The increasingly sophisticated nature of aerospace and defense systems places extraordinary demands on material performance. Understanding how materials respond under extreme temperature gradients, mechanical stress, and harsh environmental conditions requires precision instrumentation capable of replicating these challenging scenarios in controlled laboratory settings. High-performance composites, specialty polymers, aerospace-grade adhesive systems, protective coatings, environmental sealants, and advanced metallurgical alloys constitute the foundation of this materials revolution-transforming theoretical possibilities into realities.
Today, evolving mission requirements and stringent safety regulations necessitate a comprehensive understanding of material behavior across the entire product life cycle. Leading OEMs, specialized tier suppliers, and government research laboratories are fundamentally reassessing their approach to material qualification protocols, manufacturing process optimization, and predictive performance modeling. TA Instruments | Waters Corporation provides essential analytical solutions that empower engineers and scientists to design, validate, and deploy cutting-edge technologies with confidence.
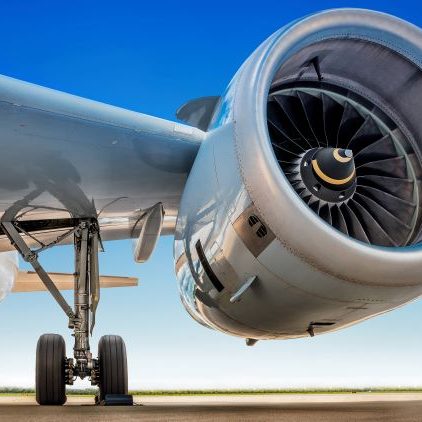
Aerospace & Defense Solutions: Enabling Mission-Critical Innovation
TA Instruments provides essential thermal analysis, rheology, and mechanical testing solutions trusted by leading Aerospace & Defense organizations to solve their most complex material challenges:
- Accelerate qualification of advanced composites/metals for extreme environments
- Optimize manufacturing of next-gen propulsion systems and airframe structures
- Ensure operational reliability through predictive lifecycle testing
This critical phase focuses on formulating, screening, and fundamentally understanding advanced polymers, composites, adhesives, coatings, and sealants. We provide essential tools to characterize core thermal transitions, flow behavior, cure and crystallization kinetics, thermomechanical properties, and degradation pathways. These insights enable the development of structure-property relationships, support computational modeling efforts, and accelerate the selection of materials engineered to meet extreme performance targets in demanding aerospace and defense environments.
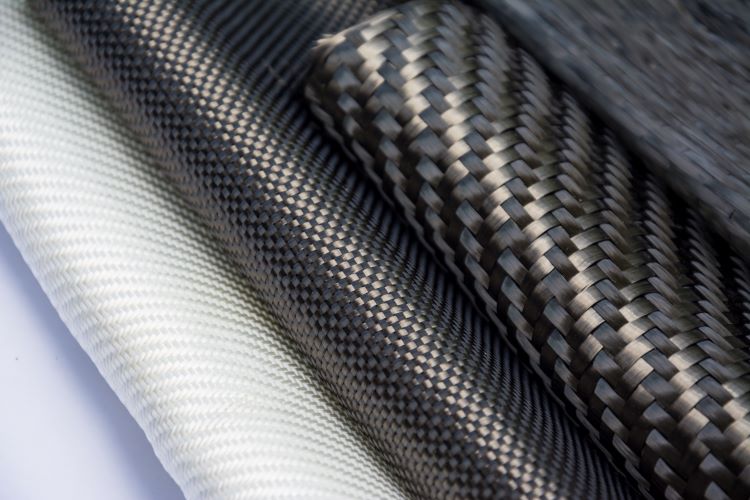
Differential Scanning Calorimeters (DSC)
- Gel Time
- Phase transitions
- Melting Temperature (Tm)
- Heat of Fusion
- Glass Transition (Tg)
- Crystallinity
- Heat Capacity
- Thermal Stability
Thermomechanical Analyzers (TMA)
- Coefficient of Thermal Expansion (CTE)
- Glass Transition Temperature (Tg)
- Decomposition Onset
- Residual Stress
Thermogravimetric Analyzers (TGA)
- Thermal Stability
- Decomposition Temperatures
- Max Service Temperatures
- Composition determination
- Glass Fiber Content
- Additives
- Propellant Stability Assessment (STANAG 4582)
- Stabilizer Compatibility Testing
- Humidity Impact Analysis
- Coefficient of Thermal Expansion (CTE)
- Phase Transitions
- Sintering Behavior
- Thermal Cycling
Leveraging fundamental material data is key to optimizing advanced manufacturing processes like automated fiber placement, additive manufacturing, welding, forming, and infusion. Our instruments help define precise processing windows by characterizing viscosity profiles, cure/crystallization kinetics under process-relevant conditions, and thermal stability limits. Understanding material flow, solidification behavior, and thermomechanical response during manufacturing enables enhanced process control, predictive simulation, improved quality, and higher production rates.
