Keywords: Cement, Building Materials, Sulfate, Microcalorimeters, ASTM C150, EN197, SO3, Isothermal Microcalorimetry
MC170
Abstract
In 1946 William Lerch published a paper on the optimum sulfate content in Portland cement, which demonstrated that the optimum sulfate content with respect to mortar strength correlated closely with heat of hydration measured by isothermal calorimetry, and also with the length change of mortar bars stored in water. Lerch concluded that a Portland cement with close to optimum sulfate content would display a calorimetry heat profile with the time of sulfate depletion occurring after the main silicate hydration peak. The results of Lerch were reviewed in light of the development of modern “easy-to-use” calorimeters and their potential usefulness for the cement industry.
Introduction
Sulfate is added to clinker in the manufacture of Portland cement for the purpose of retarding the hydration of the aluminate phase. Codes such as ASTM C150 and EN197 regulate the maximum sulfate expressed as SO3 with respect to durability, but no SO3 minimums are assigned.
An extensive study by William Lerch /1/ used isothermal calorimetry to study the influence of gypsum addition rates to a range of commercial clinkers on the hydration performance of corresponding Portland cements in terms of strength development and dimensional stability. It was concluded that the optimum sulfate content for maximum strength usually correlates with minimum dimensional change during water storage.
The optimum sulfate content was easily identified by a calorimetry heat profile. Optimum sulfate with respect to strength development and dimensional stability occurred when the depletion of soluble sulfate used up by aluminate hydration occurred at a time later than the maximum heat evolution from the main silicate hydration peak, Figure 1.
Figure 1 shows an example of hydrating Portland cement with slightly higher than optimum sulfate content monitored at room temperature by an isothermal conduction calorimeter. Portland cement mixed with water initially displays a strong exotherm caused (A) by rapid dissolution and initial hydration of mainly the aluminate phase. If sufficient sulfate is available in solution, the hydration rate rapidly decreases (B) as aluminate reacts with calcium and sulfate to form ettringite. The formation of ettringite prevents so called “Flash Set” and allows the concrete to be transported and placed while it is still fluid. After some time the strength giving Alite hydration takes off, which results in a broad exotherm (C). “Set” usually occurs at the initial part of the Alite exotherm. The Alite and aluminate hydration continue in parallel until the mixture runs out of soluble sulfate (D), which initiates the formation of aluminates with less sulfate than ettringite.
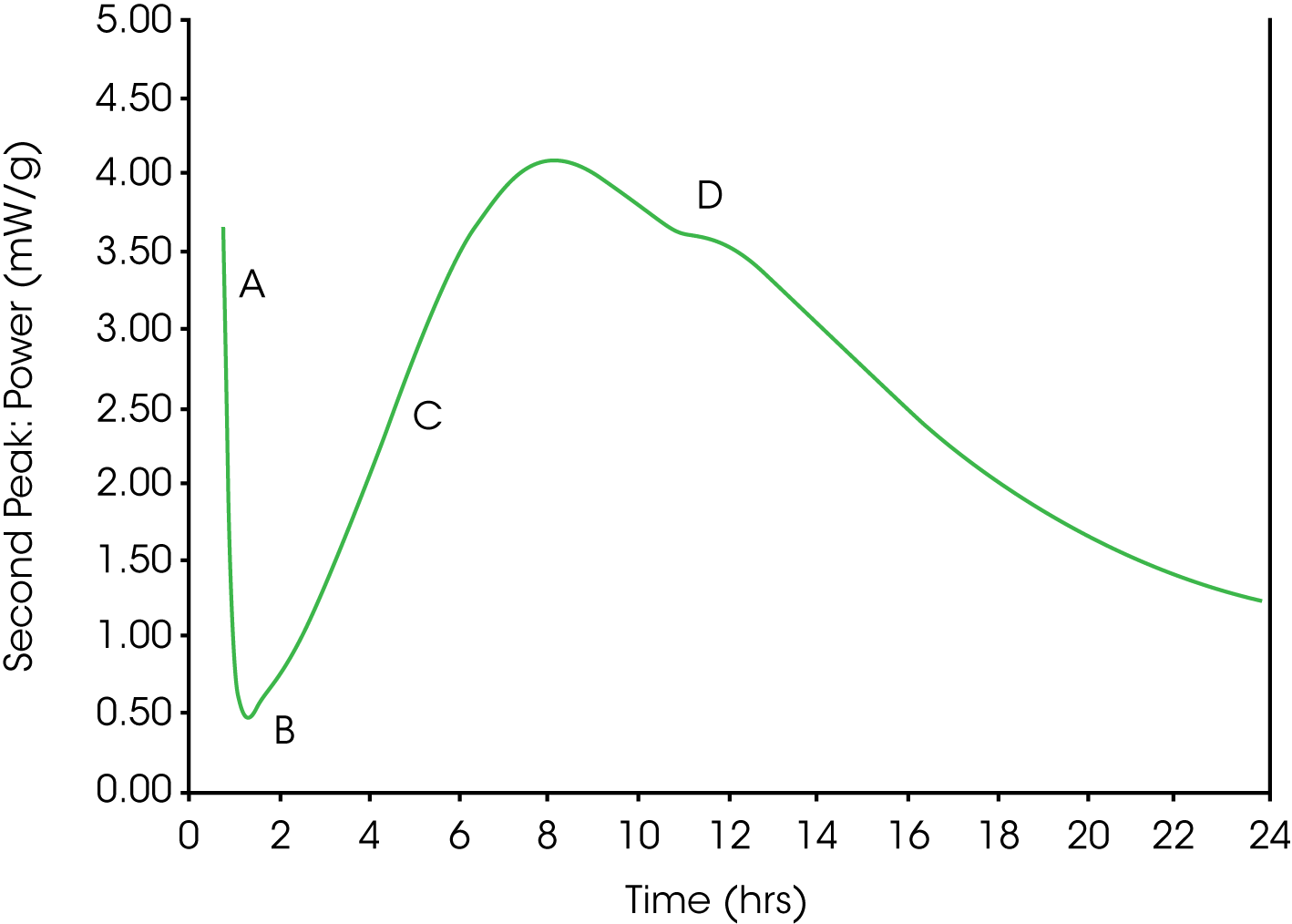
Laboratory Screening of Optimum SO3 for a Portland Cement by Isothermal Calorimetry
Figure 2 shows how Lerch’s criteria – sulfate depletion peak to occur after the main silicate peak – can be used for a rapid indication of the optimum sulfate content of a laboratory ground clinker.
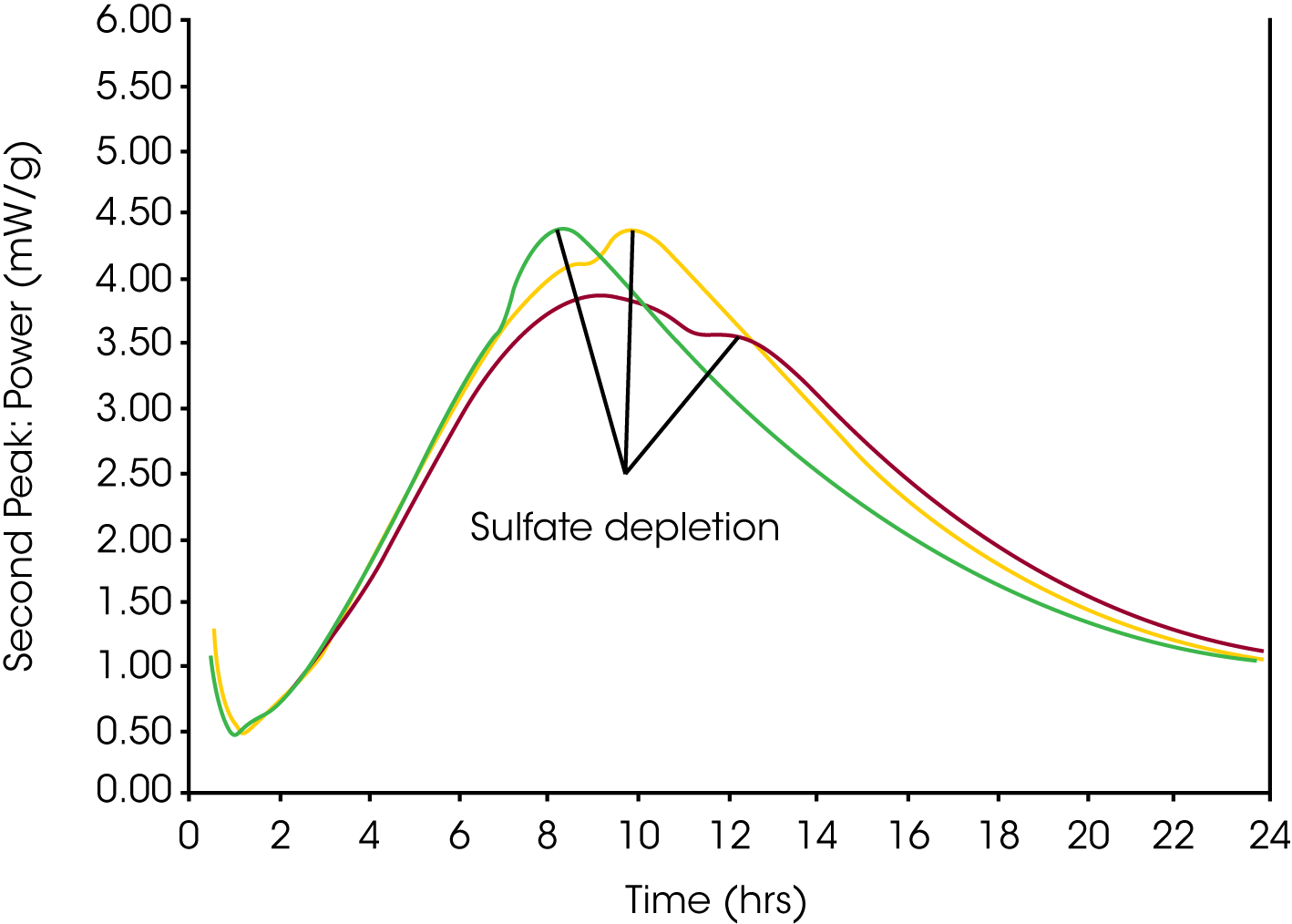
Evaluation of Laboratory Results and Further Field Tests for Sulfate Optimum
