폴리머 첨가제는 수지의 성질을 강화하며 특정 용도에 맞게 다듬어 가치를 높입니다. 배합업체와 첨가업체는 안정제, 화합제, 산화방지제, 착색제 등의 적합한 조합을 순수 수지와 결합하여 가공에 사용할 제제를 만듭니다. 변환업체는 이처럼 미리 형성된 화합물을 가지고 바로 가공 작업에 돌입할 수 있습니다. 첨가제는 가공 도중에 기본 수지와 함께 가라앉기 때문에 농축 마스터배치로 유연하고 경제적인 첨가제 조제 옵션을 제공하기도 합니다.
첨가제 제조사와 배합업체, 첨가업체는 폴리머 특성 분석을 이용해 유입 수지의 성질을 철저히 파악하며, 첨가제에 의한 수지 변형을 평가하여 고객이 올바로 가공할 수 있도록 합니다.

기기 및 테스트 매개변수
응용 사례 – 폴리머 특성화와 가공
기본적으로 열가소성 가공의 핵심 단계는 3가지 기본 공정으로 나눌 수 있습니다.
- 열을 가하여 수지 녹이기/연화
- 최종 형태로 변형
- 제품을 식혀서 방출
생산 매개변수의 세부 사항이 서로 다르더라도 사출 성형, 압출부터 열성형, 필름 블로 몰딩에 이르기까지 다양한 폴리머 가공 기법에 위 세 단계를 적용할 수 있습니다. 여기서는 폴리머 가공의 모든 단계에서 흔하게 부딪치는 의문을 자세히 들여다보고 폴리머 특성화 기법으로 얻을 수 있는 인사이트를 이용해 답해 보겠습니다.
수지의 적정 가공 온도는 몇 도인가?
폴리머가 몇 도에서 연화되고 녹는지에 대한 것은 폴리머 가공에 관한 기본적인 재료 성질로서 꼭 알아야 합니다. 압축, 사출 성형, 필름 블로 몰딩 가공 등의 첫 단계에서는 수지 펠릿을 녹는점을 넘어 가열하는 것이 일반적입니다. 열성형과 블로 몰딩의 경우 유리 전이 온도 이상으로 수지를 가열하여 연화하되 완전히 녹이지는 않습니다. 단단한 수지 펠릿(낮은 에너지 상태)에서 연화되거나 완전히 녹은 펠릿(높은 에너지 상태)으로 변형하려면 에너지를 투입해야 하며 DSC(시차 주사 열량계)로 측정 가능합니다.
DSC 테스트에서는 온도가 정속 증가하므로 시료의 열흐름을 모니터링할 수 있습니다. 용융과 유리 전이 같은 열 전이는 높은 에너지 상태로 이동하면서 재료가 열을 흡수하는 흡열 이벤트로 나타납니다. 그 결과 폴리머 형태에 대한 정보도 드러납니다. 비정질 상태와 반결정체 상태 사이에 뚜렷한 차이를 보이죠. DSC 테스트의 1차 가열 주기 동안 비정질 재료는 녹지 않고 폭넓은 유지 전이를 보여주는 반면 반결정체 폴리머는 또렷하고 명확한 용해 최대치를 보여줍니다. 용해 온도와 유리 전이 온도는 폴리머마다 고유하기 때문에 이 정보를 이용하여 가공에 앞서 유입되는 공급 원료의 질을 신속하게 평가할 수 있습니다.