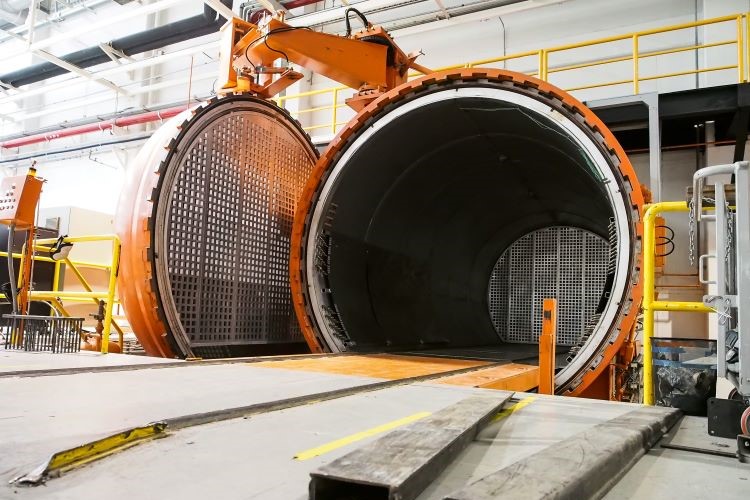
- Gel Time
- UV-Curing
- Dielectric Measurements
- Melt Strength
- Processability
- Viscosity Flow Curve
- Zero Shear Viscosity
- Viscoelastic Properties (Storage Modulus, Loss Modulus)
- Crossover Modulus and Frequency
Differential Scanning Calorimeters (DSC)
- Glass Transition Temperature (Tg)
- Thermal Stability
- Oxidative Induction Time (OIT)
- Oxidative Onset Time (OOT)
- Curing Exotherm
Dynamic Mechanical Analyzers (DMA)
- Creep
- Glass Transition Temperature (Tg)
- Storage Modulus, Loss Modulus, tan delta
- Blend Compatibility
Ensuring components meet stringent performance and reliability standards requires thorough validation. Our analytical tools verify that the final material state meets design specifications after manufacturing. We enable the assessment of thermomechanical performance across operational conditions, characterize long-term durability behavior like creep and stress relaxation, evaluate the integrity of bonded joints and coatings, and help understand the impact of manufacturing variability on component life and reliability for certification.
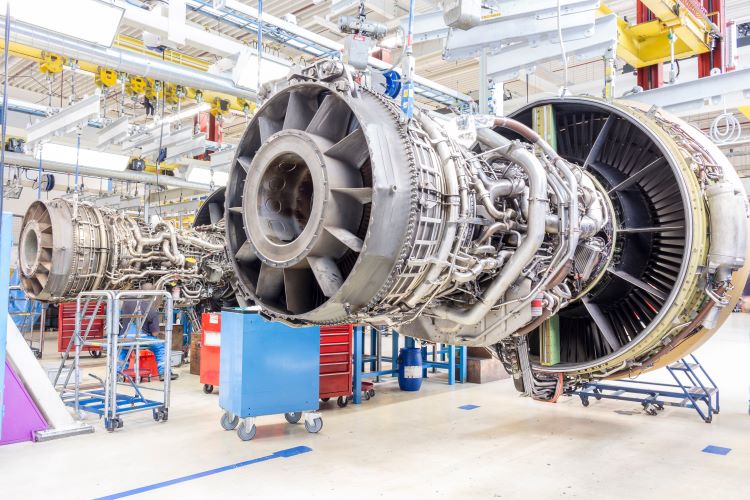
Thermomechanical Analyzers (TMA)
- Coefficient of Thermal Expansion (CTE)
- Glass Transition Temperature (Tg)
Differential Scanning Calorimeters (DSC)
- Residual Cure Detection
- Thermal Degradation Thresholds
- Phase Change Validation
Dynamic Mechanical Analyzers (DMA)
- Creep
- Mechanical Anisotropy
- Heat Deflection Temperature
ElectroForce Mechanical Testers
- Material Strength
- Tensile
- Modulus
- Yield Strength
- Final Assembly Strength
- Flexural
- Fatigue
- Compression After Impact (CAI)
- Materials Development & Characterization
-
This critical phase focuses on formulating, screening, and fundamentally understanding advanced polymers, composites, adhesives, coatings, and sealants. We provide essential tools to characterize core thermal transitions, flow behavior, cure and crystallization kinetics, thermomechanical properties, and degradation pathways. These insights enable the development of structure-property relationships, support computational modeling efforts, and accelerate the selection of materials engineered to meet extreme performance targets in demanding aerospace and defense environments.
