醫療器材的材料耐久性試驗
疲勞試驗如何使器材更可靠
Troy Nickel | Morgan Ulrich
February 03, 2023
您的患者是否擔心在跑步時,置換的髖關節發生骨折?或是他們的義足能使用多久?何時需更換新品?您是否需要提交越來越多有關使用壽命試驗的審查文件?
什麼是醫療器材的耐久性試驗?
耐久性試驗也稱為疲勞或應力試驗,亦即使器材承受生理負荷來驗證使用壽命。也可利用疲勞至斷裂方法及超出生理負荷程度來瞭解器材失效情形並設計範圍。耐久性試驗主要是幫助防止意外的產品故障,以免產生嚴重後果。
耐久性試驗包括對植入式醫療器材重複進行物理性加載,方式與在人體內隨著時間遇到的負荷非常相似。試驗通常包括利用力度、扭矩、旋轉、應變、位移和/或壓力,對器材或特定元件施加廣泛及標靶性的負載。負載有時會應用於整個器材,有時會應用於器材的子元件或材料。
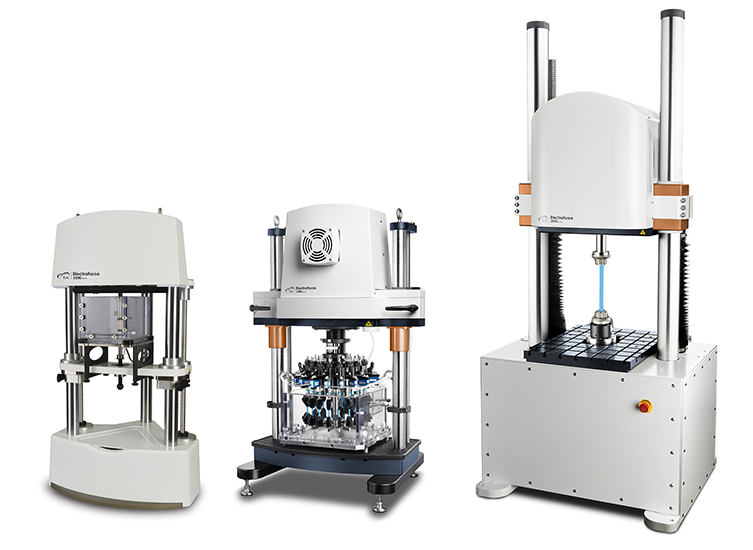
什麼是耐久性試驗方法?
測試負載通常透過兩種試驗方法重複 應用:
疲勞試驗至成功
例如,疲勞試驗至成功的試驗可以證實植入體在承受 1000 萬次循環 (大約 10 年步行和跑步的使用壽命)生理程度的負荷時不致故障。
疲勞至斷裂
疲勞至斷裂 (FtF) 施以更大的負載幅度使器材超過故障極限,來瞭解器材中最脆弱的元件位置。該方法通常用於器材開發早期,因為它提供的見解有助於完善器材的最終設計。而且由於疲勞至斷裂結果提供了更有力的可靠性證據及更嚴格的安全範圍評估,因此越來越常用於審查文件中。
例如,您可能會以 2 倍的生理程度測試植入體來確定故障方式與時間,然後以 2.5 倍或 1.5 倍來瞭解使用壽命如何隨著負載程度的變化而增減。該方法以不同程度重複施用於許多試樣,以便在負載程度與植入體使用壽命之間的關係獲得越來越高的可信度。
醫療器材的疲勞試驗系統
如上所述,設計新醫療器材的材料與產品需要在預期的最終用途範圍內(有時甚至超出預期的最終用途)對材料特性進行全面評估及完整的性能鑑定。靈活而堅固的儀器能夠準確並及時執行特定於器材的試驗標準,並對骨科器材測試進行嚴格的性能評估。
ElectroForce 技術徹底改變了材料測試的執行方式。這些儀器經過驗證可進行超級可靠的疲勞與耐久性試驗,是全球醫療器材實驗室中的主要儀器。
哪種儀器適用於我的實驗室?