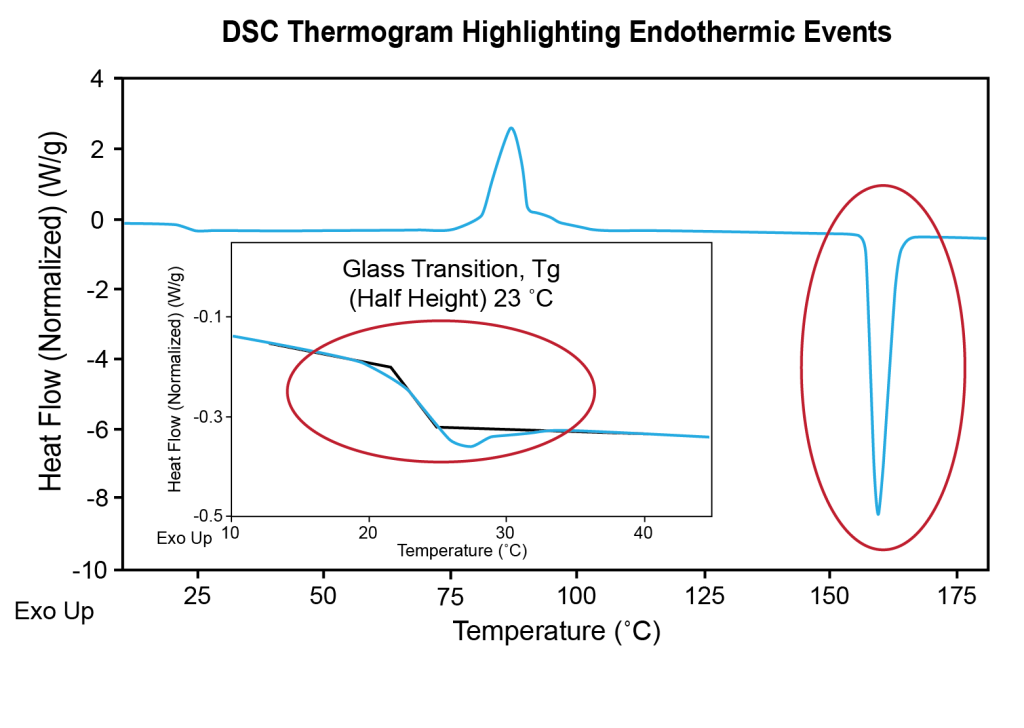
가공 및 최종 사용 중에 수지는 얼마나 안정적인가?
가공 도중, 그리고 최종 사용 조건에서 마주하게 되는 환경 영향으로 인한 질 저하를 막기 위해 수지에 안정제와 다른 첨가제를 첨가하는 경우가 많습니다. 가공 도중에 그리고 제품을 사용하면서 원래 의도한 폴리머의 성질을 유지하기 위해 산화방지제, 탈산소제, 열 및 자외선 안정제, 내연제 같은 첨가제를 넣습니다. 안정제는 본질적으로 소진되는 성질이 있어 고열이나 자외선에 노출되면 서서히 소모됩니다. 일단 안정제가 완전히 소진되면 폴리머의 성질은 급속도로 저하되기 시작합니다.
DSC에서 산화 유도 시간(OIT)을 통해 안정제의 성능을 평가할 수 있습니다. 이 등온 테스트에서는 DSC의 정화 가스가 질소에서 산소로 바뀌며 안정제가 소모되는 환경을 마련합니다. 폴리머 저하가 시작되는 시점에 열 흐름 신호가 상승하기 시작하고 시간은 OIT로 기록됩니다.
DSC의 온도 상승을 이용하여 폴리머 안정성에 관한 수치인 산화 시작 시간(OOT)을 측정할 수도 있습니다. OIT와 OOT 테스트 모두 고압 DSC를 이용해 실시할 수도 있는데, 이렇게 하면 안정제 소모를 가속시켜 테스트 시간이 단축됩니다.
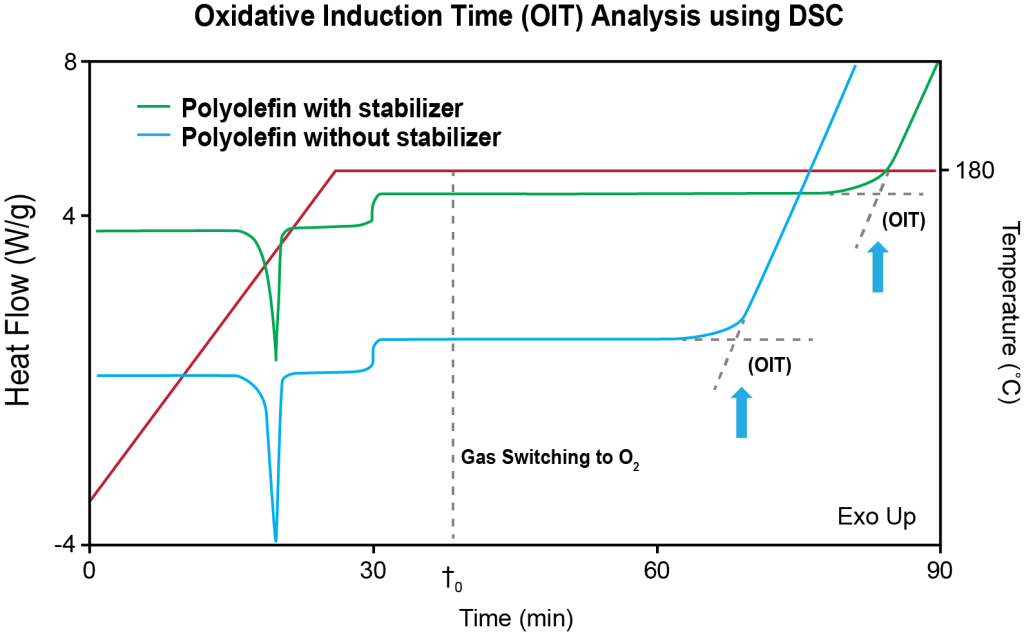
DSC에서 실시한 OIT 및 OOT 결과로 다음 질문에 답해보세요.
