Keywords: Cement, Building Materials, Sulfate, Microcalorimeters, ASTM C150, EN197, SO3, Isothermal Microcalorimetry
MC171
Abstract
William Lerch published a paper in 1946 on the optimum sulfate content in Portland cement, which demonstrated that the optimum sulfate content with respect to mortar strength correlated closely with heat of hydration measured by isothermal calorimetry, and also with the length change of mortar bars stored in water. Lerch concluded that a Portland cement with close to optimum sulfate content would display a calorimetry heat profile with the time of sulfate depletion occurring after the main silicate hydration peak. The results of Lerch were reviewed and it was showed that calorimetry might be used to consider optimum sulfate levels also for mixture with cement and admixture.
Introduction
Sulfate is added to clinker in the manufacture of Portland cement for the purpose of retarding the hydration of the aluminate phase. Codes such as ASTM C150 and EN197 regulate the maximum sulfate expressed as SO3 with respect to durability, but no SO3 minimums are assigned. An extensive study by William Lerch /1/ used isothermal calorimetry to study the influence of gypsum addition rates to range of commercial clinkers on the hydration performance of corresponding Portland cements in terms of strength development and dimensional stability. It was concluded that the optimum sulfate content for maximum strength usually correlates with minimum dimensional change during water storage. The optimum sulfate content was easily identified by a calorimetry heat profile.
Admixtures in general may have an impact both on the activity of the aluminate phase (which needs sufficient sulfate to be retarded enough to avoid slump loss) and the solubility of sulfate (which impacts how available the sulfate is to react with aluminate). As a result, most admixtures have some impact on the optimum SO3 of a mixture compared to the same mixture without admixture. Consequently, a given cement that has sufficient SO3 without admixture may experience a lack of sulfate in presence of admixture. This is especially true for some highly reactive class C fly ashes, due to their content of reactive aluminate, and for chemical admixtures that accelerate the aluminate hydration.
Hydration Phenomena Governing Set and Strength Development
Portland cement has four major phases, aluminate “C3A”, Alite “C3S”, Belite “C2S”, and ferrite “C4AF”. The aluminate ids the most reactive phase, and therefore has the largest impact on workability as it consumes large amounts of water upon hydration. The Alite is the second most reactive phase, with strong impact on set and strength development. Set occurs when enough hydrates has formed to interlock particles and restrict their flow. Therefore, the set time is strongly affected by the free water content (determines how much hydrates must form before particles become interlocked) and both the aluminate and the Alite rate of hydration.
The aluminate and Alite compete for water for their hydration. Since aluminate is much more reactive, it is critical to have enough sulfate available to retard the aluminate. Sulfate must first dissolve before it can react with aluminate to form ettringite, which coats the surface and retards the aluminate hydration. If not enough sulfate is available to slow down the aluminate hydration, loss of workability or even flash set may occur as the aluminate hydrates formed rapidly consume free water. Since the aluminate hydrates also tend to coat the Alite, excess aluminate hydrates may retard and partly prevent the onset of the strength giving Alite hydration.
Calorimetry Heat Profiles from Hydrating Portland Cement in PResence of Admixture
Fig. 1 shows an example of the effect of a typical water-reducing admixture on the hydration of a Portland monitored at room temperature by an isothermal conduction calorimeter. The Portland cement by itself had a slightly higher than optimum sulfate content, as seen by the sulfate conversion peak appearing several hours after the maximum of the main silicate hydration peak. As the water-reducing admixture was added to the mixture at increasing dosages, the aluminate reactivity increased while the main strength giving silicate hydration was retarded. As a consequence, note how the sulfate depletion peak appeared closer and closer to the maximum of the main silicate hydration peak. Eventually, the sulfate depletion peak appeared before the now strongly retarded silicate hydration peak, when a strong overdose of admixture was used.

Laboratory Screening of the Stability of Cement-Admixture Combinations
Based on the results shown in Fig. 1, it was concluded that the tested cement-admixture combination appears to be “robust” because a 50% admixture overdose was not enough to significantly alter the cement hydration profile. As a rule of thumb, one should always test a candidate cement-admixture combination at an overdose of admixture, because the result will indicate if a mixture is close to an “out-of-balance” situation or not. If an intended mixture is close to being “out-of-balance”, one should look for a more stable mixture design. Mixtures close to “out-of-balance” typically result in undesired high variability in concrete setting time, strength development, and sometimes also premature stiffening as a result of not properly controlled aluminate hydration. Since cement has an inherent natural variability in composition and reactivity, and concrete conditions vary, it is very important to design “robust” mixtures that can tolerate minor variations in reactivity without the mixture being put “out-of-balance”.
It would be impossible for a cement producer to test all their cements for all possible admixture combinations. Cement is used in many different processes, cement contents, and temperatures, making it impossible to optimize the sulfate content for all situations. Furthermore, restrictions imposed by ASTM, states, DOT’s, AAHSTO; etc often limits the total SO3 allowed in cement. On the other hand, one can select a few most common admixture combinations that represent the local marketplace, and then use these combinations for screening cement. Such screening should be done whenever there is a known change in cement composition or process, or when concrete producers are developing new mixture designs.
Likewise, it would be impossible for concrete producers to test all incoming cement loads for all admixture combinations used. However, screens would be recommended whenever there is a known change in type or amount of the materials used, or when there is a significant change in concrete curing temperature.
