如何透過熱分析來最佳化 3D 列印材料
Jason Saienga | Gray Slough | Morgan Ulrich
May 30, 2022
3D 列印也稱為積層製造是一種多功能製造技術,它正被不同產業所接受。3D 列印可以快速製造原型,並依照需求來列印解決方案,以避免批次生產造成的浪費。
3D 列印在製造業中被廣泛採用,其中一個因素就是它具有可創造複雜形狀的獨特能力。許多標準的製造方法都無法在結構中建立孔腔和凹槽。而積層式方法可以輕鬆建立特殊的形狀。
現今 3D 列印正擴展到各種材料中,包括生物相容性聚合物和金屬。3D 列印甚至應用於醫療保健領域,列印客製化的醫療裝置。1
為了最佳化 3D 列印的材料,製造商需要仔細考量最終材料的機械和熱屬性。雖然 3D 列印元件通常比較輕,並且正確的聚合物元件組合可以有類似金屬的張力強度,但積層製造元件典型的低機械和熱屬性仍是其中一大挑戰。2
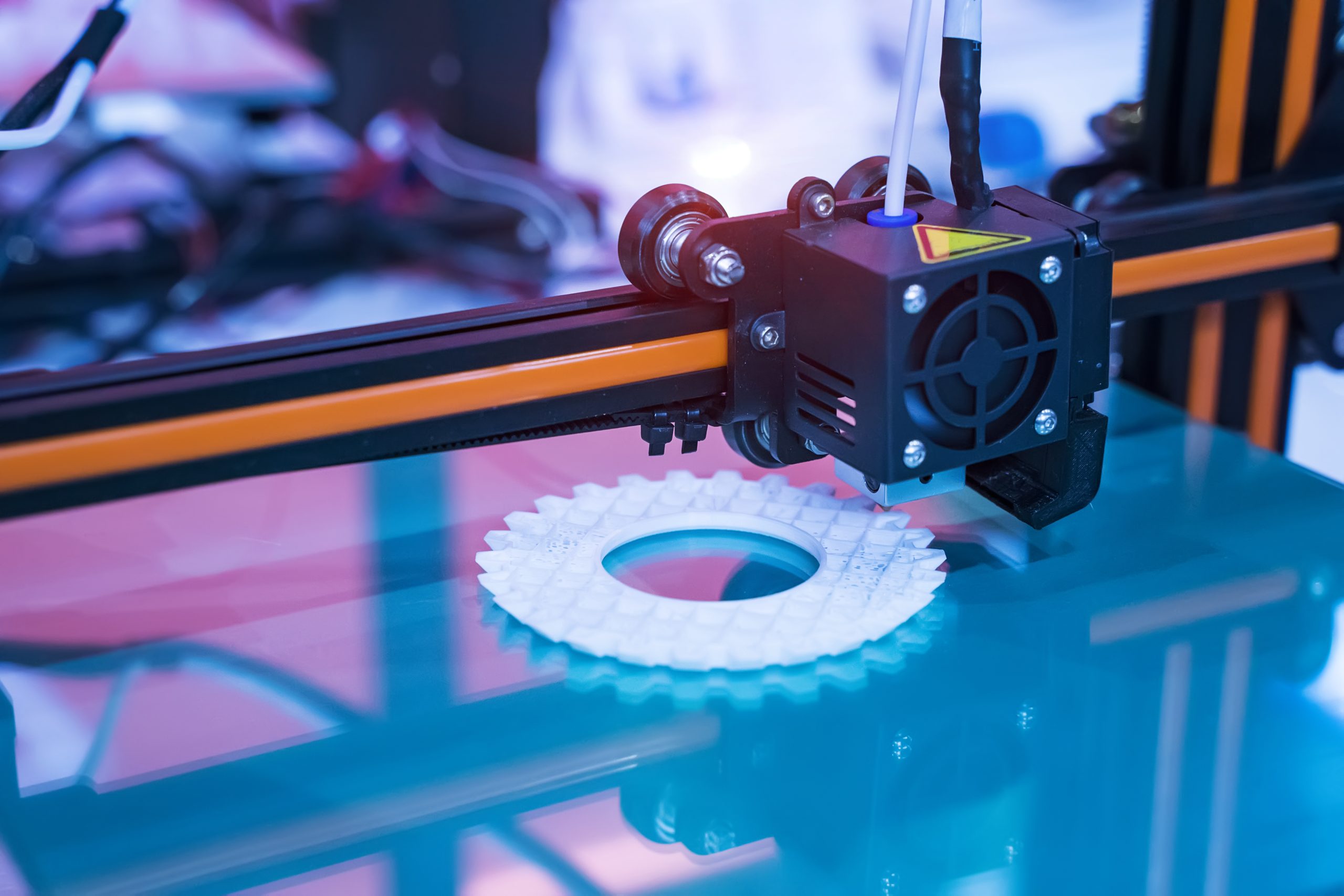
3D 列印產品屬性的加工最佳化
找出擠製過程中如何影響最終列印材料的屬性,是一個非常熱門的研究領域。汽車應用是對材料的伸張性和熱屬性要求最高的領域之一。
很幸運地,目前許多含有碳纖維、玻璃纖維和克維拉的熱塑性聚合物基質皆很適合 3D 列印元件,可以實現足夠的效能在汽車應用中。2
在 3D 列印過程中,列印的基材被融化然後分層沉積來形成最終的物件。在這個過程中有許多參數可以最佳化,例如聚合物的床層和噴嘴的溫度,以及各層之間的固化時間。
現在有許多 3D 列印的方法,包括選擇性激光燒結、生物列印和熔融沈積建模。其中熔融沈積建模是一種最常見的方法。
玻璃轉變溫度是決定正確溫度拉伸非晶態聚合物的必要資訊。對於半結晶性聚合物而言,熔化溫度是一個有趣的數值。結晶度對聚合物的機械屬性有很大的影響。
許多聚合物是用紫外線來固化,紫外線會在聚合物材料中產生自由基,這些自由基在生產最終聚合物的過程中成為交聯過程的引發劑。較高的交聯度通常會有更堅硬和牢固的材料。交聯產生的材料強度可經由改變樣品暴露在紫外線下時間的長短來改變。
溫度和固化時間都會影響聚合物在材料中的分子結構和屬性。因此,為了最佳化這些參數並探索它們對最終材料的影響,材料設計師會採用對聚合物屬性細節敏感的測試技術。
3D 列印材料的熱分析
研究擠製過程對最終材料屬性影響的主要熱分析工具,包括熱重分析 (TGA)、差示掃描量熱法 (DSC)、熱機械分析 (TMA) 和動態機械分析 (DMA)。3每種技術皆提供互補的資訊,結合起來可以對列印材料的屬性有更深的了解。
熱重分析測量材料的重量隨溫度或時間變化而變化的幅度和速度。TGA 對於表徵擠壓的影響非常有幫助,因為許多材料在加熱後會發生氧化或分解,重量就會跟著改變。4 熱重分析是確定樣品在擠壓過程的條件下是否會發生降解的最佳方法之一。
差示掃描量熱法是一種很有用的技術,用來測量材料中作為溫度函數放熱和吸熱的轉變 – 擠壓加工常見的興趣點包括玻璃轉變溫度、熔化溫度和材料的熱容量。
差示掃描量熱法和熱重分析是一種強大、互補的技術組合,用於了解擠壓的影響。這兩種技術結合在一起,可以用來分析聚合物在擠壓溫度下的熱屬性。3
熱機械分析用於測量熱膨脹係數 (CTE) 和玻璃轉變溫度,它是另一種互補技術。由於玻璃轉變溫度取決於材料的熱歷程,熱機械分析是檢查擠製過程是否會讓成品物件帶來不必要的機械行為的一個好方法。 此外,根據相對於纖維方向的測量方向,增強材料的 CTE 可能會表現出各向異性。3
動態機械分析也被廣泛用於材料工程,用於分析聚合物複合材料,因為它可以發現材料在動態載入條件下的行為資訊。5 DMA 對於表徵3D 列印成品元件特別有幫助,反映不同的規劃和加工方法如何影響最終使用效能。
選擇正確的 3D 列印熱分析技術
大多數 3D 列印製造生產線都依賴上述的技術組合。作為熱分析領域的全球領導者,TA Instruments 是世界各地積層製造的首選儀器供應商。
我們幫助不同產業的使用者,為他們獨特的 3D 列印挑戰和目標找到適合的儀器和方法。我們提供一系列領先業界的熱分析儀器,這些儀器都設計易於使用且高效率。TA Instruments 全方位的熱分析產品系列擁有所有必要的設備,可以讓您完全表徵基材的熱屬性和機械屬性。