- 공급 원료 평가: 이 수지는 이대로 가공할 수 있는가? 추가 안정제로 산화방지제가 필요한가?
- 실패 분석: 충분한 양을 사용한 부품 산화방지제가 최종 사용 조건에 적합한가?
- 수명 종료 후 재활용: PCR 배치의 안정화와 가공을 위해 어느 정도의 산화방지제가 필요한가?
관련 응용 분야 정보:
수지가 어떻게 흐르는가?
폴리머 용융의 점성 및 점탄성 거동은 사출 성형과 압축 기법을 이용해 폴리머를 가공할 때 중요한 역할을 담당합니다. 기본적으로 점성은 흐름에 대한 재료 내부의 저항입니다. 점성이 높은 수지는 느리게 흐르고 몰드를 채우는 데 많은 시간이 걸리므로 사이클 타임이 증가하고 미성형 같은 결함 가능성이 발생할 수 있습니다. 결과적으로 수지의 점성을 측정하고 세심하게 통제해야 가공 안정성을 보장하고 배치 간 변동성을 제거할 수 있습니다.
폴리머 용융의 경우 전단 속도라고도 하는 변형 속도에 따라 점성 프로파일이 좌우됩니다. 전단 속도가 증가하면 점성이 감소하므로 압출과 사출 성형 공정에서 높은 전단 속도를 마주하면 멱승법 영역에서 점성 곡선이 전단 박화 거동을 표시합니다. 이와 같은 전단 속도 의존성은 폴리머의 분자 중량 분포와 분기 정도의 영향을 받습니다.
높은 전단 속도는 가공 조건과 관련이 있지만 낮은 전단 속도에서 점성을 측정하는 것은 수지의 분자 구조를 드러내는 데 필수적입니다. 1차 뉴턴 영역에서 0 전단 점성은 수지의 분자 중량과 직접적인 상관관계가 있고 회전 레오미터로 측정할 수 있습니다.
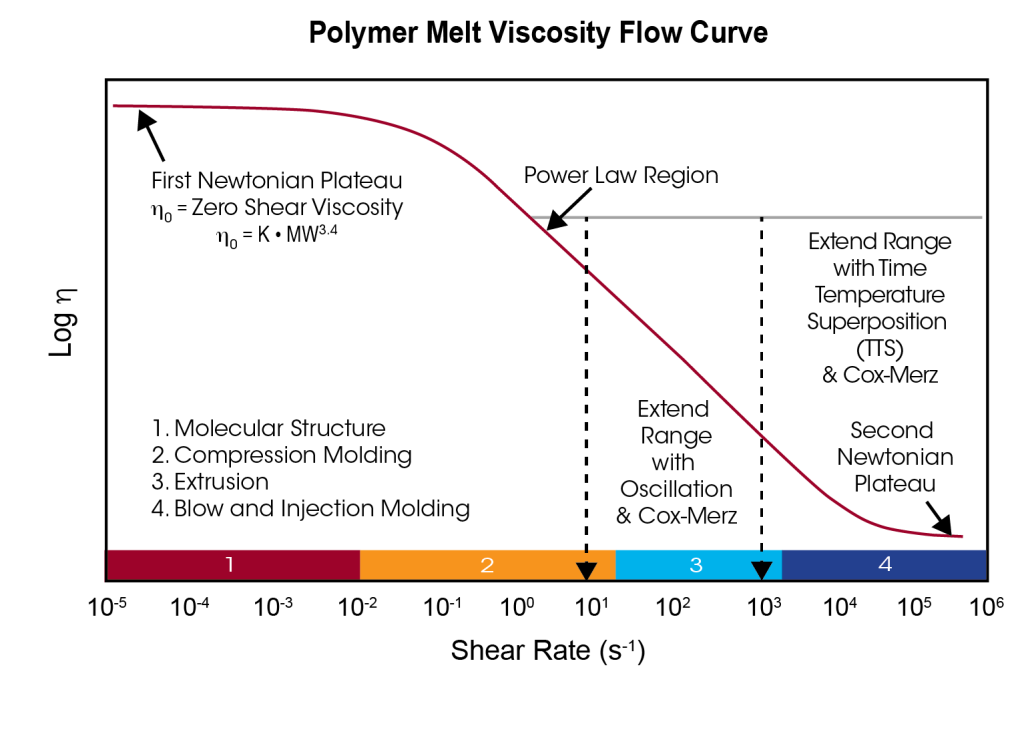
점탄성은 분자 중량/분자 중량 분포와 어떤 관계가 있는가?
