Keywords: chemical recycling, LDPE, catalytic pyrolysis, H-MOR
TA482
Abstract
Pyrolysis is a chemical recycling technique that creates feedstock from plastic waste through thermal energy. The energy used in the process can be reduced using a catalyst that lowers the temperature for degradation. Development and screening of catalysts can be done using thermogravimetric analysis (TGA), offering an efficient way to optimize catalytic pyrolysis by forgoing large scale reactors. In addition to understanding the impact of catalyst on degradation temperature, the residual material can be used to understand the amount of recoverable material in the recycling process. Various amounts of catalyst were added to commercially available polyethylene to demonstrate TGA as a screening tool in catalytic pyrolysis. The onset temperature of the polymer’s degradation decreased with increasing catalyst and the residue was equal to the amount of catalyst used.
Introduction
Plastic waste accumulation in the environment necessitates innovative ways to process and recycle non-biodegradable polymers. Mechanical processes currently dominate recycling infrastructure but chemical processes, which hold the promise of more complete circularity, are gaining traction [1]. Pyrolysis is a chemical process that uses thermal energy to convert solid plastic waste into smaller molecules for feedstock. Compared to other chemical processes such as incineration or gasification, pyrolysis has the potential to produce fewer emissions and is viewed as a more sustainable, efficient chemical recycling process [2].
Catalytic pyrolysis can be used to reduce the processing energy by lowering the temperature for degradation of the polymer to occur [3]. Various parameters influence the performance of catalytic pyrolysis, such as catalyst properties, polymer impurities, and the polymer identity itself [4]. As a result, development and screening of catalysts is necessary to optimize the recycling process for the material of interest. Often, large scale reactors are used, but TGA is an efficient and accurate alternative. TGA simulates pyrolysis conditions and allows investigation of the catalyst activity to reduce the amount of energy required in the process. This work demonstrates TGA as a catalytic pyrolysis screening tool using a mordenite catalyst with low density polyethylene (LDPE).