Differential Scanning Calorimeters (DSC)
- Gel Time
- Phase transitions
- Melting Temperature (Tm)
- Heat of Fusion
- Glass Transition (Tg)
- Crystallinity
- Heat Capacity
- Thermal Stability
Thermomechanical Analyzers (TMA)
- Coefficient of Thermal Expansion (CTE)
- Glass Transition Temperature (Tg)
- Decomposition Onset
- Residual Stress
Thermogravimetric Analyzers (TGA)
- Thermal Stability
- Decomposition Temperatures
- Max Service Temperatures
- Composition determination
- Glass Fiber Content
- Additives
- Propellant Stability Assessment (STANAG 4582)
- Stabilizer Compatibility Testing
- Humidity Impact Analysis
- Coefficient of Thermal Expansion (CTE)
- Phase Transitions
- Sintering Behavior
- Thermal Cycling
- High-Rate Manufacturing Optimization
-
Leveraging fundamental material data is key to optimizing advanced manufacturing processes like automated fiber placement, additive manufacturing, welding, forming, and infusion. Our instruments help define precise processing windows by characterizing viscosity profiles, cure/crystallization kinetics under process-relevant conditions, and thermal stability limits. Understanding material flow, solidification behavior, and thermomechanical response during manufacturing enables enhanced process control, predictive simulation, improved quality, and higher production rates.
- Gel Time
- UV-Curing
- Dielectric Measurements
- Melt Strength
- Processability
- Viscosity Flow Curve
- Zero Shear Viscosity
- Viscoelastic Properties (Storage Modulus, Loss Modulus)
- Crossover Modulus and Frequency
Differential Scanning Calorimeters (DSC)
- Glass Transition Temperature (Tg)
- Thermal Stability
- Oxidative Induction Time (OIT)
- Oxidative Onset Time (OOT)
- Curing Exotherm
Dynamic Mechanical Analyzers (DMA)
- Creep
- Glass Transition Temperature (Tg)
- Storage Modulus, Loss Modulus, tan delta
- Blend Compatibility
- Component Validation & Certification
-
Ensuring components meet stringent performance and reliability standards requires thorough validation. Our analytical tools verify that the final material state meets design specifications after manufacturing. We enable the assessment of thermomechanical performance across operational conditions, characterize long-term durability behavior like creep and stress relaxation, evaluate the integrity of bonded joints and coatings, and help understand the impact of manufacturing variability on component life and reliability for certification.
Thermomechanical Analyzers (TMA)
- Coefficient of Thermal Expansion (CTE)
- Glass Transition Temperature (Tg)
Differential Scanning Calorimeters (DSC)
- Residual Cure Detection
- Thermal Degradation Thresholds
- Phase Change Validation
Dynamic Mechanical Analyzers (DMA)
- Creep
- Mechanical Anisotropy
- Heat Deflection Temperature
ElectroForce Mechanical Testers
- Material Strength
- Tensile
- Modulus
- Yield Strength
- Final Assembly Strength
- Flexural
- Fatigue
- Compression After Impact (CAI)
Aerospace, Military, & Defense Resources
Aerospace, Military, & Defense Video Resources
Aerospace, Military, & Defense Blogs
Application Notes
- Flexural Fatigue Behavior of Woven Fiberglass Composites at Elevated Temperature
- Using an ARES Rheometer to investigate the β-relaxation change of graphene poly(ethylmethacrylate) nanocomposite
- Characterization of the Degree of Cure of Thermosetting Resins by DSC
- Stress/Strain Evaluation of Fibers Using TMA