為您的醫療器材測試選擇儀器之前,首先需要提出明確的需求:
- 為疲勞試驗至成功還是疲勞至斷裂?抑或兩者兼具?
- 測試材料或器材必須承受什麼樣的力?位移多少?
- 我的器材將在什麼環境中運行?即在空氣中、流體中或是特定溫度等。
ElectroForce 負載機架測試儀器系列包含適用於各種應用的一系列力和性能。最常用於醫療器材測試的型號包括 ElectroForce 3200、ElectroForce 3300、ElectroForce 3500 和多試樣疲勞儀。請查看下表找出符合您需求的儀器。
ElectroForce 3200 | ElectroForce 3300 | ElectroForce 3500 | MSF 6 | MSF 16 | |
---|---|---|---|---|---|
試樣數量 | 1 | 1 | 1 | 6 | 16 |
力範圍(每個試樣) | 0.002 to 450 N | 0.02 to 3000 N | 1 to 15,000 N | 0.005 to 225 N | 0.005 to 100 N |
位移範圍 | 0.002 to 13 mm 163mm optional |
0.005 to 25 mm, 175 mm optional |
0.005 to 50 mm | 0.005 to 25 mm, 175 mm optional |
0.005 to 25 mm |
最大疲勞頻率 | 300 Hz | 100 Hz | 100 Hz | 100 Hz | 100 Hz |
ElectroForce 負載機架儀
TA ElectroForce® 測試儀採用專利的 ElectroForce 線性傳動技術,結合先進的控制與分析軟體。由無摩擦電磁馬達驅動,為機械疲勞和動態特徵分析提供嶄新的試驗方法。由於乾淨與免維護操作,它們也非常適合用於實驗室。因此,它們為單一測試儀器的性能、可靠性和多功能性設下新標準。
ElectroForce 3200、3300 與 3500 負載機架
該系列負載機架極為靈活,提供多種負荷範圍及機架配置。它們均利用特定於力範圍的高性能摩擦電機、HADS 感測器以及靈活便利的機架功能,非常適合用於測試許多材料、元件與器材。
Electroforce™ 多試樣疲勞儀
多試樣疲勞 (MSF) 儀由強大且多功能的 3300 負載機架構建而成,可同時測試多個試樣來提高疲勞試驗效率。每個試樣均承受相同的位移,例如 30Hz 時 1 公釐,但有單獨的力感測器來偵測每個試樣的力衰減或失效。這些儀器特別適合用於彈性材料或器材的高週期疲勞計畫,其中每個試樣可能需要數天、數週,甚至數月才能失效。這種方法可以大幅提高您的生產率並縮短上市時間。
ElectroForce 3300 6 試樣 MSF 儀
MSF6 在高達 225N 的壓力下同時測試 6 個試樣來提高試樣效率。它廣泛用於彈性聚合物、彈性體或是更有彈性的金屬或結構。MSF6 也可以安裝在烤箱內操作,讓您更全面地瞭解器材或材料在不同溫度下的性能,例如將義足置於明尼蘇達州冬季或德州夏季時的情況。
ElectroForce 3300 16 試樣 MSF 儀
MSF16 提供無可比擬的 16 個試樣容量,且每個試樣可高達 100N。最佳化的設計提高試樣的便利性和可見性,以簡化試樣加載及查看。它包括一個 37 °C 流體浴槽,廣泛用於小型器材或金屬疲勞,例如鎳鈦合金和其他定製形狀記憶合金 (SMA)。
ElectroForce 負載機架及多試樣疲勞測試儀是業界領先的醫療器材耐久性試驗儀器。
詳細瞭解 TA Instruments 業界領先的醫療器材耐久性試驗。TA Instruments 還提供許多其他測試儀器,對於分析用來生產醫療器材的材料和方法的特徵而言非常有用。