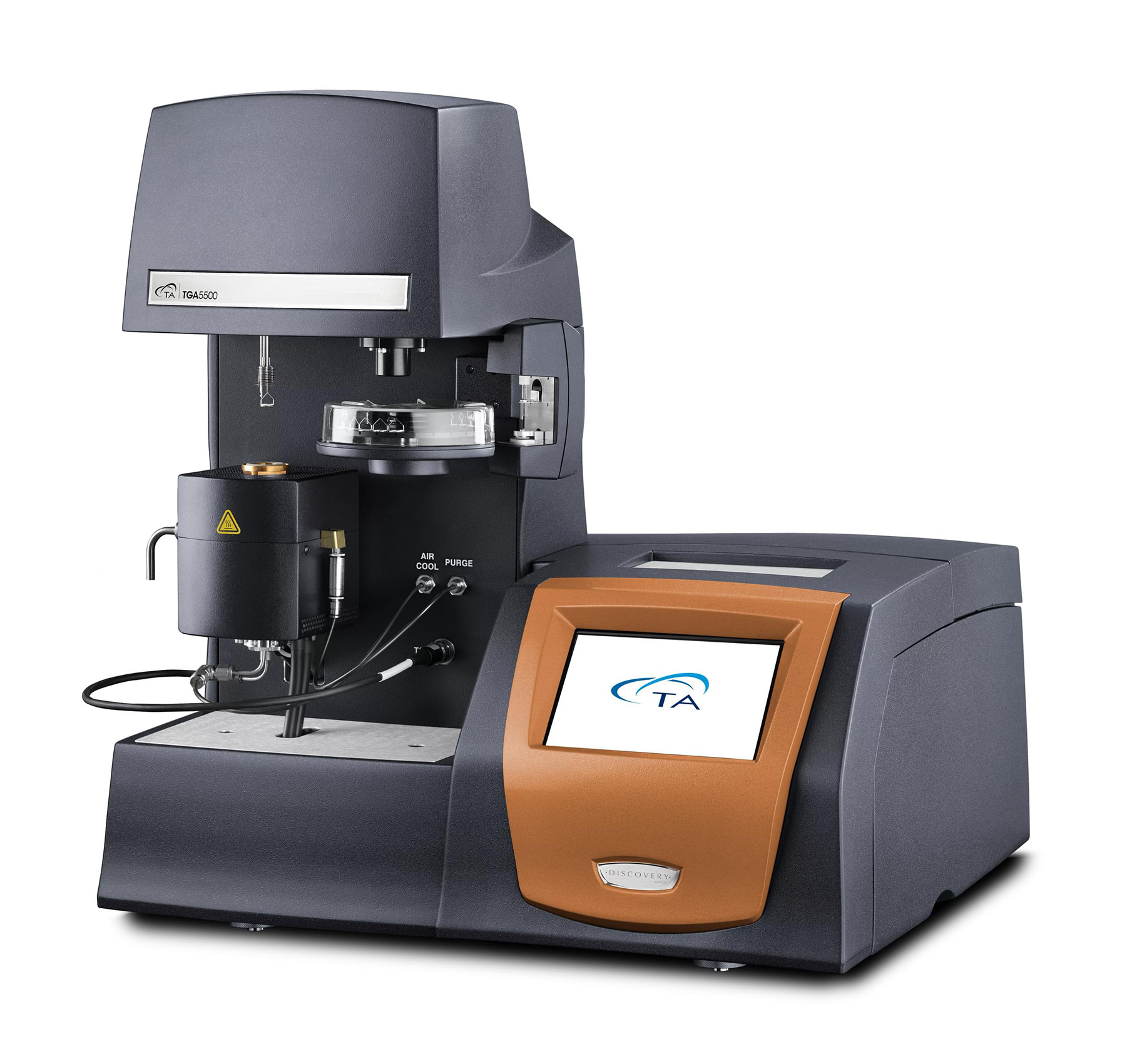
Experimental
Commercially available LDPE was thermally degraded using a hydrogen mordenite (H-MOR) catalyst. LDPE powders were mixed with varying amounts of H-MOR powder to yield samples with 0, 5, 10, and 20 wt% H-MOR.
Degradation and pyrolysis were measured using a Discovery™ 5500 TGA, shown in Figure 1. Samples of 1.5 (± 0.2) mg were loaded into 100 μL platinum pans and ramped at 20 °C/min up to 800 °C in inert gas (nitrogen).
Results and Discussion
Figure 2 shows the weight loss of the four LDPE/H-MOR samples as a function of temperature. Adding the catalyst lowers the samples’ degradation temperature and the residue for each run matches the loading level of the catalyst. In the mass balance of pyrolysis products, scientists typically target valuable liquid products that can be used as feedstock to make new polymers and other products. Less valuable solid residue is also quantified at the end of a TGA experiment.
The onset point of the weight loss from thermal degradation was determined by the intersection of two tangent lines on either side of an inflection point, identified as the maximum slope in the region. The onset of degradation for each sample is plotted in Figure 3 and listed in Table 1. The neat LDPE sample degrades at 416.3 °C and decreases nearly linearly up to 10% loading of the catalyst but appears to plateau at 20 wt% loading. This information can be used to optimize catalyst loading and degradation temperature for samples undergoing pyrolysis process refinement.
In addition to onset temperature, the thermogram obtained in a TGA experiment provides additional detail of the time and temperature resolved degradation profile of a catalytic pyrolysis reaction. Catalysts can change the degradation mechanism of polymers, which may be reflected in the TGA data. Although not studied in this report, TGA can also be combined with evolved gas analysis (EGA), which would add information to this experiment regarding the chemical identity of degradation products.