Test for the Effect of Additional Soluble Sulfate
Unstable cement–admixture combinations usually display a sulfate depletion peak appearing before or at the same time as the main silicate hydration peak. It is then recommended to run a separate test series with additional soluble sulfate added to the cement. The added sulfate test will help to confirm the location of the sulfate depletion peak, which is sometimes difficult to identify if it is completely overlapping the main silicate peak. The added sulfate test would also prevent any “unknown” hydration peaks (such as early aluminate hydration induced by accelerating admixtures) from being mistaken for a sulfate depletion peak. Sulfate is usually added in the form of calcium sulfate hemihydrate (plaster), since this is the most soluble form of calcium sulfate. Fig. 2 shows an example of a sulfate test on a cement-admixture combination that appears to be unstable.
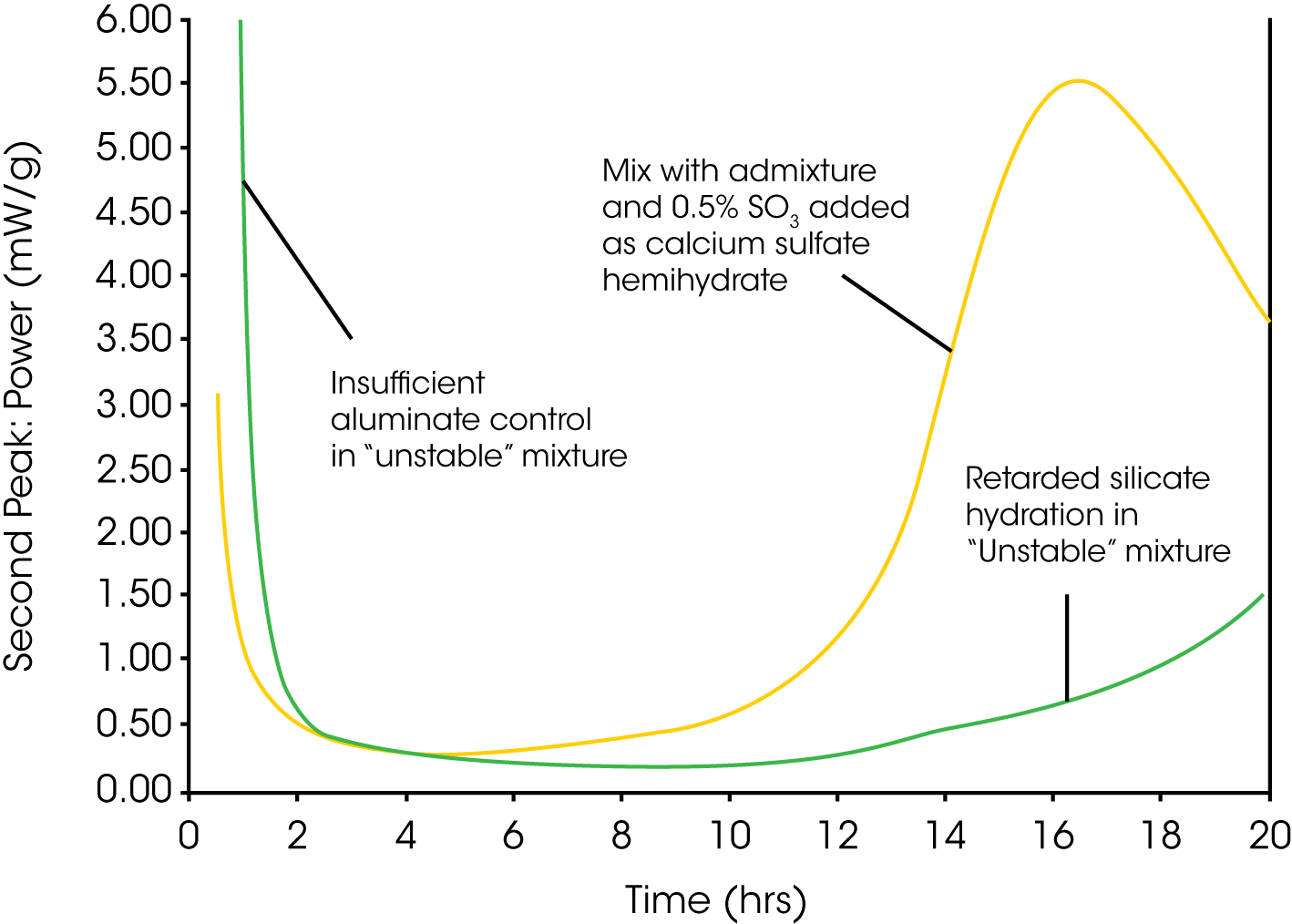
Conclusion
Calorimetry can be a very useful tool for screening cement-admixture combinations with respect to hydration stability. Repeated tests are recommended, as single tests can usually not tell if a given mixture design is very sensitive to changes or not.
Most aspects of cement hydration and performance with admixture involve heat evolution, and can therefore be monitored by calorimetry. Certain processes however, such as excess air entrainment and false set, involve so little heat relative to the overall process, that calorimetry is not a suitable screening tool.
Loss of workability or slump in concrete can to some extent be assessed by calorimetry on cement paste, by monitoring the heat associated with aluminate hydration before time of placing. Note however that calorimetry results reflect chemical aspects only. Any physical effects such as absorption on aggregate fines cannot be assessed by calorimetry tests only. Since the heat evolution measured in an externally mixed sample does not become quantitative until 10-15 minutes after inserting the sample into the calorimeter, one must use some caution when comparing heat evolution during the first 15 minutes. Slump loss occurring more than 15 minutes after initial mixing would be detectable as an increased heat evolution only if it is induced by an acceleration of the aluminate hydration.
References
- Lerch, William. “The influence of gypsum on the hydration and properties of Portland cement pastes”, Proceedings, Vol. 46, of the American Society for Testing Materials, 1946
- Sandberg, Paul. “The use of Isothermal Calorimetry to optimize cement sulfate. Part 1 – Cement without admixture. Internal document, Grace Construction Products
Acknowledgement
Click here to download the printable version of this application note.