The results of the laboratory screening shown in Fig. 2 indicate that 2.5% added SO3 might be sufficient to bring the resulting Portland cement to optimum SO3 level. At this stage a field trial would be recommended, since several factors may cause cement manufactured in the field to perform different as compared to the laboratory ground cement. Such factors include:
- Sulfate becomes more effective if interground (as compared to simple addition to cement)
- The mill circuit in the field is probably very different from the lab. This results in a different particle size distribution, and hence a different reactivity of the cement. The net result is likely a different optimum SO3 for the field cement.
- The solubility of different sulfate forms depends on the manufacturing conditions.
Figure 3 shows the results of a field trial in which cements where produced at increasingly higher dosages of gypsum into the mill, which resulted in a range of total SO3 contents. The variation in response reflects the natural variation in cement composition.
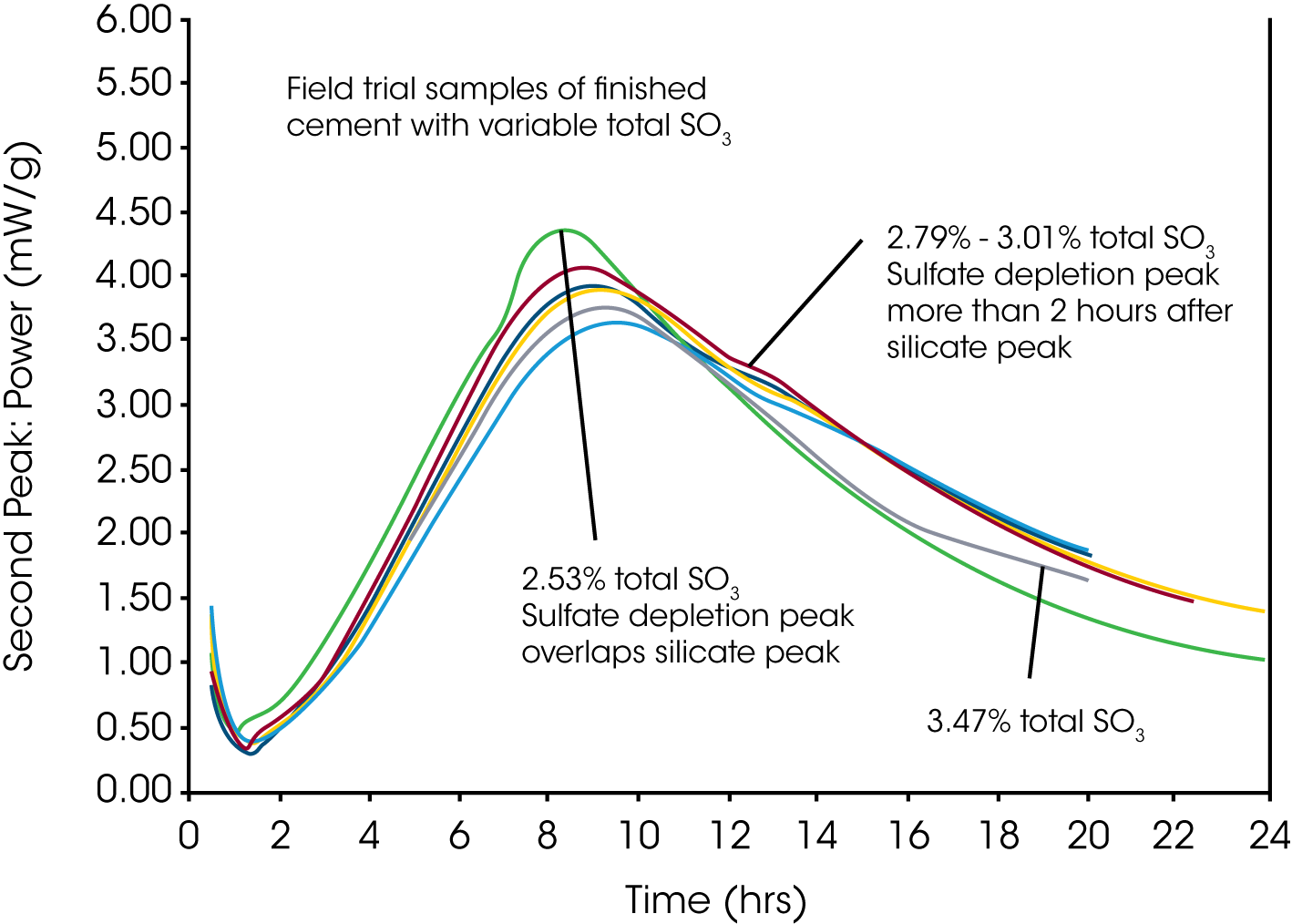
Selecting a Target SO3 Based on Isothermal Calorimetry
The optimum SO3 for production would be selected using knowledge on the variability of total SO3 in the finished cement. This variability may be influenced by the accuracy of the gypsum dosing system, alkali in raw materials, SO3 in fuel, etc. The example in Fig. 3 indicates that 2.8% total SO3 would be sufficient to delay the sulfate depletion peak until more than 2 hours after the maximum of the main silicate hydration peak. The target total SO3 of the cement would be chosen to ensure that 95% of the cement produced has 2.8% or higher total SO3.
It is also important to consider how the cement is used in the local market place. Most concrete is produced with admixtures, both chemical admixtures (water reducers, accelerators, retarders, etc.) and mineral admixtures (granulated slag, fly ash, natural pozzolans, etc.) In general, the use of admixtures leads to a more rapid depletion of soluble sulfate. Therefore, as a rule of thumb, the conversion peaks should appear no earlier than 2 hours after the maximum of the main silicate hydration peak to allow for common, general use of admixtures with the cement.
Final Remarks
In practice the method for determining the gypsum addition rate is often based on an evaluation of several factors such as gypsum and clinker costs, the response of the main concrete customers to strength and dimensional stability, and local state/DOT/AASHTO directives. However, the calorimetry serves as an excellent indication as to the approximate values to aim for to avoid setting time and admixture incompatibility issues. Furthermore, the calorimetry can be used to asses the efficiency of any changes made to the cement production, such as changes in gypsum type or changes in raw material or fuel that may influence the reactivity of the aluminate phase and thereby the demand for soluble SO3.
References
- Lerch, William. “The influence of gypsum on the hydration and properties of Portland cement pastes”, Proceedings, Vol. 46, of the American Society for Testing Materials, 1946
Acknowledgement
Click here to download the printable version of this application note.