회전 레오미터의 진동 테스트는 다양한 시간 범위에서 작은 변형을 통해 폴리머 구조를 조사함으로써 폴리머의 점탄성에 대한 귀한 인사이트를 제공합니다. 그 결과 진동 주파수의 함수로 폴리머의 저장 탄성률(G’), 손실 탄성률(G”), 복소 점도(η*)를 알 수 있으며 이를 이용해 폴리머 완화의 동력을 더욱 잘 이해할 수 있습니다. 이러한 변수는 수지의 분자 중량, 분자 중량 분포, 긴 사슬 분기 구조 등의 영향을 많이 받습니다. 용융 흐름 인덱서 또는 모세관 유동학과 비교할 때 회전 유변물성 테스트에서 얻은 점탄성 프로파일은 높은 분자 중량 오염의 존재에 특히 민감하여 가공 문제를 야기할 수 있습니다.
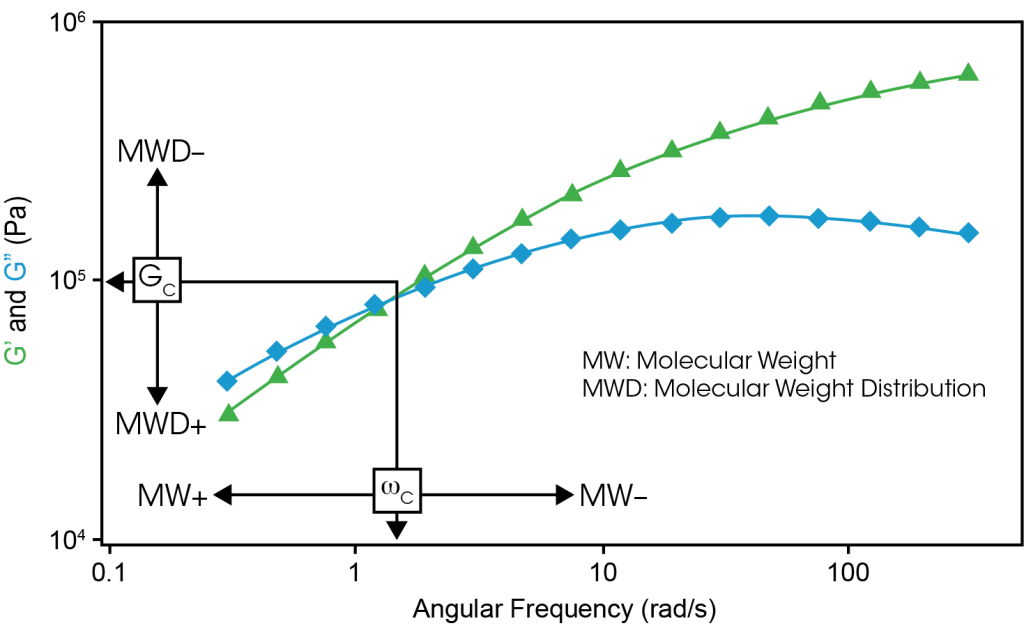
회전 레오미터에서 실시한 점성 및 점탄성 측정으로 다음 질문에 답해보세요.
- 공급 원료 평가: 수지의 분자 중량/분자 중량 분포에서 배치별 변동은 점탄성 프로파일에 어떤 영향을 주는가?
- 가공성: 제조 공정과 관련 있는 모든 전단 속도에서 수지는 올바른 점성을 갖고 있는가?
- 수명 종료 후 재활용: 재활용 수지의 오염과 MW 변동은 가공에 어떤 영향을 주는가?