Fatigue failures occur before 2 million cycles at stress levels even as low as 25% of the monotonic flexural strength and an endurance limit was not observed. Therefore, longer tests are required to understand fatigue limits for applications greater than 2M cycles. The fatigue life of composites decreases at elevated temperatures. G11 performed significantly better in retaining its structural strength at a higher operating temperature of 100 °C. The results of the four-point bending tests show that the temperature has a significant effect on the flexural strength and fatigue life of the Garolite composites. The results demonstrate that the supplier specifications shown in Table 1 may not be applicable for the entire temperature range stated. Therefore, it is important to test the materials at different operating temperatures to gain a better understanding of the materials’ performance.
Future Outlook
A more comprehensive investigation of the effect of temperature on modulus and viscoelastic properties using DMA (Dynamic Mechanical Analysis) methods will be published in a separate application note. DMA provides greater insights on glass transition temperature and material properties near and beyond the maximum rating temperatures.
References
- Paradiso A, Mendoza I, Bellafato A, Lamberson L. Failure behavior of woven fiberglass composites under combined compressive and environmental loading. Journal of Composite Materials. 2020;54(4):519-533. doi:10.1177/0021998319878771
- Zhou F, Zhang J, Song S, Yang D, Wang C. Effect of Temperature on Material Properties of Carbon Fiber Reinforced Polymer (CFRP) Tendons: Experiments and Model Assessment. Materials (Basel). 2019;12(7):1025. Published 2019 Mar 28. doi:10.3390/ma12071025
- Rasheduzzaman, Mohammad, and M. N. Cavalli. “Failure Mode Transition in Fiber Composite Fatigue.” Fracture, Fatigue, Failure, and Damage Evolution, Volume 5. Springer, Cham, 2015. 165-172.
- ASTM D6272-17 (2017) Standard Test Method for Flexural Properties of Unreinforced and Reinforced Plastics and Electrical Insulating Materials by Four-Point Bending. ASTM International, West Conshohocken.
Acknowledgement
This paper was written by Dr. Soheil Daryadel, Applications Support Scientist at TA Instruments.
Click here to download the printable version of this application note.