立即與我們的專家聯繫,以了解 TA Instruments 各種熱分析和機械分析儀器如何提升您 3D 列印產品的品質。
參考文獻:
- Trenfield, S. J., Awad, A., Madla, C. M., Hatton, G. B., Goyanes, A., Gaisford, S., Basit, A. W., Trenfield, S. J., Awad, A., Madla, C. M., & Hatton, G. B. (2019). Shaping the future: recent advances of 3D printing in drug delivery and healthcare. Expert Opinion on Drug Delivery, 16(10), 1081–1094. https://doi.org/10.1080/17425247.2019.1660318
- Mohammadizadeh, M., & Fidan, I. (2019). Thermal Analysis of 3D Printed Continous Fiber Reinforced Thermoplastic Polymers for Automotive Applications. Solid Freeform Fabrication 2019: Proceedings of the 30th Annual International Solid Freeform Fabrication Symposium – An Additive Manufacturing Conference, 899–906. https://utw10945.utweb.utexas.edu/sites/default/files/2019/078%20Thermal%20Analysis%20of%203D%20Printed%20Continuous%20Fiber%20Re.pdf
- Billah, K. M., Lorenzana, F. A. R., Martinez, N. L., Chacon, S., Wicker, R. B., & Espalin, D. (2019). Thermal Analysis of Thermoplastic Materials Filled with Chopped Fiber for Large Area 3D Printing. Solid Freeform Fabrication 2019: Proceedings of the 30th Annual International Solid Freeform Fabrication Symposium – An Additive Manufacturing Conference, 892–898. https://utw10945.utweb.utexas.edu/sites/default/files/2019/077%20Thermal%20Analysis%20of%20Thermoplastic%20Materials%20Filled.pdf
- TA Instruments (2022) 3D Printing Webinar, https://www.tainstruments.com/3-d-printing-and-additive-manufacturing-process-optimization-a-thermal-approach/, accessed May 2022
- Saba, N., Jawaid, M., Alothman, O. Y., & Paridah, M. T. (2016). A review on dynamic mechanical properties of natural fibre reinforced polymer composites. Construction and Building Materials, 106, 149–159. https://doi.org/10.1016/j.conbuildmat.2015.12.075