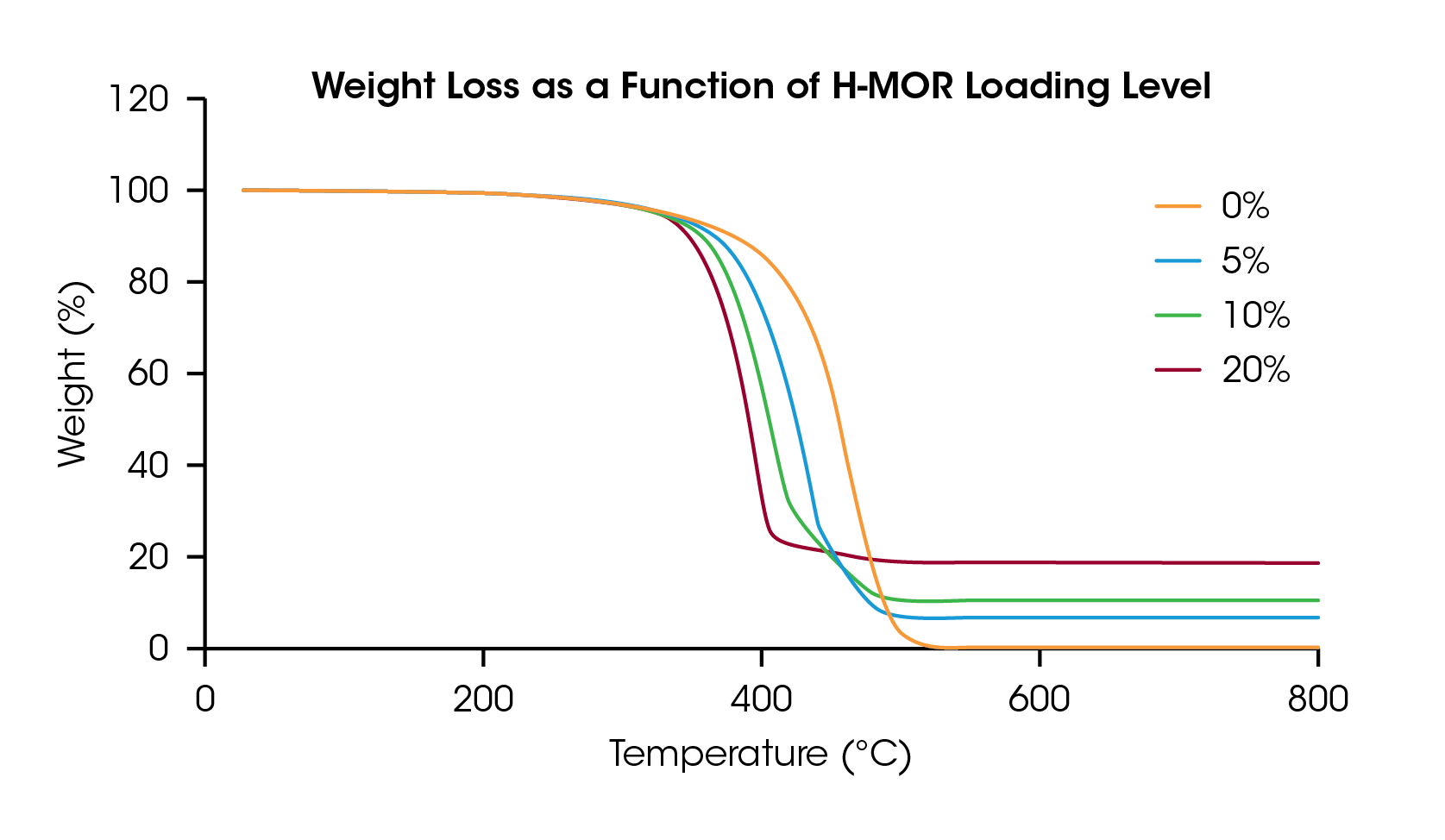
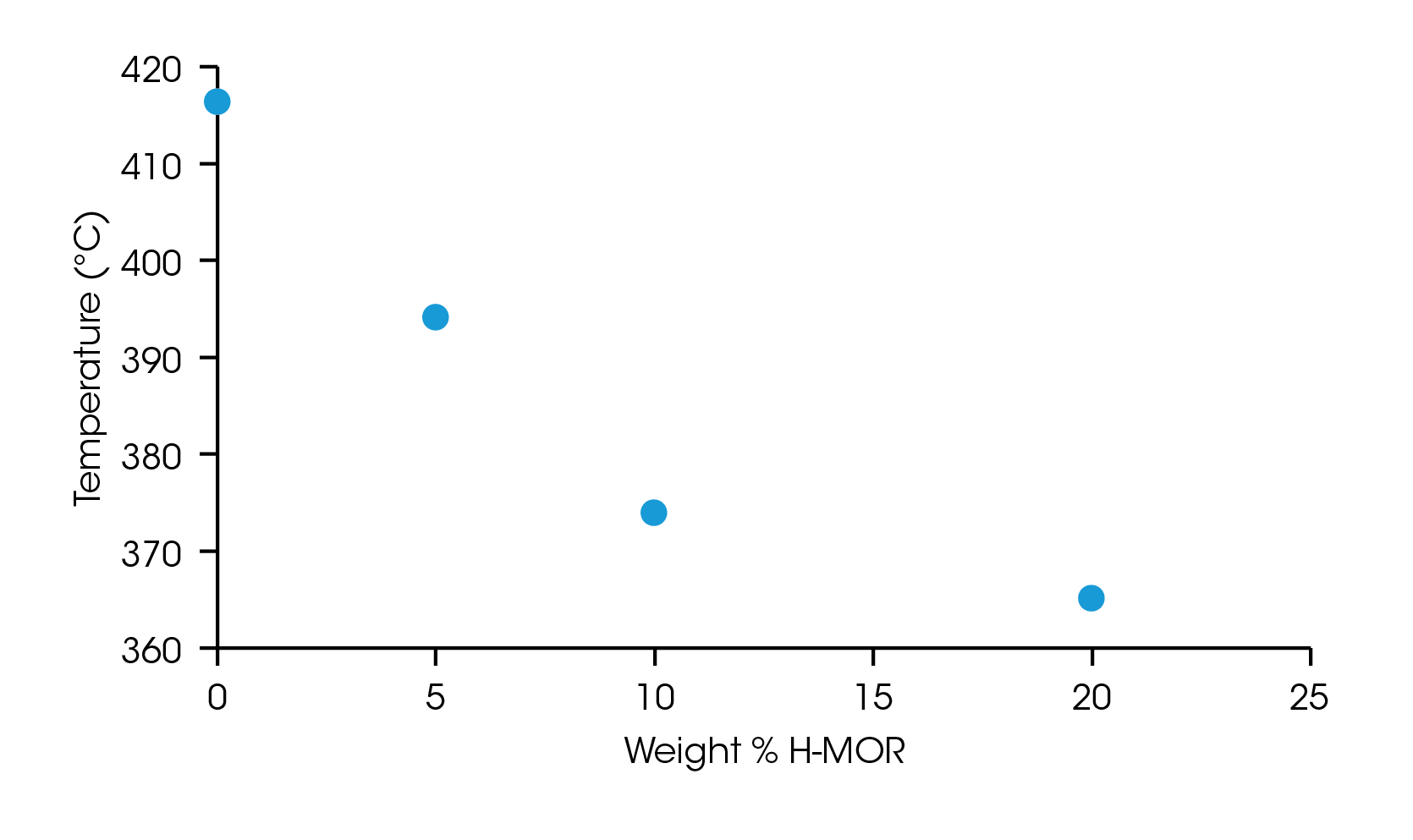
Table 1. Onset of degradation for samples of LDPE with increasing loading of H-MOR catalyst
H-MOR Loading (wt%) | Onset of Degradation (°C) |
---|---|
0 | 416.3 |
5 | 394.1 |
10 | 373.9 |
20 | 365.1 |
Conclusions
Pyrolysis technology development has become increasingly important in the recycling of polymers. This note demonstrates the utility of the Discovery TGA as a screening tool for catalyst design in pyrolysis. TGA enables efficient screening of process variables like catalyst loading and its effect on the onset temperature of polymer degradation. As demonstrated here, increasing amounts of H-MOR catalyst reduced the onset temperature of degradation in LDPE. Catalyst performance can also affect the ratio of recoverable products, which can be confirmed using the residue information from TGA experiments. The residue measured in these TGA experiments was equivalent to the amount of catalyst used, but in general may vary depending on catalyst performance, polymer identity, and residual impurities.
References
- A. Lopez, I. de Marco, B. M. Caballero, M. F. Laresgoiti and A. Adrados, “Influence of time and temperature on pyrolysis of plastic wastes in a semi-batch reactor,” Chemical Engineering Journal, vol. 173, pp. 62-71, 2011.
- S. Hafeez, E. Pallari, G. Manos and A. Constantinou, “6- Catalytic Conversion and Chemical Recovery,” in Plastics to Energy, William Andrew Publishing, 2019, pp. 147-172.
- S. M. Al-Salem, A. Antelava, A. Constantinou, G. Manos and A. Dutta, “A review on thermal and catalytic pyrolysis of plastic solid waste (PSW),” Journal of Environmental Management, vol. 197, pp. 177-198, 2017.
- M. G. Shelyapina, E. A. Krylova, A. S. Mazur, A. A. Tsyganenko, Y. V. Shergin, E. A. Satikova and V. Petranovskii, “Active Sites in H-Mordenite Catalysts Probed by NMR and FTIR,” Catalysts, vol. 13, no. 344, 2023.
Click here to download the printable version of this application note.